Program
Timetable (Updated on November 20)
Final Program (Updated on November 22)
Keynote Sessions
Keynote Sessions 1
- Time & Date:
- 10:00-12:15, Wednesday, November 27
- Room:
- Room A
- Chair:
- Kan Akatsu (Yokohama National University, Japan)
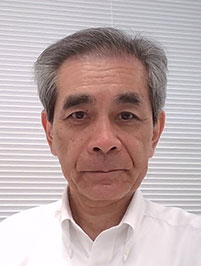
KS1-1
Superconducting Maglev and Chuo Shinkansen
Dr. Junichi Kitano
Central Japan Railway Company, Japan
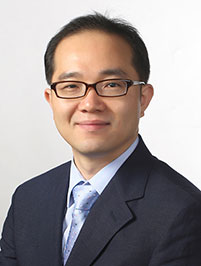
KS1-2
Research on Power Electronics Technology for Future Power Grid
Professor Rae-Young Kim
Hanyang University, Korea
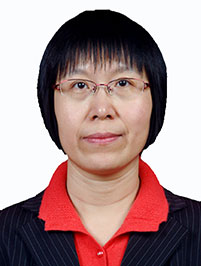
KS1-3
Research on Permanent-Magnet Synchronous Machines with Hybrid Utilization of Permanent Magnets
Professor Ping Zheng
Harbin Institute of Technology, China
Keynote Sessions 2
- Time & Date:
- 14:30-16:00, Wednesday, November 27
- Room:
- Room A
- Chair:
- Akira Chiba (Institute of Science Tokyo, Japan), Takashi Kosaka (Nagoya Institute of Technology, Japan)
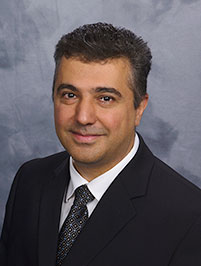
KS2-1
High Performance Integrated Motor Drives Using Wide Bandgap Devices Including Current Source Inverter
Professor Bulent Sarlioglu
University of Wisconsin-Madison, USA
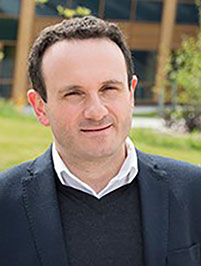
KS2-2
Design and Manufacturing of MW-class High Performance Electrical Machines
Professor Chris Gerada
University of Nottingham, UK
Due to various circumstances, Professor Li's lecture has been canceled. We are pleased to announce that Professor Rae-Young Kim from Hanyang University will be giving a lecture instead. Further details will be provided soon.
Organized Session
Organized Session 1
The session "Rotating Machines for Traction and Propulsion Applications" highlights recent advancements in electric vehicles (EVs) and aircraft electrification.
In the first presentation, Nissan introduces four key initiatives to reduce dependence on rare-earth materials in EV motors: heavy rare-earth reduction, magnet recycling, rare-earth-free magnet development, and the creation of an Externally Excited Synchronous Motor (EESM).
The second presentation discusses the development of a high-speed, lightweight motor prototype aimed at miniaturization and enhanced power density. This prototype achieves a maximum rotational speed of 34,000 rpm, reducing motor weight by 54% and doubling power density compared to traditional 50 kW-class motors.
In the third presentation, a novel motor drive system is proposed to streamline EV design by integrating both AC and DC charging functions, which reduces part count and improves overall efficiency. This system shows promising results in tests, with a 99.5% power factor for AC charging and doubled output voltage for DC charging.
The fourth presentation focuses on a direct-drive in-wheel motor utilizing a Halbach magnet array,
which enables high torque at lower speeds and increases interior space efficiency. This system
effectively cools the motor without a notable increase in fluid friction.
The fifth presentation showcases a hybrid electric motor designed for aircraft, aimed at MW-class
output. The prototype demonstrates a maximum output of 365 kW in tests, showing potential for MW-scale
propulsion systems in aviation.
Together, these advancements contribute significantly to the development of sustainable, high-performance rotating machines for traction and propulsion applications.
- Time & Date:
- 9:30-11:35, Thursday, November 28
- Room:
- Room A
- Chair:
- Kenji Nakamura (Tohoku University, Japan), Kyohei Kiyota (Institute of Science Tokyo, Japan)
Rotating Machines for Traction and Propulsion Applications
- OGS1-1
- Motor Initiatives Aimed at Reduction of Rare-earth Usage
- Shunji Oki, Nissan Motor Co., Ltd., Japan
- OGS1-2
- Development of High Power-Density Motors for Electric Axles using Nd-Based Bonded Magnets
- Masahiro Kayano, Aichi Steel Corporation, Japan
- OGS1-3
- Integration of Motor Drive and Charger System with Two-phase Motor and H-Bridge Inverter for Electric Vehicle
- Soumei Nakatomi, Honda R&D Co., Ltd., Japan
- OGS1-4
- Increasing the Power Density of In-wheel Motor using Direct-drive Technology
- Makoto Ito , Hitachi, Ltd., Japan
- OGS1-5
- Development of a Megawatt-Class Engine Embedded Electric Machine for Aircraft Electrification
- Tomoya Yamamoto, IHI Corporation, Japan
Organized Session 2
As electrification progresses in fields such as automobiles and aircraft, there is a need for smaller and lighter motor drive systems. Increasing the speed of the motor is effective in reducing the size of the motor drive system. However, there are many challenges specific to high-speed motors, such as mechanical strength, efficiency, and computation time. Therefore, in this special session, we will propose motor design and drive systems compatible with high-speed motor drive systems.
- Time & Date:
- 14:30-16:10, Thursday, November 28
- Room:
- Room A
- Chair:
- Junichi Asama (Shizuoka University, Japan), Gilsu Choi (Inha University, Korea)
High Speed Motors and Drives
- OGS2-1
- Adaptive Linear Neuron-based Active Disturbance Rejection Control System for Current Harmonics Suppression of PMSM Drives
- Christpher Lee, Nanyang Technological University, Singapore
- OGS2-2
- MW-class electric propulsion : Geared or Direct Drive?
- David Gerada, University of Nottingham, UK
- OGS2-3
- Evaluation of AC Copper Loss in High-Speed & High-Power Electric Machines
- Takehiro Jikumaru, IHI Corporation, Japan
- OGS2-4
- Impact of Current Sensor System Dynamics on Current Measurements and Novel Compensation Scheme on dq-Reference Frame
- Bulent Sarlioglu, University of Wisconsin-Madison, USA
Organized Session 3
Currently, variable speed drive technology for AC motors is widely used in home appliances, industry, and transportation. Furthermore, recent motor drives are required to realize multiple technical requirements, such as high efficiency under multiple conditions. For example, motor drives that achieve both current harmonic regulation (IEC61000-3-2) and low cost, high efficiency, and high reliability, and both low-speed high-torque and high-speed low-torque regions. In this special session, we will propose power conversion technologies to meet multiple technical requirements for AC motors.
- Time & Date:
- 9:30-11:35, Friday, November 29
- Room:
- Room A
- Chair:
- Hitoshi Haga (Shizuoka University, Japan), Shohei Komeda (Tokyo University of Marine Science and Technology, Japan)
Power Conversion Technology for Multiple Objectives in Motor Drives
- OGS3-1
- Buck-Boost Operation by Zero-Sequence Current Control for Negative-Point-Connected Dual Inverter with Variable Voltage Capacitor
- Akihito Mizukosh, Kisarazu College, Japan
- OGS3-2
- Transition and Latest Technology of Power Electronics for Air Conditioners
- Shinya Shimizu, Carrier Japan Corporation, Japan
- OGS3-3
- A Novel Single-Phase AC Power Supplied Dual-Inverter Topology with Integrated Rectifier
- Taiju Sakurai, Shizuoka University, Japan
- OGS3-4
- Zero-Sequence Current Ripple Reduction Control in Open-End Winding Interior Permanent-Magnet
- Yushi Araki, Sanden Corporation, Japan
- OGS3-5
- [JIA-to-ICEMS] Online Cell Capacitance and ESR Monitoring Using Switching Frequency in a Modular Multilevel Converter
- Kazunori Hasegawa, Kyushu Institute of Technology, Japan
Special Sessions
Special Session 1
A magnetic bearing is a mechanical element which supports a rotating shaft without any mechanical contact by magnetic force. A bearingless motor is defined as a rotating machine that combines magnetically integrated bearing function. Due to non-contact operation, these are applied to ultra-high speed and contamination-free drives, such as turbo-molecular pump, turbo-compressor, ventricular assist devices, semiconductor manufacturing devices. This session focuses on recent technologies and related topics of magnetic bearings and bearingless motors.
- Time & Date:
- 16:20-18:00, Wednesday, November 27
- Room:
- Room G
- Chair:
- Junichi Asama (Shizuoka University, Japan), Victor Tedesco (The Texas Heart Institute, USA)
Bearingless Motors and Drives
- SS1-1
- Comparison of High Pole Number Bearingless Motors with Irregular Distribution of Stator Slots
- Hiroya Sugimoto, Tokyo Denki University, Japan
- SS1-2
- Decoupling Force and Torque Generation in Bearingless Motors with Toroidal Windings
- Wolfgang Gruber, Johannes Kepler University, Austria
- SS1-3
- Development of a Bearingless PM Motor with Axial Magnetic Suspension Using Zero-Sequence Current
- Yusuke Fujii, Tokyo Institute of Technolog, Japany
- SS1-4
- Design, Modelling and Performance Evaluation of a Single-Phase Passively Levitated Self-Bearing Machine
- Joachim Van Verdeghem, UC Louvai, Belgiumn
Special Session 2
In order to reduce copper loss in rotating machines, a motor (Magnet Reversal Motor) that is driven by pulse current instead of sinusoidal current drive is introduced in this session. MRM is realized by a Flux Switching Motor, which is equipped with a variable magnet and is driven by changing the polarity of the magnet by a high pulse current. In this session, the structure and characteristics of MRM and its driving method such as main circuit, inverter module, and gate drive circuit with over current protection will be presented.
- Time & Date:
- 14:30-16:10, Thursday, November 28
- Room:
- Room G
- Chair:
- Kan Akatsu (Yokohama National University, Japan)
Current Pulse Driven Motor and Its Driving Circuit
- SS2-1
- High Pulse Current IGBT Power Module for MRM Drive
- Ichiro Omura, Kyushu Institute of Technology, Japan
- SS2-2
- A Novel Magnet Reversal Motor (MRM) Driven by High Pulse Current for Copper Loss Reduction
- Kan Akatsu, Yokohama National University, Japan
- SS2-3
- High Pulse and Sinusoidal Current Output Inverter for MRM Drive
- Keiji Wada, Tokyo Metropolitan University, Japan
- SS2-4
- Gate Driver IC With Fully Integrated Overcurrent Protection for Driving Magnet Reversal Motor With High Pulse Current
- Makoto Takamiya, The University of Tokyo, Japan
Industry Session
Only this Session on November 26 is a admission free event that does NOT
require pre-/on-site registration.
We look forward to welcoming everyone who are involved or interested in this field.
This session will provide the audience cutting edge application cases of motor, motor drive, and power electronics technical field. Two of cases of a home apparatus application and a railway vehicle traction application, which are published in Journal of Industrial Application (JIA) of IEEJ, "Cool Japan" issues, are presented in this session.
- Time & Date:
- 15:00-16:30, Tuesday, November 26
- Room:
- Room A
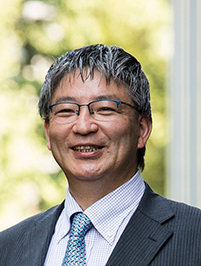
Moderator
Keiichiro Kondo
Waseda University
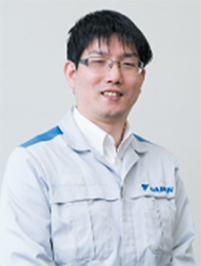
[JIA-to-ICEMS] Inverter Air Conditioner Promotion by Developing a High Power Density Motor Drive System
Nobuo Hayashi
Daikin Industies, LTD
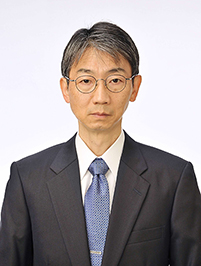
[JIA-to-ICEMS] Outstanding Technical Features of Traction System in N700S Shinkansen New Generation Standardized High Speed Train
Kenji Sato
Central Japan Railway Company
Technical Sessions
November 27 (Wed.), 2024
Session PS1-1Permanent Magnet Machines 4
- Time:
- 13:00-14:00
- Venue:
- FIT Arena
- PS1-1-1
- Experimental Investigation on the Influence of a Hollow Rotor Shaft Cooling and Oil Properties on No-load Losses in Traction Electric Machines
- A. Gilson, R. Sindjui, G. Bourhis, and G. Zito
- IFP Energies nouvelles, France
- PS1-1-2
- Novel Refrigerant Cooling Method for Traction Motor Thermal Management
- Sun Lee1, Andrew Botham1, Jigar Mistry2, Reza Nasirizarandi2, and Narayan C. Kar1
- 1University of Windsor, Canada, 2R&D Americas, Schaeffler, Canada
- PS1-1-3
- Analysis and Desing of IPMSM for Reducing AC Copper Loss in EV Traction Motor
- Chang-Hyeon Wang, Ho-Jin Oh, Han-Joon Yoon, Nam-Ho Kim, and Sang-Yong Jung
- Sungkyunkwan University, Republic of Korea
- PS1-1-4
- Impact of Leakage Flux on Permanent Magnet Synchronous Machines in Traction Drives Using 2D and 3D Finite Element Analysis Comparative Study
- Ioannis Thomidis, Walaa Chliouet Benaboud, and Rik W. De Doncker
- RWTH Aachen University, Germany
- PS1-1-5
- Experimental Validation of a Prediction Method for Bearing Currents in Traction Drive Systems
- Lennart Jünemann, Pauline Höltje, Bernd Ponick, and Axel Mertens
- Leibniz University Hannover, Germany
- PS1-1-6
- Rotor Design Considering Demagnetization Characteristics of Ribless IPMSM for EV Propulsion
- In-seok Song, Ho-Jin Oh, DoHyun Jang, and Sang-Yong Jung
- Sungkyunkwan University, Republic of Korea
- PS1-1-7
- Review of High Torque Density Permanent Magnet Machines for Electric Propulsion System
- Yanlei Yu1, Feng Chai2, and Christopher H. T. Lee1
- 1Nanyang Technological University, Singapore, 2Harbin Institute of Technology, China
- PS1-1-8
- Optimisation of Permanent Magnet Synchronous Motor for Electric Vehicles
- Pengbo Ming, Jun Di, Shifan Luo, Weili Li, and Junci Cao
- Beijing Jiaotong University, China
- PS1-1-9
- Optimization Study of Torque in the IPMSM for E-bike Application
- Jinming Hu1, Fei Zhao1, Zeting Mei2, Jing Wang2, and Dezhi Chen3
- 1Harbin Institution of Technology, China, 2Shenzhen Sailvan Network Technology Co., Ltd., China, 3Shenyang University of Technology, China
Session PS1-2Permanent Magnet Machines 5
- Time:
- 13:00-14:00
- Venue:
- FIT Arena
- PS1-2-1
- Design and Optimization of an Outer-rotor PMSM for Torque Ripple Minimization
- Gwan-Hui Jang1, Sehwan Kim2, and Gilsu Choi1
- 1Inha University, Republic of Korea, 2Korea Institute of Machinery and Materials, Republic of Korea
- PS1-2-2
- Comparative Analysis of Torque Ripple in IPMSM Topologies using the Frozen Permeability Method
- Ho-Jin Oh, Yongmin Kim, Chang-Hyeon Wang, and Sang-Yong Jung
- Sungkyunkwan University, Republic of Korea
- PS1-2-3
- Fault-tolerant Control Method to Reduce Torque Ripple for Symmetrical Winding Multi-phase Brushless DC Motor Under Open-circuit Faults
- Lixiang Zhu, Wei Chen, Xinmin Li, and Zhiqiang Wang
- Tiangong University, China
- PS1-2-4
- An Optimization Design for Reducing Cogging Torque in Permanent Magnet Synchronous Motors
- Feiyang Liu, Jinglin Liu, and Yuyuan Yang
- Northwestern Polytechnical University, China
- PS1-2-5
- Investigation and Analysis of Cogging Torque for Axial Flux Permanent Magnet Machines
- Yanbo Lu1,2, Chen Wang1,2, and Jian Huang1,2
- 1Key Laboratory of Anhui Province, China, 2Anhui Polytechnic University, China
- PS1-2-6
- Study of Rotor Slotting on Cogging Torque of Spoketype Permanent Magnet Machine
- Haolin Shu1,2, Ming Jiang1,2, and Chen Wang1,2
- 1Key Laboratory of Anhui Province, China, 2Anhui Polytechnic University, China
- PS1-2-7
- Reduction of Axial Magnetic Force and Starting Current in Single-sided Axial-flux Machine with Ring PM Unit and Flux-weakening Control
- Ryuga Koyanagi1, Hiroya Sugimoto1, Akihiro Ochiai2, and Tadashi Sato2
- 1Tokyo Denki University, Japan, 2Ebara Corporation, Japan
- PS1-2-8
- Vibration and Noise Analysis and Suppression of High Torque Density Permanent Magnet Motor
- Baoxin Li1, Ziheng Yin1, Ruiwu Cao1, Kai Wang1, and Zheng Wang2
- 1Nanjing University of Aeronautics and Astronautics, China, 2Southeast University, China
- PS1-2-9
- Unbalanced Magnetic Radial Pull During Module Open Circuit Fault in a Multi-modular, High Voltage PM Synchronous Direct Drive Generator for Offshore Wind
- Pål Stabel Keim, Casper Leonard Klop, Lorrana Faria da Rocha, Runar Mellerud, Arne Nysveen, and Robert Nilssen
- Norwegian University of Science and Technology, Norway
Session PS1-3Permanent Magnet Machines 6
- Time:
- 13:00-14:00
- Venue:
- FIT Arena
- PS1-3-1
- Multi-objective Optimization of a Novel Permanent Magnet Starter-generator
- Haoquan Zhang, Baoquan Kou, He Zhang, and Junren Mu
- Harbin Institute of Technology, China
- PS1-3-2
- Multi-objective Optimization for a Low-speed Hightorque Permanent Magnet Motor
- Ziheng Yin1, Baoxin Li1, Ruiwu Cao1, Kai Wang1, and Zheng Wang2
- 1Nanjing University of Aeronautics and Astronautics, China, 2Southeast University, China
- PS1-3-3
- Analytical Modeling and Optimization of Three-segment Halbach Permanent Magnet Array High Lift Motor
- Maixia Shang, Jinglin Liu, Xiaobao Chai, and Mengqi Li
- Northwestern Polytechnical University, China
- PS1-3-4
- Optimization Design Research of Dual-airgap Hightorque Permanent Magnet Motor Based on Coevolution Algorithm
- Yingjie Xu1, Siyang Yu1, Yue Zhang2, Hongkui Zhang1,3, and Fengge Zhang1
- 1Shenyang University of Technology, China, 2Shandong University, China, 3 CCTEG, China
- PS1-3-5
- Improved IPM Motor Design with Integrated Ribs for Stress Reduction and Weight Optimization
- Lucio José Fernando Cáceres Vera1, Min-Fu Hsieh1, and Guan-Ming Chen2
- 1NCKU, Taiwan, 2China Steel Corporation, Taiwan
- PS1-3-6
- Back EMF Waveform Optimization of Hybrid Less Rareearth Synchronous Reluctance Motor Using PSO Algorithm
- Ziyu Wang1, Xiaolin Wang1, Qixing Gao2, and Fanghua Zhang1
- 1Nanjing University of Aeronautics and Astronautics, China, 2Yanshan University, China
- PS1-3-7
- Cost Optimization Method for Less-rare-earth Permanent Magnet Synchronous Motor Based on Surrogate Model
- Biao Wang, Guangwei Liu, Zhenyao Xu, and Fengge Zhang
- Shenyang University of Technology, China
- PS1-3-8
- Design Proposal Based on Characteristic Analysis of Permanent Magnet Utilization Ratio in Dual Rotor IPMSM
- Jae-Hyeong Park1,2, Sung-Bae Jun2, Tae-Yong Lee2, Minyeong Choi2, Sanghoon Moon2, and Sang-Yong Jung1
- 1Sungkyunkwan University, Republic of Korea, 2Hyundai Motor Company, Republic of Korea
Session PS1-4Permanent Magnet Machines 7
- Time:
- 13:00-14:00
- Venue:
- FIT Arena
- PS1-4-1
- Magnet Reduction Effect of Split Rotor and Nonmagnetic Wedge in V-shaped Interior Permanent Magnet Motor
- Takuhiro Uzawa and Yuki Hidaka
- Nagaoka University of Technology, Japan
- PS1-4-2
- Investigation of Angle Displacements in a Novel Dualthree-phase Equinumerous-slot-pole PMSM
- Yongtao Liang1, Zaixin Song1, Yidan Ma1,2, Yujie Chen1, and Xiaoyu Lang1
- 1The Hong Kong Polytechnic University, China, 2Xi’an Jiaotong University, China
- PS1-4-3
- Design and Performance Analysis of a Novel Permanent Magnet Synchronous Motor with Stepped Magnetic Poles
- Jinjin Duan, Zhihui Chen, Jiajun Zhu, and Hongxi Hu
- Nanjing University of Aeronautics and Astronautics, China
- PS1-4-4
- A Novel Permanent Magnet Synchronous Machines with Improved Magnetic Field Characteristics and Performance Analysis
- Xiaoyu Liang, Yuhong Zheng, Mingqiao Wang, Yong Liu, Ping Zheng, Wei Liu, and Minghao Wang
- Harbin Institute of Technology, China
- PS1-4-5
- Design and Analysis of Fractional-slot Concentrated Winding PMSMs with Unequal Tooth Towards Improving Torque Density
- Zicheng Yin, Xiaoyan Huang, and Ang Liu
- Zhejiang University, China
- PS1-4-6
- A Novel Two Degrees-of-freedom Rotary-linear Permanent Magnet Machine
- Peixin Wang, Heyang Liang, Jikai Si, Rui Nie, and Shuai Xu
- Zhengzhou University, China
- PS1-4-7
- Design and Analysis of a Rotor-coreless Multi-disk Axial Flux Permanent Magnet Motor with Unaligned Permanent Magnets
- Qiyu Guo, Wenliang Zhao, Ning Wang, Yan Ren, and Xiuhe Wang
- Shandong University, China
- PS1-4-8
- Design and Analysis of Permanent Magnet Synchronous Motor Based on Asymmetric Auxiliary Teeth for Rotor Mechanical Position Self-sensing Technology
- Xiaogang Lin1, Zheng Zeng1, Yuwei Zhao1,2, and Wei Xie1
- 1Chinese Academy of Sciences, China, 2University of Chinese Academy of Sciences, China
- PS1-4-9
- Electromagnetic Performance Comparison of Dual-rotor Permanent Magnet Motor with Three Different Rotor Topologies
- Yu Fu, Jing Wang, and Weiwei Geng
- Nanjing University of Science and Technology, China
Session PS1-5Permanent Magnet Machines 8
- Time:
- 13:00-14:00
- Venue:
- FIT Arena
- PS1-5-1
- Research of the Variable Frequency Compressor Motor Based on Air Grooves of Rotor Yoke
- Yusheng Hu1,2,3, Xumin Zhao1,2,3, Bo Zhou3, Hui Zhang3, Qitao Li3, and Zhongpeng Xu3
- 1State Key Laboratory of Air Conditioning Equipment and System Energy Conservation Zhuhai, China, 2Guangdong Key Laboratory of Refrigeration Equipment and Energy Conservation Technology, Inc., China, 3Gree electric appliances, inc. of zhuhai, China
- PS1-5-2
- Design of an Adjustable-performance Internal Permanent Magnet Motor for DC Inverter Compressors used in Air-conditioning Systems
- Chia-Sheng Chiang2, Kai-Yi Huang1, Ming-Tsung Chiu1, Yao-Yang Hsieh1, and Chung-Ming Lin1
- 1New Widetech Industries Co., Ltd., Japan 2Tokai University, Japan
- PS1-5-3
- Research on Design and Electromagnetic Characteristics Analysis of Super Premium Efficiency (IE4) Permanent Magnet Assisted Synchronous Reluctance Motor for Rare Earth Permanent Magnet Reduction
- Do Yun Kwon, Ki Won Kim, Tae Hoon Kwon, and Myung Jeong
- HD Hyundai Electric, Republic of Korea
- PS1-5-4
- High Slot Fill Aluminum Distributed Winding for Highspeed and High Power Density Electric Machines
- Yuto Yamada, Jun Ebinuma, and Hiroya Sugimoto
- Tokyo Denki University, Japan
- PS1-5-5
- Feasibility Analysis and Sizing for High-speed IPMSM Designs
- Guoyu Chu, Rukmi Dutta, John E. Fletcher, and M. F. Rahman
- UNSW Sydney, Australia
- PS1-5-6
- Rotor Stress Analysis for High-speed PM Machines Considering Fringe Effect
- Jiayue Zhou, Xi Xiao, and Hang Xu
- Tsinghua University, China
- PS1-5-7
- Design and Analysis of Fault-tolerant IPM Considering Bidirectional Electromagnetic-thermal Coupling Constraints
- Yiming Ma1, Xiangdong Su2, Zhenxiao Yin2, Yujia Zhang2, and Hang Zhao2
- 1CSG (China Southern Grid), China, 2The Hong Kong University of Science and Technology (Guangzhou), China
- PS1-5-8
- Investigation of Multi-phase Electric Motors Having the Same Electromagnetic Structure Considering Performance Trade-off
- HyeonMyeong Woo, Sangjin Lee, Yechan Park, Sangmin Lee, and Cheewoo Lee
- Pusan National University, Republic of Korea
- PS1-5-9
- Pulsation Reducing Effect in DC Current and Torque for Motor Fault-tolerance Based on Second Order Component Power Cancelation
- Sota Takahashi and Yuki Hidaka
- Nagaoka University of Technology, Japan
Session PS1-6PM Machine Control and Drives 1
- Time:
- 13:00-14:00
- Venue:
- FIT Arena
- PS1-6-1
- Improved MTPA Control Strategy with Adaptive Gain for Permanent Magnet Synchronous Reluctance Motors
- Jun Huang1, Bo Wang1, Haoyuan Yu1, and Dewen Tian2
- 1Southeast University, China, 2China North Vehicle Research Institute, China
- PS1-6-2
- Modified Virtual Signal Injection Control of MTPA for IPMSM Considering Switching Operating Conditions
- Guidan Li, Xufeng Rui, Bin Li, Xiaochen Ma, and Yulu Ling
- Tianjin University, China
- PS1-6-3
- Accurate MTPA Control Based on Ferrari Method for IPMSM with Partial Derivative Term Calculation
- Yiyang Li1,2, Xin Gu1,3, Zhiqiang Wang1,3, Liyan Guo1,3, Wei Chen1,3, Xinmin Li1,3, and Chen Li4
- 1Tiangong University, China, 2Tianjin Key Laboratory of Intelligent Control of Electrical Equipment, China, 3National Local Joint Engineering Research Center, China, 4Zhejiang University, China
- PS1-6-4
- A Loss Minimization Dynamic-static Transition Control Strategy Based on Model Predictive Current Control for IPMSMs
- Cheng Song1, Jinhua Du1,2, Guoqiang Zhang1, Boyan Zhang1, Han Wu1, and Geping Xu3
- 1Xi’an Jiaotong University, China, 2Shaanxi Province Key Laboratory of Smart Grid, China, 3Xi’an XiChi Electric Co., Ltd., China
- PS1-6-5
- Position Offset Injection based Fast and Accurate Maximum Torque Per Ampere (MTPA) Control of Interior PMSMs
- Zhe Tong1, Fengyu Wang1, Yuting Lu1, Beichen Ding1, and Guodong Feng1,2
- 1Sun Yat-sen University, China, 2Guangdong Provincial Key Laboratory of Fire Science and Intelligent Emergency Technology, China
- PS1-6-6
- Auto Associative Kernel Regression Data-driven Method for Permanent Magnet Synchronous Motor Control
- Hang Xu, Xi Xiao, and Jiayue Zhou
- Tsinghua University, China
- PS1-6-7
- Comparative Analysis of PID, Self-tunning PID, and Adaptive Neuro-fuzzy Logic Inference System Controllers for BLDC Motor Speed Control
- Theeraphong Srichiangsa, Piyapath Siratarnsophon, Sirichai Wattanasophon, and Sarinee Ouitrakul
- Kasetsart University, Thailand
- PS1-6-8
- IPOA-NLADRC Based Permanent Magnet Synchronous Motor Control Strategy
- Shanyong Xu1, Youqing Ma1, Yourui Huang1,2, and Tao Han1
- 1Anhui University of Science and Technology, China, 2West Anhui University, China
Session PS1-7PM Machine Control and Drives 2
- Time:
- 13:00-14:00
- Venue:
- FIT Arena
- PS1-7-1
- Control Strategy for Small DC-link Capacitor Brushless DC Motor Drives Using a Single DC-link Current Sensor
- Hang Gao1, Xinmin Li1, Xin Gu1, Wei Chen1, and Changliang Xia1,2
- 1Tiangong University, China, 2Zhejiang University, China
- PS1-7-2
- An Open-winding Permanent Magnet Synchronous Motor Drive System Based on the CSI-VSI Hybrid Converter
- Run Zhou, Jiadan Wei, Zhihui Wang, Yidi Meng, and Zeyu Zhang
- Nanjing University of Aeronautics and Astronautics, China
- PS1-7-3
- Research on Fractional-order Active Disturbance Rejection Control Method for Permanent Magnet Synchronous Motor
- Enming Cui1, Yiguang Chen1, Ruxi Sun2, and Xiaolong Zhao1
- 1Tianjin University, China, 2Tianjin Huaneng Yangliuqing Power Co., Ltd., China
- PS1-7-4
- Multi-vector Model Predictive Control for Permanent Magnet Synchronous Motors with Disturbance Compensation
- Zhaoyi Wang1, Jialiang Dai1, Jungho Ahn1, Seungjoo Kim2, and Ju Lee1
- 1Hanyang University, Republic of Korea, 2Korea Testing Certification, Republic of Korea
- PS1-7-5
- An Improved Active Disturbance Rejection Control for Speed Control of Permanent Magnet Synchronous Motor Using Reduced-order Extended State Observer
- Xiaolong Zhao1, Yiguang Chen1, Ruxi Sun2, and Enming Cui1
- 1Tianjin University, China, 2Tianjin Huaneng Yangliuqing Power Co., Ltd., China
- PS1-7-6
- Improved Sliding Mode Control Strategy with Disturbance Compensation for PMSM Speed Regulation System
- Yong Zhao, Jingxiu Wu, Yong Kong, Qiang Liu, and Lei Zhang
- University of Nanjing Xiaozhuang, China
- PS1-7-7
- Current Sampling Error Suppression Method for Deadbeat Predictive Direct Speed Control Based on Quasi-resonant Controller
- Guodong Yu, Haoyi Mu, Shaobin Li, Xudong Bai, and Yongxiang Xu
- Harbin Institute of Technology, China
- PS1-7-8
- High-efficiency Drive Technology for High-speed, Multipole Motors with Minor Sampling Process
- Katsuya Haruki and Yoshitaka Iwaji
- Ibaraki University, Japan
- PS1-7-9
- Adaptive One Sample Ahead Preview Control for Non-Sinusoidal PMSM with dq Coordinate Implementation
- Guilherme V. Hollweg1, Lucas R. Rocha2, Van-Hai Bui1, Rodrigo P. Vieira2, Mengqi Wang1, and Wencong Su1
- 1University of Michigan-Dearborn, USA, 2Federal University of Santa Maria, Brazil
Session PS1-8Sensorless Control 1
- Time:
- 13:00-14:00
- Venue:
- FIT Arena
- PS1-8-1
- Rotor Position Error Compensation for Sensorless Control of SPMSM Based on BP Neural Network
- Linyi Shen1, Peiyu Yao1, and Guodong Feng1,2
- 1Sun Yat-sen University, China, 2Guangdong Provincial Key Laboratory of Fire Science and Intelligent Emergency, China
- PS1-8-2
- A Sensorless Control Method for an Open-phase Fivephase PMSM by Using Series-SOGI and an Adaptive Neutral-voltage Compensation
- Jie Chen1, Bing Tian1, Yingzhen Li2, and Qiming Bai3
- 1Nanjing University of Aeronautics and Astronautics, China, 2China Industrial Control Systems, China, 3Jiangsu Co., Ltd., China
- PS1-8-3
- Sensorless Control of SPMSM with Improved Extended Kalman Filter Based on Runge-Kutta Model
- Peiru Sun1,2, Baodong Chen1,2, Shiqiang Zheng1,2, Lirong Deng1,2, Gengkui Wei1,2, and Hao Wang1,2
- 1Beihang University, China, 2National Institute of Extremely-Weak Magnetic Field Infrastructure, China
- PS1-8-4
- Second Order Generalized Integrator Filtering for Enhanced Sliding Mode Observer with Fuzzy Logic Switching Function
- Kunsheng Cai, Shuanghong Wang, and Zixin Li
- Huazhong University of Science and Technology, China
- PS1-8-5
- Sensorless Active Disturbance Rejection Control of PMSM Based on Extended Kalman Filter
- Li Liu1, Jialiang Dai1, Zhaoyi Wang1, Seungjoo Kim2, and Ju Lee1
- 1Huazhong University, Republic of Korea, 2Korea Testing Certification, Republic of Korea
- PS1-8-6
- Full-order Super-twisting Non-singular Terminal Sliding Mode Observer for PMSM Sensorless Control
- Siyuan Liu1, Ling Liu1, Zihao Li1, Peng Kou1, and Yue Zhang2
- 1Xi’an Jiaotong University, China, 2Dongfang Electric Machinery, China
- PS1-8-7
- A Nonlinear Flux Observer Based on Limit Cycle Oscillator for Sensorless Permanent Magnet Synchronous Motor Drives
- Quanjiang Wang, Song Zhang, and Wen Jiang
- Qingdao University, China
- PS1-8-8
- Multiple Signal Classification Method of EMF-based Speed and Position Estimation for Surface PMSM Sensorless Drives
- Jiasheng Yin, Jinglin Liu, and Zhiman Lu
- Northwestern Polytechnical University, China
Session PS1-9Power Converters of Renewable Energy Systems 1
- Time:
- 13:00-14:00
- Venue:
- FIT Arena
- PS1-9-1
- Extended Describing Function Method based Modeling Technique for Three-port Series Resonant Converters
- Zhijing Ye, Chi Li, and Zedong Zheng
- Tsinghua University, China
- PS1-9-2
- Power Decoupled VSG Based on Full-state Feedback for Better Dynamic Performance and Improved System Robustness
- Yipeng Ding, Xiaoqi Xu, Yi Wang, Yanjun Tian, Yuhua Gao, Zhen Zhang, and Yuwei Li
- North China Electric Power University, China
- PS1-9-3
- Study on Phase-change Cooling for a Reactor Used in Offshore Wind Power Converters
- Zhao Sheng1, Yang Zhangbin1, Yuan Wenhang1, Lei Xiao1,2, Peng Daixiao3, Chen Feiyu3, and Bi Yanke4
- 1Chinese Academy of Sciences, China, 2China Three Gorges Corporation, China, 3China Three Gorges Construction Engineering Corporation, China, 4Rongxin Huiko Electric Co., Ltd., China
- PS1-9-4
- Optimal Placement and Sizing of Hybrid Distribution Transformers in Active Distribution Networks Under Load and PV Generation Uncertainty
- Yanting Xue, Deliang Liang, and Yibin Liu
- Yanting Xue, Deliang Liang, and Yibin Liu
- PS1-9-5
- MPPT Control Method for Micro Wind Turbine System with Newton Method
- Itta Mizutani and Naoki Yamamura
- Mie University, Japan
- PS1-9-6
- Performance Improvement of a Magnus Effect-based Turbine Generator for a Point Absorber Wave Energy Converter
- Ken-ichiro Yamashita and Seina Takekoshi
- Salesian Polytechnic, Japan
- PS1-9-7
- Design of Direct Drive Dual 3-phase Permanent Magnet Generator for Ship-mounted Wind Power Applications Considering Redundancy
- Young-Ho Hwang1, In-seok Song1, Kyung-Won Jeon2, Byung-Hee Kang3, Seok-Won Jung1, and Sang-Yong Jung1
- 1Sungkyunkwan University, Republic of Korea, 2Hanhwa Ocean, Republic of Korea, 3SJ Global Engineering, Republic of Korea
- PS1-9-8
- Power Fluctuation Suppression Under Distorted Grid Voltage in Wind Power System Using Wound Rotor Induction Generator
- Kichiro Yamamoto, Tomoya Nakahira, and Atsushi Shinohara
- Kagoshima University, Japan
- PS1-9-9
- Comparative Study of Operating Characteristics of Doubly-fed Variable-speed Pumped Storage Unit under Two Different Control Strategies
- Tao Lei1, Haoyu Kang1, Jianjun Liu2, Lin Luo2, Jin Wang1, and Libin Zhou1
- 1Huazhong University of Science and Technology, China, 2Dongfang Electric Machinery Co., Ltd., China
- PS1-9-10
- Combined Capacity and Internal Resistance Estimation of Lithium-ion Batteries Based on Voltage Recovery
- Qianyuan Dong and Jinglin Liu
- Northwestern Polytechnical University, China
Session PS1-10Power Converters of Motor Drives
- Time:
- 13:00-14:00
- Venue:
- FIT Arena
- PS1-10-1
- Loss Evaluation of Three-phase Inverter Driven Twophase PWM Scheme at High Switching Frequency
- Masataka Minami and Tenshin Kamahara
- Kindai University, Japan
- PS1-10-2
- An Overview of Resonant DC-link Inverters
- Cheng He, Dong Zhang, Jing Guo, Tao Fan, and Xuhui Wen
- Chinese Academy of Sciences, China
- PS1-10-3
- Robotic Grasp Detection Method Based on a Novel Multi-scale Multi-task Mutual-learning Architecture in Neural Network
- Baixiang Wang, Yinbei Li, Jiaqiang Yang, and Yasir Salam
- Zhejiang University, China
- PS1-10-4
- A Study on Giant Magnetostrictive Actuator for Interior Sound Control System of the Ultra-compact Mobility: Fundamental Consideration on Formation of the Giant Magnetostrictive Phases Depending on Heat Treatment Condition
- Taro Kato1, Ryusei Naganuma1, Koki Bando1, Kentaro Sawada3, Wu Wenbao2, Ikkei Kobayashi2, Jumpei Kuroda2, Daigo Uchino3, Kazuki Ogawa4, Keigo Ikeda5, Ayato Endo6, Hideaki Kato2, Takayoshi Narita2, and Mitusaki Furui1
- 1Tokyo University of Technology, Japan, 2Tokai University, Japan, 3National Institute of Technology (KOSEN), Numazu College, Japan, 4Aichi University of Technology, Japan, 5Hokkaido University of Science, Japan, 6Fukuoka Institute of Technology, Japan
- PS1-10-5
- Topology Optimization for a Spoke-type Permanent Magnet Synchronous Motor Based on a Siamese Convolutional Network
- Yidan Ma1,2, Zaixin Song1, Yongtao Liang1, and Jianfu Cao2
- 1The Hong Kong Polytechnic University, China, 2Xi’an Jiaotong University, China
- PS1-10-6
- Contact Tip Trajectory in Steady-state Regime Prediction Using Deep Learning for Piezoelectric Actuators
- Marc Favier, Xinxin Liao, Marjan Ghorbani, Paolo Germano, and Yves Perriard
- École Polytechnique Fédérale de Lausanne, Switzerland
- PS1-10-7
- Efficiency Map Versus Time-stepping Solutions for Drive Cycle Performance Analysis of Permanent Magnet Synchronous Motors
- Pawan Kumar Dhakal, Kourosh Heidarikani, Roland Seebacher, and Annette Muetze
- Graz University of Technology, Austria
- PS1-10-8
- Maximum Torque per Ampere Control of IPMSM Drive for Electric Two-wheeler Applications
- Adrish Bhaumik1, Xiaocong Li2, Hongxuan Wang1, Lim Shouk Gaem Jeanette2, and Prahlad Vadakkepat1
- 1National University of Singapore, Singapore, 2Agency for Science, Technology and Research (A*STAR), Singapore
Session OS1BInduction Machines
- Time:
- 16:20-18:20
- Venue:
- Room: B
- Chair:
- Makoto Ito (Hitachi, Ltd., Japan), Nijan Yogal (Physikalisch-Technische Bundesanstalt (PTB), Germany)
- OS1B-1
- Compatibility Determination of Single-phase Induction Motor and Load
- Nakarin Prempri
- King Mongkut’s University of Technology, Thailand
16:20-16:40
- OS1B-2
- A Performance Analysis of a 12-slot 10-pole Concentrated Winding Induction Motor with Wave-winding Rotor for Loss Reduction
- Kosuke Kihara and Yuichi Yokoi
- Nagasaki University, Japan
16:40-17:00
- OS1B-3
- Equivalent Two-dimensional Finite Element Analysis of Axial Flux Induction Motor with Double Stator and Single Rotor
- Qin Wang, Jing Wang, and Weiwei Geng
- Nanjing University of Science and Technology, China
17:00-17:20
- OS1B-4
- Controllability Enhancement of Doubly Fed Induction Generators by Use of Tapped Stator Windings
- Boštjan Polajžer1, Annette Muetze2, Matej Kerndl1, and Jožef Ritonja1
- 1University of Maribor, Slovenia, 2Graz University of Technology, Austria
17:20-17:40
- OS1B-5
- Designing for Success: The Imperative of Critical Speed in Electrical Motors - Industry Perspective
- Suhaila Mansor and Ir. Abdul Wahid Jafar
- PETRONAS, Malaysia
17:40-18:00
- OS1B-6
- Influence of Rotor Closed Slots on Magnetic Field Harmonics and Electromagnetic Vibration in Induction Motors
- Longhui Liu, Yu Xiao, Xiaolong Zhao, Jin Wang, and Libing Zhou
- Huazhong University of Science and Technology, China
18:00-18:20
Session OS1CPermanent Magnet Machines 1
- Time:
- 16:20-18:20
- Venue:
- Room: C
- Chair:
- Takashi Kato (Nissan Motor Co., Ltd., Japan), Shun Cai (University College London, UK)
- OS1C-1
- Aluminum Windings and Their Manufacturing Technologies in Electrical Machines: A Review
- Chenyi Zhao1, Han Zhao2,3, Jing Li1, Xiaochen Zhang1,2, Yixiao Ruan2,4, and Huanran Wang5
- 1University of Nottingham Ningbo, China, 2Yongjiang Laboratory, China, 3University of Chinese Academy of Sciences, China, 4Tianjin University, China, 5Zhejiang University, China
16:20-16:40
- OS1C-2
- Investigation of Reducing Magnet Amount in Traction Motors with Aluminum Windings
- Daichi Washio and Kan Akatsu
- Yokohama National University, Japan
16:40-17:00
- OS1C-3
- Layered Structure of Permanent Magnet for Eddy Current Loss Reduction in Electric Machine Design
- Yitong Li1, Wei Xu1, Shuhua Fang1, and Xiping Liu2
- 1Southeast University, China, 2Jiangxi University of Science and Technology, China
17:00-17:20
- OS1C-4
- Evaluation of an IPMSM Featuring a Rotor Core Directly Injection-molded with Sm-Fe-N Bonded Magnets
- Yukihiro Yoshida1, Rie Yoshida2, Taisei Uwano1, Sho Sakurai1, Masahiro Abe2, Shuichi Tada2, Muneo Yamamoto2, and Katsubumi Tajima1
- 1Akita University, Japan, 2Nichia Corporation, Japan
17:20-17:40
- OS1C-5
- A Study on Slot-pole Combinations of Slit Stator Motors
- Masaki Shimoguchi, Yuichi Yokoi, and Tsuyoshi Higuchi
- Nagasaki University, Japan
17:40-18:00
- OS1C-6
- Improving Reluctance Torque of Outer-rotor-type PM Motor with Segmented Rotor Structure
- Sho Sakurai, Yukihiro Yoshida, and Katsubumi Tajima
- Akita University, Japan
18:00-18:20
Session OS1DReluctance Machines 1
- Time:
- 16:20-18:20
- Venue:
- Room: D
- Chair:
- Kyohei Kiyota (Institute of Science Tokyo, Japan), Zhenyao Xu (Shenyang University of Technology, China)
- OS1D-1
- Standalone Testing Method of Synchronous Reluctance Motor for Determining Operating Characteristics
- Masatsugu Oyamada, Sunao Wakasugi, Yusuke Moriyama, and Fumiya Koga
- TMEIC Corporation, Japan
16:20-16:40
- OS1D-2
- Enhanced Performance of a Synchronous Reluctance Motor due to Less Rare-earth Magnets Combined Ferrite and NdFeB
- Kazuto Sakai and Yuto Kojima
- Toyo University, Japan
16:40-17:00
- OS1D-3
- A Novel Synchronous Reluctance Machine with Unequal-turn Concentric Winding
- Yue Tang1, Yawei Wang1, Shengqiao Hao1, Yuanjian Chen1, Yeming Zheng1, Likun Wang2, and Ronghai Qu1
- 1Huazhong University of Science and Technology, China, 2Harbin University of Science and Technology, China
17:00-17:20
- OS1D-4
- Research on High-speed PM-assisted Synchronous Reluctance Motor based on Dual-phase Materials
- Xianghai Zhang, Jing Ou, and Dianguo Xu
- Harbin Institute of Technology, China
17:20-17:40
- OS1D-5
- Characteristics Analysis of a Novel Permanent Magnet Assisted 12/8 Segmental Rotor Type Switched Reluctance Motor
- Tao Li1, Zhenyao Xu1, Yue Zhang2, Dong-Hee Lee3, and Yuli Bao4
- 1Shenyang University of Technology, China, 2Shandong University, China, 3Kyungsung University, Republic of Korea, 4University of Nottingham Ningbo, China
17:40-18:00
- OS1D-6
- Optimization of SRG Comprehensive Performance Based on Two-step Commutation
- Zhiyuan Chai1, Minjun Guan2, Yanting Liu1, Chuang Liu1, and Kai Wang1
- 1Nanjing University of Aeronautics and Astronautics, China, 2Jinling Institute of Technology, China
18:00-18:20
Session OS1EFlux Switching & Variable Flux Machines 1
- Time:
- 16:20-18:20
- Venue:
- Room: E
- Chair:
- Wataru Kitagawa (Nagoya Institute of Technology, Japan), Yu Zeng (Jiangsu University, China )
- OS1E-1
- Influence of Ratio of Outer Diameter and Axial Length on Torque Density in Axial Wound Field Flux Switching Motor with Segmental Rotors
- Yudai Koishi and Hiroki Goto
- Utsunomiya University, Japan
16:20-16:40
- OS1E-2
- Analysis of PM Volume Reduction Methods for Hybrid Excitation Switched Flux Machines
- Wentao Zhang, Zhongze Wu, Wei Hua, and Ji Qi
- Southeast University, China
16:40-17:00
- OS1E-3
- Axial-gap Type Adjustable Field Permanent Magnet Synchronous Motor Using Coil-end and Zero-sequence Current
- Kiyohiro Iwama and Toshihiko Noguchi
- Shizuoka University, Japan
17:00-17:20
- OS1E-4
- A Study on Performance Improvement via Magnetic Saturation in a 12-slot 10-pole Concentrated-winding Permanent-magnet Motor
- Takanori Yoshikawa, Yuichi Yokoi, and Tsuyoshi Higuchi
- Nagasaki University, Japan
17:20-17:40
- OS1E-5
- Proposal of Variable Magnet Vernier Motor for High Efficiency in Wide Speed Range
- Yusuke Ozawa and Kohei Aiso
- Shibaura Institute of Technology, Japan
17:40-18:00
- OS1E-6
- Design and Analysis of Variable Flux PM Machine for Extending Speed Region to Improve the Drive Cycle Efficiency
- H. N. Phyu, Yang Zaifeng, Akash Singh, and Jonathan Hey
- Agency for Science Technology and Research (A*STAR), Singapore
18:00-18:20
Session OS1FMulti-winding/Multi-phase Machine Control
- Time:
- 16:20-18:20
- Venue:
- Room: F
- Chair:
- Tetsuji Daido (Nagasaki University, Japan), Zhe Chen (Northwestern Polytechnical University, China)
- OS1F-1
- Harmonic Current Suppression Scheme for Dual Three-phase PMSM Based on Harmonic Subspace Phase-shifting Operation
- Xiaochen Ma1, Bin Li1, Xuefeng Rui1, and Weijie Hou2
- 1Tianjin University, China, 2Tianjin Key Laboratory of Microgravity and Hypogravity Environment Simulation Technology, China
16:20-16:40
- OS1F-2
- DSOGI Based Rotor Position Estimation for DTP-PMSM Considering DC Bias
- Feng yang Liu, Gui jie Yang, and Jian yong Su
- Harbin Institute of Technology, China
16:40-17:00
- OS1F-3
- Data-driven based Model-free MPC for DTP-PMSM with Optimized Space Vector
- Xiaojun Zhang1, Liang Yan1, Jiaqiang Yang1, Weiqiang Sun1, Yuqi Jia2, and Anqi Situ1
- 1Zhejiang University, China, 2Aviation Key Laboratory of Science and Technology on Aero Electromechanical System Integration, China
17:00-17:20
- OS1F-4
- High Precision Model Predictive Current Control of Dual Three-phase Permanent Magnet Synchronous Motor
- Shuaihang Wei1, Tingna Shi1, Chen Li1, and Zhanqing Zhou1,2
- 1Zhejiang University, China, 2Tiangong University, China
17:20-17:40
- OS1F-5
- A Radial Force Mode Control in IPMSM Using Multi-phase Motor
- Shojiro Fujita and Kan Akatsu
- Yokohama National University, Japan
17:40-18:00
- OS1F-6
- Online Capacitor Monitoring Strategy in 3L-NPC Inverter Driven Open Winding Multiphase Drives
- Shusen Ni1, Chaohui Liu2, and Zedong Zheng1
- 1Tsinghua University, China, 2National New Energy Vehicle Technology Innovation Center, China
18:00-18:20
Session OS1HInduction Motor Control and Drives
- Time:
- 16:20-18:20
- Venue:
- Room: H
- Chair:
- Ikuya Sato (Fuji Electric Co., Ltd., Japan), Boštjan Polajžer (University of Maribor, Slovenia)
- OS1H-1
- Predictive Controller Based on Indirect Vector Control for Induction Motor in Electric Vehicle
- Chakrit Panpean1, Nontakan Mangkala2, Phonsit Santiprapan3, and Jeerawan Homjan4
- 1King Mongkut’s University of Technology, Thailand, 2Suranaree University of Technology, Thailand, 3Prince of Songkla University, Thailand, 4Rajamangala University of Technology Suvarnabhumi, Thailand
16:20-16:40
- OS1H-2
- An Improved Torque Ripple Minimization Pulsewidth Modulation for Induction Motors Under Low Carrier Ratio
- Yang Shen1, Yiming Ma2, Yujia Zhang1, Zhenxiao Yin1, and Hang Zhao1
- 1Hong Kong University of Science and Technology (Guangzhou), China, 2CSG PGC Energy Storage Research Institute, China
16:40-17:00
- OS1H-3
- Speed Sensor-less Control of Induction Machines in Low-speed Region Based on the Gain-scheduled Adaptive Flux Observer and Frequency Control
- Yoshiyasu Takase, Noor Aamir Baloch, Yasumasa Hamabe, Shinya Morimoto, and Takahiro Saeki
- YASKAWA Electric Corporation, Japan
17:00-17:20
- OS1H-4
- Study on Predictive Control Strategy of Pumped-storage DFIM with Dual-objective Constraint Model Under Grid Voltage Imbalance Condition
- Wei Liu1,2, Ruihua Zhang1,2, Bo Zhang1,2, Qiongxuan Ge1,2, and Yaohua Li1,2
- 1Chinese Academy of Sciences, China, 2University of Chinese Academy of Sciences, China
17:20-17:40
- OS1H-5
- Design of an Induction Machine with an Additional Asymmetrical Rotor Winding Providing a Rotor-fixed Anisotropy for Self-sensing Control
- Constantin Schepe and Bernd Ponick
- Leibniz University Hannover, Germany
17:40-18:00
- OS1H-6
- Real-time Extraction for Stator Interturn Fault Features in Induction Motor Drives Using Tracking Filters
- Koroku Nishizawa, Mengyu Li, Jing Bai, and Ikuya Sato
- Fuji Electric Co., Ltd., Japan
18:00-18:20
Session OS1IPM Motor Control 1
- Time:
- 16:20-18:20
- Venue:
- Room: I
- Chair:
- Naoki Kawamura (Chubu University, Japan), Shuai Mao (Northwestern Polytechnical University, China)
- OS1I-1
- Seamless Switch of Control Mode Over Current Vector Control and Voltage Phase Control in IPMSM
- Takumi Kokago and Keiichiro Kondo
- Waseda University, Japan
16:20-16:40
- OS1I-2
- Voltage Overshoot Mitigation for PMSM Voltage Closed-loop Field-weakening Control Based on a Low-pass Feedforward Compensator
- Linzhi Wang, Yong Yu, Bo Wang, and Dianguo Xu
- Harbin Institute of Technology, China
16:40-17:00
- OS1I-3
- Torque Derivative Value Manipulated Type Torque Feedback Control System for PMSM
- Naoki Kawamura and Masaru Hasegawa
- Chubu University, Japan
17:00-17:20
- OS1I-4
- Active Disturbance Rejection Control - Based on Delayed Signal Cancellation for Current Harmonics Reduction in Permanent Magnet Synchronous Motors Drives
- Huayu Ji1, Zifeng Chen1, Xijian Lin1, Xinghao Wang1, Xi Luo1, and Dianxun Xiao1,2
- 1The Hong Kong University of Science and Technology (Guangzhou), China, 2HKUST, China
17:20-17:40
- OS1I-5
- Current Tracking for PMSMs Using Discrete Time Delay Control with Estimation Error Compensation
- Gan Wang, Yanfei Cao, Hongjie Li, and Tingna Shi
- Zhejiang University, China
17:40-18:00
- OS1I-6
- Ultra-local Model-free Predictive Control with Switching Strategy of PMSMs for Two-phase Stationary Current
- Xueyan Wang, Zhenxiao Yin, Yang Shen, Ming Liu, and Hang Zhao
- The Hong Kong University of Science and Technology (Guangzhou), China
18:00-18:20
Session OS1JSwitched Reluctance Motor Control and Drives
- Time:
- 16:20-18:20
- Venue:
- Room: J
- Chair:
- Kazuhiro Ohyama (Fukuoka Institute of Technology, Japan)
- OS1J-1
- Towards Sustainable Mobility: Optimal Flux Control of Drive Cycles for Variable Flux Motors via Deep Reinforcement Learning
- Zaifeng Yang, Hla Nu Phyu, Xiaocong Li, and Jonathan Hey
- Agency for Science, Technology and Research (A*STAR), Singapore
16:20-16:40
- OS1J-2
- Speed – Torque Range Expansion of In-wheel Axial-flux SR Motor for Compact EV
- Shintaro Nagasawa, Yusuke Nishigai, and Kenji Nakamura
- Tohoku University, Japan
16:40-17:00
- OS1J-3
- Characteristics of Switched Reluctance Motor using Operating Area Expandable Drive Circuit in Unexpanded Operating Area
- Taisei Ishizawa, Ryuya Sugai, Hiroki Goto, and Hirohito Funato
- Utsunomiya University, Japan
17:00-17:20
- OS1J-4
- An Online Torque Sharing Function with Torque Reference Self-adjusting Method for Switched Reluctance Machines
- Zixin Li, Shuanghong Wang, and Libing Zhou
- Huazhong University of Science and Technology, China
17:20-17:40
- OS1J-5
- Investigation on the Maximum Efficient Current Waveform of SRM Considering Torque Ripple Reduction
- Atsunori Miyata, Yudai Koishi, Dai Kojima, and Hiroki Goto
- Utsunomiya University, Japan
17:40-18:00
- OS1J-6
- Loss Reduction in V/f Control for Switched Reluctance Motor Driven by Single-pulse Voltage
- Hirotaka Kato, Hiroki Watanabe, and Jun-ichi Itoh
- Nagaoka University of Technology, Japan
18:00-18:20
Session OS1KPower Converters of Renewable Energy Systems 1
- Time:
- 16:20-18:20
- Venue:
- Room: K
- Chair:
- Ken-ichi Kondo (Kansai University, Japan), Yi Wang (North China Electric Power University, China)
- OS1K-1
- A High Gain Common Ground Inverter without Electrolytic Capacitors
- Jiangpeng Yang, Fanglin Bai, Yanni Ming, Yang Li, Linzhe Li, and Zeliang Shu
- Southwest Jiaotong University, China
16:20-16:40
- OS1K-2
- A Minimum Backflow Power with Optimal Current Stress Method of Single-stage DAB Microinverter
- Ruinan Xue, Panbao Wang, Yousu Yao, Wei Wang, and Dianguo Xu
- Harbin Institute of Technology, China
16:40-17:00
- OS1K-3
- A Current-limiting Scheme with Adjustable Virtual Impedance for Three-phase Four-wire Grid Forming Inverters
- Preenapan Panya, Surapong Suwankawin, and Somboon Sangwongwanich
- Chulalongkorn University, Thailand
17:00-17:20
- OS1K-4
- A 36-pulse Thyristor Hydrogen Converter Based on a Nine-phase Phase-shifting Transformer
- Jingfang Wang1, Changbao Wang1, Teng Liu2, and Bin Wang1
- 1Harbin Engineering University, China, 2Beijing Feiyu Microelectronic Circuits Company Limited, China
17:20-17:40
- OS1K-5
- Energy Management Strategy of Fuel Cell Management System for Flooding Condition with Distributed Supercapacitors Storage Element
- Apinya Siangsanoh1, Panupan Srisomboon1, Matheepot Phattanasak1, Roghayeh Gavagsaz-Ghoachani2, Jean-Philippe Martin3, Serge Pierfederici3, and Sophie Didierjean3
- 1KMUTNB, Thailand, 2Shahid Beheshti University, Iran, 3Université de Lorraine, France
17:40-18:00
- OS1K-6
- A Proposal of Permanent Magnet Transverse Flux Generator for Large Wind Turbine Generation System
- Kumano T and Shinkai T
- Meiji University, Japan
18:00-18:20
Session OS1LPower Converters of Motor Drives
- Time:
- 16:20-18:20
- Venue:
- Room: L
- Chair:
- Akihito Mizukoshi (National Institute of Technology, Kisarazu College, Japan), Takanobu Ohno (University of Innsbruck, Austria)
- OS1L-1
- Space Vector Modulation with Flexible Switching Pause Period Function for Three-phase PMSM Drive Inverters
- Keitaro Kawarazaki and Nobukazu Hoshi
- Tokyo University of Science, Japan
16:20-16:40
- OS1L-2
- High-power Density Three-phase Inverter with 3D Circuit Structure Using Liquid Immersion Cooling
- Norihiro Izu and Daiki Satou
- Tokyo Denki University, Japan
16:40-17:00
- OS1L-3
- Prototype Design and Testing of a Novel Unidirectional Back-to-back T-type Three-level Converter for High Efficiency Applications
- Monchai Ariyapuek1, Somboon Sangwongwanich1, Surapong Suwankawin1, Puchong Jirachaisophon2, Pongsak Mongkoldee2, and Masaki Kanamori3
- 1Chulalongkorn University, Thailand, 2Carrier Air Conditioning Co., Ltd., Thailand, 3Carrier Japan Corporation, Japan
17:00-17:20
- OS1L-4
- Design and Comparison of Multilevel Energy Storage Converter Topologies for High Power Motor Drive Applications
- Fanqiang Gao1,2, Zixin Li1,2, Ye Zhang1,2, Jinhao Zhang1,2, Yaohua Li1,2, Hang Zhang1, and Cong Zhao1,2
- 1Chinese Academy of Sciences, China, 2University of Chinese Academy of Sciences, China
17:20-17:40
- OS1L-5
- Wide Frequency Range Second Harmonic Suppression in Cascaded H-bridge Energy Storage Converters Using a Disturbance Observer
- Jinhao Zhang, Fanqiang Gao, Zixin Li, Ye Zhang, Cong Zhao, and Yaohua Li
- Chinese Academy of Sciences, China, University of Chinese Academy of Sciences, China
17:40-18:00
- OS1L-6
- Application of GaN E-HEMT to Reaction Wheel Motor Drive
- David Lwo1, Min-Fu Hsieh1, Yen-Kai Kuo1, Xue-Pin Lu1, Chen-Lin Chan1, and Chih-Chao Hsu2
- 1National Cheng Kung University, Taiwan, 2National Chung-Shan Institute of Science and Technology, Taiwan
18:00-18:20
November 28 (Thu.), 2024
Session OS2BLinear Drives and Magnetic Levitations 1
- Time:
- 9:30-11:50
- Venue:
- Room: B
- Chair:
- Hiroyuki Ohsaki (The University of Tokyo, Japan), Jinhua Du (Xi’an Jiaotong University, China)
- OS2B-1
- The Parameter Sensitivity Analysis of Linear Permanent Magnet Assisted Synchronous Reluctance Motor
- Yu Hanchuan, Xuzhen Huang, and Zhuoran Zhang
- Nanjing University of Aeronautics and Astronautics, China
9:30-9:50
- OS2B-2
- Maximizing Thrust Force and Reducing Eddy Current Loss in Arc Linear Servo Motors Using 3D FE Analysis of Partial Magnet Segmentation
- Zuhair Abbas, Byoung-Wook Jo, Sung-Won Lee, Dae-Hyeon Kim, and Jin Hur
- Incheon National University, Republic of Korea
9:50-10:10
- OS2B-3
- Effect of Primary Iron Core on Performance Characteristics of Linear Switched Reluctance Motor with High-temperature Superconducting Excitation Windings
- Ryuto Motoda1, Shuma Kawabata1, and Tadashi Hirayama2
- 1Kagoshima University, Japan, 2Kogakuin University, Japan
10:10-10:30
- OS2B-4
- Systemic Stability Evaluation of a Miniature Maglev Drive System for a Pediatric Left Ventricular Assist Device
- Nobuyuki Kurita1,2,3,4, Victor Tedesco3, Ethan Maddin3, Chris Hoi Houng Chan3, Iki Adachi1,2, O. H. Frazier1,3, and Yaxin Wang3
- 1Baylor College of Medicine, USA, 2Texas Children’s Hospital, USA, 3The Texas Heart Institute, USA, 4Gunma University, Japan
10:30-10:50
- OS2B-5
- Design Method and Systemic Robustness Evaluation for the Magnetically Levitated Drive System of a Hemocompatibility Assessment Platform
- Nobuyuki Kurita1,2,4, Victor Tedesco3, Ethan Maddin3, Chris Hoi Houng Chan3, Iki Adachi1,2, O. H. Frazier1,3, and Yaxin Wang3
- 1Baylor College of Medicine, USA, 2Texas Children’s Hospital, USA, 3Texas Heart Institute, USA, 4Gunma University, Japan
10:50-11:10
- OS2B-6
- Additive Manufacturing Overlapping Winding for Enhanced Performance of a Coreless Permanent Magnet Synchronous Linear Motor
- Zheng Wang, Xuzhen Huang, and Jing Li
- Nanjing University of Aeronautics and Astronautics, China
11:10-11:30
- OS2B-7
- Research on the Characteristics of Multi-mover Independent Coil Permanent Magnet Linear Synchronous Motor
- Qinwei Sun, Mingyi Wang, Minghong Liu, and Liyi Li
- Harbin Institute of Technology, China
11:30-11:50
Session OS2CPermanent Magnet Machines 2
- Time:
- 9:30-11:50
- Venue:
- Room: C
- Chair:
- Yoshihiro Miyama (Mitsubishi Electric Corporation, Japan), Yanlei Yu (Nanyang Technogical University, Singapore)
- OS2C-1
- Optimal Design of Fractional Slot Number Using Response Surface Method on the Cogging Torque and Unbalanced Magnetic Pull Reduction in Permanent Magnet Machine
- Tajuddin Nur1, Syamsir Abduh2, Herlina3, and Eduard Muljadi4
- 1Atma Jaya Catholic University of Indonesia, 2PLN Institute of Technology, Indonesia, 3Universitas Sriwijaya, Indonesia, 4Auburn University, USA
9:30-9:50
- Chair:
- OS2C-2
- Design and Analysis of a Hybrid Excitation Synchronous Generator with Radial Additional Air-gaps
- Longxin Du1, Zhuoran Zhang1, and Chen Wang2
- 1Nanjing University of Aeronautics and Astronautics, China, 2Anhui Polytechnic University, China
9:50-10:10
- OS2C-3
- Achieving Magnetic Force and Cogging Torque Reduction in a Permanent Magnet Generator with Concentrated Slot Technique and Pole Arc Optimization at Magnet Edge
- Syamsir Abduh1, Tajuddin Nur2, Eduard Muljadi3, and Herlina4
- 1Institut Teknologi PLN, Indonesia, 2Universitas Katolik Indonesia Atma Jaya, Indonesia, 3Auburn University, USA, 4Sriwijaya University, Indonesia
10:10-10:30
- OS2C-4
- An Optimized Boundary to Characterize the Relationship between Training Data Quantity and Neural Network Accuracy in Describing Variable Parameters of PMSMs
- Yilin Ma1,2, Huan Yang1,2, Rongxiang Zhao1, and Xiangning He1
- 1Zhejiang University, China, 2Zhejiang Provincial Key Laboratory of Electrical Machine Systems, China
10:30-10:50
- OS2C-5
- Design and Optimization of Magnetizer for Axial Flux Permanent Magnet Motor with Halbach Array
- Puspa Subedi, Ju-Hyeong Moon B, and Dong-Woo kang C
- Keimyung University, Republic of Korea
10:50-11:10
- OS2C-6
- Reconstruction Method of Stator Magnetomotive Force of High-speed Fault-tolerant Permanent Magnet Synchronous Motor with Single Winding Independent Control Structure
- Zhibai Gao1, Jiwei Cao1, Chengbao Zhong2, Jiaxi Liu1, Yuchen Song1, and Liyi Li1
- 1Harbin Institute of Technology, China, 2Guangdong Provincial Key Laboratory of High-Performance Servo System, China
11:10-11:30
- OS2C-7
- Fast Diagnosis of Faults with One-phase High-resistance Characteristics in FPPMSM
- Wei Liu, Zihang Yuan, Chengde Tong, Mingqiao Wang, and Ping Zheng
- Harbin Institute of Technology, China
11:30-11:50
Session OS2DSynchronous Machines 1
- Time:
- 9:30-11:50
- Venue:
- Room: D
- Chair:
- Yuichi Yokoi (Nagasaki University, Japan), Hao Chen (Zhejiang University, China)
- OS2D-1
- Validation of the Analytical Prediction of the Damper Winding Pole-to-pole Impedance in Hydro Generators
- Andreas Ridder1, Allan de Barros1, Urban Lundin2, Bo Hernnäs2,3, Babette Schwarz4, and Bernd Ponick1
- 1Leibniz University Hannover, Germany, 2Uppsala University, Sweden, 3Voith Hydro AB, Sweden, 4Voith Hydro Holding GmbH & Co. KG, Germany
9:30-9:50
- OS2D-2
- Digitalization of Excitation Control Circuit for Self-starting Salient-pole Synchronous Motor
- K. Matsuura, Y. Kosugi, and T. Watanabe
- TMEIC Corporation, Japan
9:50-10:10
- OS2D-3
- Shaft Voltage Reduction Technique by Layered-shield of Wound Field Synchronous Motor
- Jun-Hyeok Heo1, Jun-Kyu Kang1, Jun-Hyuk Im2, and Jin Hur1
- 1Incheon National University, Republic of Korea, 2Daegu Mechatronics & Materials Institute, Republic of Korea
10:10-10:30
- OS2D-4
- Temperature Calculation Method for Transposed Armature Windings and its Verification through Direct Measurement of Strand Temperatures
- Kenichi Hattori1, Kazuhiko Takahashi1, Keiji Kobashi2, Hiroshi Okabe3, and Seijiro Muramatsu
- 1Mitsubishi Generator, Japan, 2Hokkaido University, Japan, 3Mitsubishi Heavy Industries, Japan
10:30-10:50
- OS2D-5
- Secondary-fault Diagnosis of a Rotating Rectifier in a Three-stage Starter-generator based on the Idle Winding Terminal Voltage
- Shoucheng Li1, Chenghao Sun1, Wenjing Xu1, Ji Pang2, Sijia Cheng1, Jiawei Zhang1, Xinyu Li3, and Shuye Ding1
- 1Nanjing Normal University, China, 2Xi’an University of Posts & Telecommunications, China, 3State Grid Xi’an Electric Power Supply Company, China
10:50-11:10
- OS2D-6
- Static Testing System for Electromagnetic Torque Characteristics of Synchronous Motors
- Jiuyin Zhang1, Jian-Xin Shen1, Wen-Jie Wan1, Dan Shi1, Shun Cai2, and Yunchong Wang1
- 1Zhejiang University, China, 2University College London, UK
11:10-11:30
- OS2D-7
- Carbon Emission Evaluation and Comparison for Different Electric Machines
- Xuebei Zhang, Zeyuan Xu, Fengyu Zhang, Mostafa Ahmadi Darmani, Jianan Jiang, Chris Gerada, and David Gerada
- University of Nottingham, UK
11:30-11:50
Session OS2ENumerical Analysis and Modeling 1
- Time:
- 9:30-11:50
- Venue:
- Room: E
- Chair:
- Yasuhito Takahashi (Doshisha University, Japan)
- OS2E-1
- Fast Calculation of Proximity Loss Induced by Harmonic Current in Electrical Machines Using Magnetic Equivalent Circuit
- Yixiang Yuan1, Mostafa Ahmadi Darmani2, Yuli Bao1, Xiaochen Zhang3, David Gerada2, and He Zhang3
- 1University of Nottingham Ningbo, China, 2University of Nottingham, UK, 3Yongjiang Laboratory, China
9:30-9:50
- OS2E-2
- Rotational Magnetic Field Calculation of Electrical Motors by Incorporating a Modified Anisotropic Vector Hysteresis Model
- Jiatong Yin, Yongjian Li, Shuaichao Yue, Hongtao Shi, and Jiapeng Zhou
- Hebei University of Technology, China
9:50-10:10
- OS2E-3
- Study on Torque Ripple Reduction of Asymmetric Flux Barrier using Topology Optimization and Frozen Permeability Method
- Shunsuke Yamamoto and Yuki Hidaka
- Nagaoka University of Technology, Japan
10:10-10:30
- OS2E-4
- Theoretical Assessment of Electrical Steel Magnetic Components During PWM-type Conversion: A Comparison Between Two Hysteresis Models
- Shengze Gao1,2, Benjamin Ducharne3,4, Yanhui Gao2, and Xiaojun Zhao1
- 1North China Electric Power University, China, 2Oita University, Japan, 3Tohoku University, Japan, 4Univ Lyon, France
10:30-10:50
- OS2E-5
- Lumped Parameter Thermal Network Modeling and Analyzing for a 15 kW, 120000 rpm High-speed Cage Solid Rotor Induction Motor
- Dongdong Zhang1, Quan Zhang1, Jiawei Yi1, Shuaijun Chu2, Zhihao Zhu1, Min Sun1, Qinyuan Dong1, and Cunhao Rong3
- 1Guangxi University, China, 2Xi’an Jiaotong University, China, 3Southeast University, China
10:50-11:10
- OS2E-6
- Modelling for PWM Carrier Loss Evaluation in Claw-pole Machine using MATLAB/Simulink
- Yusuke Okunishi1, Takashi Kosaka1, Yu Hirai2, Yoshihiro Miyama2, and Hideaki Arita2
- 1Nagoya Institute of Technology, Japan, 2Mitsubishi Electric Corporation, Japan
11:10-11:30
- OS2E-7
- Analytical Calculation of Cogging Torque Considering Core Reluctance by Using Equivalent Field Winding Model
- Peidong Hu1, Dong Yan1, Zhen Zhang2, Tingna Shi1, and Changliang Xia1,2
- 1Zhejiang University, China, 2Advanced Electrical Equipment Innovation Center, China
11:30-11:50
Session OS2FNoise, Vibration and Reliability of Electric Machines 1
- Time:
- 9:30-11:50
- Venue:
- Room: F
- Chair:
- Katsutoku Takeuchi (Toshiba Infrastructure Systems & Solutions Corporation, Japan), Yatai Ji (Tsinghua University, China)
- OS2F-1
- Precise Vibration Measurement with Mechanical Load Isolation for Sub-fractional Horsepower Motors
- Shahin Asgari, Nejat Saed, and Annette Muetze
- Christian Doppler Laboratory for Brushless Drives for Pump and Fan Applications, Austria, Graz University of Technology, Austria
9:30-9:50
- OS2F-2
- Temperature Impact on Insulation Lifetime During Electrical Endurance Tests
- Yatai Ji1, Paolo Giangrande2, Weiduo Zhao3, Michael Galea4, Giampaolo Buticchi3, and Pinjia Zhang1
- 1Tsinghua University, China, 2University of Bergamo, Italy, 3University of Nottingham Ningbo, China, 4University of Malta, Malta
9:50-10:10
- OS2F-3
- Compensation of Radial Mode 0 Vibration of an Electrically Excited Synchronous Machine using Harmonic Field Current Injection
- Jonas Jansen and Axel Mertens
- Leibniz University Hannover, Germany
10:10-10:30
- OS2F-4
- On the Use of Machine Learning to Improve the Analytical NVH Predictions of Electric Machines
- Fabien Chauvicourt, Raluca Raia, Sebastian Ciceo, and Kohta Sugiura
- Siemens Digital Industries Software, Belgium
10:30-10:50
- OS2F-5
- A Sparsity-driven Method to Iteratively Extract Motor Fault Signatures in Varying-speed Operations
- Dehong Liu, Yebin Wang, and Shinya Tsuruta
- Mitsubishi Electric Research Laboratories, USA
10:50-11:10
- OS2F-6
- Determination of the Equivalent Mechanical Properties of the Stator Core for Vibration Analysis in Hydro Generators
- Allan de Barros1, Amir Ebrahimi2, Babette Schwarz3, and Bernd Ponick1
- 1Leibniz University Hannover, Germany, 2University of Bremen, Germany, 3Voith Hydro Holding GmbH & Co. KG, Germany
11:10-11:30
- OS2F-7
- Analysis and Suppression of Synchronous Reluctance Motors with Mirror Asymmetric Rotors
- Yujie Yuan, Yawei Wang, Xuan Li, Yuanjian Chen, Yeming Zheng, and Ronghai Qu
- Huazhong University of Science and Technology, China
11:30-11:50
Session OS2GPM Motor Control 2
- Time:
- 9:30-11:50
- Venue:
- Room: G
- Chair:
- Tetsuya Kojima (Mitsubishi Electric Corporation, Japan), Frederik De Belie (Ghent University, Belgium)
- OS2G-1
- A Dual Internal Mode Decoupling Control Strategy for Permanent Magnet Synchronous Motor Drives Fed by the Current Source Inverter
- Yuzhuo Lu, Tianhao Yao, Youtong Wu, and Quntao An
- Harbin Institute of Technology, China
9:30-9:50
- OS2G-2
- Current Source Inverter Drive System with Equivalent DC-machine Control Characteristics
- Spasoje Mirić1, Predrag Pejović2, Takanobu Ohno1, and Michael Haider
- 1University of Innsbruck, Austria, 2University of Belgrade, Serbia
9:50-10:10
- OS2G-3
- Torque Synchronous Control for Dual-PMSM Contra-rotating Propulsion System Based on Parameter Compensation
- Minghao Wang, Mingqiao Wang, Chengde Tong, Ziyu Zhou, and Ping Zheng
- Harbin Institute of Technology, China
10:10-10:30
- OS2G-4
- Hybrid Frequency and Power Dual-converter for Harmonics Suppression of Open-end Winding High-speed PMSM
- Yang Liang, Shuchen Xu, Shangze Li, Deliang Liang, Shaofeng Jia, Yuheng Wang, Shuaijun Chu, and Qidong Wen
- Xi’an Jiaotong University, China
10:30-10:50
- OS2G-5
- Common Mode Voltage Elimination and Conducted EMI Reduction for Two-unit PMSM
- Yongxiang Xu, Pan Wang, Haiyang Gao, Jibin Zou, and Shaoshan Jin
- Harbin Institute of Technology, China
10:50-11:10
- OS2G-6
- Analysis of High-frequency Harmonics of the Common Mode Voltage Under AZSPWM1
- Yongxiang Xu, Haiyang Gao, Pan Wang, and Jibin Zou
- Harbin Institute of Technology, China
11:10-11:30
- OS2G-7
- Control Strategy Considering Angle Difference of PM Synchronous Motor with an Integrated Common-mode Voltage Filter
- Jing Zhang1, Xiaochen Zhang1,2, Chunyang Gu1,2, and Jing Li1
- 1University of Nottingham, China, 2Yongjiang Laboratory, China
11:30-11:50
Session OS2HSynchronous Machine Control and Drives 1
- Time:
- 9:30-11:50
- Venue:
- Room: H
- Chair:
- Kiyohiro Iwama (Shizuoka University, Japan), Zhiwei Chen (Zhengzhou University of Light Industry, China)
- OS2H-1
- An Active Disturbance Rejection Control Strategy for the HVDC Generation System of More Electric Aircraft
- Yankun Wang, Zhuoran Zhang, Yiming Yao, Heng Shi, Hanqi Li, and Jincai Li
- Nanjing University of Aeronautics and Astronautics, China
9:30-9:50
- OS2H-2
- A Starting Control Scheme for Dual Three-phase Three-stage Brushless Synchronous Starter/generator Based on VSD Conversion
- Jun Zhang1, Junwei Zhang2, Kun Gao2, Hanbing Dan1, and Mei Su1
- 1Central South University, China, 2Aecc South Industry Company Limited, China
9:50-10:10
- OS2H-3
- Parameter-independent Back Electromotive Force Information Estimation Method of the Main Exciter of the Brushless Synchronous Starter Generator
- Shuai Mao, Chongzhao Ma, Shuo Zhang, Ziqun Guo, Jiachen Shi, and Weiguo Liu
- Northwestern Polytechnical University, China
10:10-10:30
- OS2H-4
- A Novel Field Current Estimation Method of the Brushless Synchronous Starter/generator
- Chongzhao Ma, Shuai Mao, Guangzhao Luo, Weiguo Liu, Ziqun Guo, and Shuo Zhang
- Northwestern Polytechnical University, China
10:30-10:50
- OS2H-5
- Q-axis Current-based Excitation Current Calculation Method for Torque Ripple Suppression of Hybrid Excitation Machine
- Changzhou Lu, Zhuoran Zhang, Xiangpei Gu, Yao Sun, Taiyang Dai, and Weijia Jiang
- Nanjing University of Aeronautics and Astronautics, China
10:50-11:10
- OS2H-6
- Suspension Control for Bearingless Doubly Salient Electromagnetic Motor Considering Magnetic Saturation Based on Back Propagation Neural Network
- Zhongshan Luo, Li Yu, Wei Chen, and Haonan Zou
- Nanjing University of Aeronautics and Astronautics, China
11:10-11:30
- OS2H-7
- Small-signal Modeling and Impedance Analysis of Doubly Salient Electrical-magnetic Generator Considering Saturation
- Lu Wang, Li Yu, Yiming Yao, Yongtao Guan, and Zhuoran Zhang
- Nanjing University of Aeronautics and Astronautics, China
11:30-11:50
Session OS2ISensorless Control 1
- Time:
- 9:30-11:50
- Venue:
- Room: I
- Chair:
- Atsushi Shinohara (Kagoshima University, Japan), Jiadan Wei (Nanjing University of Aeronautics and Astronautics, China)
- OS2I-1
- Discrete Variable Gain Second-order Sliding Mode Observer Design for Position-sensorless Control of Permanent Magnet Synchronous
- Jiangwen Liu, Chengming Zhang, Pengrui Fu, Yiming Sun, Chaoyu Zhang, and Liyi Li
- Harbin Institute of Technology, China
9:30-9:50
- OS2I-2
- An Improved Speed Observer Based on Current Prediction Compensation for PMSM Sensorless Control
- Zhe Chen1, Cong Gao1, Peiyang Chen1, Jincheng Li1, Hang Zhang2, and Guangzhao Luo1
- 1Northwestern Polytechnical University, China, 2Xi'an University of Technology, China
9:50-10:10
- OS2I-3
- Improvement of Sensorless Rotor Angle Estimation using Zero-sequence Voltage Measurement
- Robin Meisinger1, Wolfgang Gruber1, and Siegfried Silber2
- 1Johannes Kepler University Linz, Austria, 2Linz Center of Mechatronics, Austria
10:10-10:30
- OS2I-4
- Dynamic Position Estimator for a PMSM using Regular Current Sampling and Numerical Optimisation
- Viktor Willich, Niklas Himker, and Axel Mertens
- Leibniz University Hannover, Germany
10:30-10:50
- OS2I-5
- An Improved Speed Estimation Method for PMSM Using Speed Correction
- Weiqiang Sun1, Zhebin Yang1, Xiaojun Zhang1, Anqi Situ1, Yuqi Jia2, and Jiaqiang Yang1
- 1Zhejiang University, China, 2Aviation Key Laboratory of Science and Technology on Aero Electromechanical System Integration, China
10:50-11:10
- OS2I-6
- Double ESO Aided Nonlinear Flux Observer for Sensorless Control of PMSM
- Zhe Chen1, Jincheng Li1, Kun Zhang2, Mingyuan Zhangliu1, Hang Zhang3, and Guangzhao Luo1
- 1Northwestern Polytechnical University, China, 2Nanjing Engineering Institute of Aircraft Systems, China, 3Xi'an University of Technology, China
11:10-11:30
- OS2I-7
- Sensorless Control Strategy for Permanent Magnet Synchronous Motors Based on Enhanced SOGI-FLL with Limit Cycle Oscillator
- Siqi Wang1, Guoqiang Zhang1, Yuan Yuan2, Kai Tian2, Xiangqian Zhang2, Shuhui Jin2, Gaolin Wang1, and Dianguo Xu1
- 1Harbin Institute of Technology, China, 2Tianjin Research Institute of Electric Science Co., Ltd., China
11:30-11:50
Session OS2JMotion Control and Servo Systems
- Time:
- 9:30-11:50
- Venue:
- Room: J
- Chair:
- Seiichiro Katsura (Keio University, Japan)
- OS2J-1
- Integrated Motor Control with Active Bearings for Speed Regulation with Rotor Imbalance
- Tingyu Lin, Dunant Halim, Zhuang Xu, and Chung Ket Thein
- University of Nottingham Ningbo, China
9:30-9:50
- OS2J-2
- Iterative Learning Controller Based on Linear Extended State Observer for Six-degree-of-freedom Micro-motion Stage
- Junchi Li, Mingyi Wang, Minghong Liu, Chengming Zhang, and Liyi Li
- Harbin Institute of Technology, China
9:50-10:10
- OS2J-3
- Speed Control of Separately Excited DC Motor Using Fuzzy Logic Controller
- Jeerawan Homjan1, Phonsit Santiprapan2, and Chakrit Panpean3
- 1Rajamangala University of Technology Suvarnabhumi, Thailand, 2Prince of Songkla University, Thailand, 3King Mongkut’s University of Technology, Thailand
10:10-10:30
- OS2J-4
- Advanced Task Realization by Robot Fingers Using Mode Quarry Matrix
- Aina Kojima, Shunichi Sakurai, and Seiichiro Katsura
- Keio University, Japan
10:30-10:50
- OS2J-5
- Motion Analysis of Gravity Compensation Mechanism with Low Inertia Using Parallel Wire Mechanism
- Yusaku Kuroki and Seiichiro Katsura
- Keio University, Japan
10:50-11:10
- OS2J-6
- A Comparative Study of Vibration Damping Based on Wave Model—Decoupling Reflected Waves from Traveling Waves
- Kosuke Shikata1, Krzysztof Szabat2, and Seiichiro Katsura1
- 1Keio University, Japan, 2Wroclaw University of Science and Technology, Poland
11:10-11:30
- OS2J-7
- Development of a Pneumatic Leader-follower System with Force Feedback
- Keisuke Goto, Hajime Moriguchi, Hiroaki Kobayashi, and Osamu Ichikawa
- Polytechnic University, Japan
11:30-11:50
Session OS2KPower Converter 1 (DC-DC)
- Time:
- 9:30-11:50
- Venue:
- Room: K
- Chair:
- Shohei Komeda (Tokyo University of Marine Science and Technology, Japan), Tzung-Lin Lee (National Sun Yat-sen University, Taiwan)
- OS2K-1
- Enhanced Model Predictive Controller Utilizing Kalman Filter for Dual Active Bridge Converter in More Electric Aircraft
- Han Wu, Bingqiang Li, Dongheng Wang, Saleem Riaz, and Yuening Deng
- Northwestern Polytechnical University, China
9:30-9:50
- OS2K-2
- Non-inverting Buck-boost (NIBB) Converter Analysis of GaN Half Bridges Operation for 24V Unity Conversion Ratio
- Ravi Nath Tripathi
- Kyushu Institute of Technology, Japan
9:50-10:10
- OS2K-3
- A Dual Three-phase LLC Resonant Converter with Phase Shedding Strategy for High Power Application
- Xinghong Luo1, Xuliang Yao1, Yannan Gao2, and Jingfang Wang1
- 1Harbin Engineering University, China, 2Guangdong Ocean University, China
10:10-10:30
- OS2K-4
- Ripple Current Compensation of DAB Converter with Matching Transformer-less Series DC Active Filter in DC Distribution Feeder
- Yuya Abe and Hiroaki Yamada
- Yamaguchi University, Japan
10:30-10:50
- OS2K-5
- Adaptive Neuron Adjustment for Transient Accuracy Enhancement in FPGA-based Power Electronics Simulation
- Haowen Weng, Zixiang Liao, and Can Wang
- Harbin Institute of Technology (Shenzhen), China
10:50-11:10
- OS2K-6
- A Multicellular Converter Topology Allowing for the Scaling of GaN HEMTs to Higher Power Applications
- Jordon A Dobson1, Alan J Watson1, Paul Evans1, Neo Lophitis1, Mark Johnson1, and Rob Leedham2
- 1University of Nottingham, UK, 2Amantys Power Electronics Ltd, UK
11:10-11:30
- OS2K-7
- Multiple Output Power Supply Utilizing Multi-winding Transformers
- Thanachot Srimongkol, Narong Thumputi, and Satit Owatchaiphong
- King Mongkut’s University of Technology, Thailand
11:30-11:50
Session OS2LPower Electronics of Mobility Applications
- Time:
- 9:30-11:50
- Venue:
- Room: L
- Chair:
- Jun-ichi Itoh (Nagaoka University of Technology, Japan), Burin Yodwong (King Mongkut’s University of Technology, Thailand)
- OS2L-1
- A Seamless Operation of Bidirectional Battery Charger for Electric Vehicles with Power Quality Compensator
- Reo Emoto1, Shun Okamoto2, Fuka Ikeda2, Masayuki Okamoto2, Hiroaki Yamada1, and Toshihiko Tanaka1
- 1Yamaguchi University, Japan, 2National Institute of Technology, Ube College, Japan
9:30-9:50
- OS2L-2
- Adaptive Stabilization of a Three-stage Brushless Generator-based DC Electrical Power System in More Electric Aircraft
- Fan Yang, Xin Chen, Donghui Zhang, and Zhiyuan Teng
- Nanjing University of Aeronautics and Astronautics, China
9:50-10:10
- OS2L-3
- Analysis of the Vehicle-grid System Stability Considering Electromagnetic Transient Characteristics of High-speed Railway Vehicles
- Wenjing Tian, Chenghao Liu, Sixian Zhu, Jien Ma, Lin Qiu, Zhenzhi Lin, and Youtong Fang
- Zhejiang University, China
10:10-10:30
- OS2L-4
- Quantification of Steady-state Efficiency Maps vs. Time-stepping Solutions for Drive Cycle Performance Analysis of Induction Motors
- Kourosh Heidarikani, Pawan Kumar Dhakal, Roland Seebacher, and Annette Muetze
- Graz University of Technology, Austria
10:30-10:50
- OS2L-5
- A Novel Phase-unit Axial-modular Permanent Magnet Machine with U-core Stators for Aerospace Propulsion System
- Yanlei Yu1, Feng Chai2, Yulong Pei2, Guanghui Yang3, and Christopher H. T. Lee1
- 1Nanyang Technological University, Singapore, 2Harbin Institute of Technology, China, 3Zhejiang University of Technology, China
10:50-11:10
- OS2L-6
- Superconducting-based Power Transmission Architecture Design for Hydrogen Hybrid-electric Aircraft
- Heng Yu, Yulong Li, Enze Ma, Huaqi Lian, Xingjian Li, and Shijie Xu
- Beihang University, China
11:10-11:30
- OS2L-7
- Design Study on High Power Density Quasi-coreless PMSM for Vehicle Traction Drive Rotating at 50,000r/min as the Maximum Speed
- Teruchika Ishihara, Ayaka Sakuma, and Takashi Kosaka
- Nagoya Institute of Technology, Japan
11:30-11:50
Session PS2-1Permanent Magnet Machines 9
- Time:
- 12:00-13:00
- Venue:
- FIT Arena
- PS2-1-1
- Robust Design Considering Assembly Imperfection of 20 W Chip Mounter Motor
- Su-Hwan Kim, Jun-Kyu Kang, Jun-Hyeok Heo, Ikhlaq Ahmad, and Jin Hur
- Incheon National University, Republic of Korea
- PS2-1-2
- Design and Analysis of Service Robot Motor with High Torque and High Back Drivability Focusing on the Torque/inertia Ratio
- Toshihide Yamada1, Yoshihiro Okumatsu1, Hiroyuki Kaimori2, and Hideki Ohguchi3
- 1TOYOTA MOTOR Co., Japan, 2Science Solutions International Laboratory, Inc., Japan, 3Tokai Univ., Japan
- PS2-1-3
- Impact of Partially Demagnetized Permanent Magnets on Operating Range of an Interior Permanent Magnet Synchronous Machine
- Pavel Ogrizek, Mitja Garmut, and Martin Petrun
- University of Maribor, Slovenia
- PS2-1-4
- Selection and Analysis of Rotor Structure for Expansion of IPMSM Operating Range
- Arisa Matsuo, Yusuke Yatsu, and Kenji Suzuki
- Tokyo City University, Japan
- PS2-1-5
- Analysis and Research on the Influence of Different Rotor Structures on the Magnetic Field Characteristics of Machines
- Xiaoyu Liang, Xinyu Dong, Mingqiao Wang, Ping Zheng, Yong Liu, Minghao Wang, and Wei Liu
- Harbin Institute of Technology, China
- PS2-1-6
- Design and Analysis of Axial Flux Motors with Rotor Mechanical Position Observation Capability
- Wei Chen1,2, Xiaogang Lin2, Guohao Jiang2, Tao Zheng2, and Wei Xie2
- 1Fuzhou University, China, 2Chinese Academy of Sciences, China
- PS2-1-7
- Electromagnetic Reduced Order Model of a Permanent Magnet Synchronous Motor
- Grace Firsta Lukman1, Gyeonghwan Yun1, Chansoo Park2, Dongmin Park2, and Cheewoo Lee1
- 1Pusan National University, Republic of Korea, 2LG Electronics, Republic of Korea
- PS2-1-8
- Eddy Current Loss Suppression of Rotor in HSPMSG Considering Skin Effect
- Guodong Yu, Xudong Bai, Haoyi Mu, Yongxiang Xv, and Jibin Zou
- Harbin Institute of Technology, China
Session PS2-2Synchronous Machines 2
- Time:
- 12:00-13:00
- Venue:
- FIT Arena
- PS2-2-1
- Sensorless Rotor Position Estimation and Control for a Three-stage Synchronous Starter-generator
- Shu-An Chin1,2, Min-Fu Hsieh1, Xue-Pin Lu1, Yong-Han Huang1, I-Hsien Lin2, and Kuang-Pin Chen2
- 1National Cheng Kung University, Taiwan, 2National Chung-Shan Institute of Science and Technology, Taiwan
- PS2-2-2
- Characteristic Analysis of Demagnetizing Fault of Pod Propulsion Motor
- Heng Kuang1,2, Yang Xiao1, Zhang Wen1, and Yanan Wang1
- 1Wuhan Institute of Marine Electric Propulsion, China, 2Shenyang University of Technology, China
- PS2-2-3
- Design of Electrically Excited Synchronous Motors for Traction Applications Using Optimisation with Genetic Algorithms
- Leander Philipp Eschenmann1, Christian Nörenberg2, and Bernd Ponick1
- 1Leibniz University Hannover, Germany, 2Audi AG, Germany
- PS2-2-4
- Inductance Measurement of Synchronous Motors with Solid Elements Using Quasi-static Approach Considering Saturation Effects
- Andrea Credo1, Simone Mari1, Federico Centi1, Marco Tursini1, Ilya Petrov2, and Juha Pyrhönen2
- 1University of L’Aquila, Italy, 2Lappeenranta University of Technology, Finland
- PS2-2-5
- Comparison of Hysteresis Motor Output According to Applied Voltage
- Seung-Min Song, Ji-Hoon Han, Eui-Jin Choi, Jong-Hoon Park, and Sun-Ki Hong
- Hoseo University, Republic of Korea
- PS2-2-6
- Torque Ripple Effects According to Hysteresis Motor Closed-slot Structures Geometry with Finite Element Analysis
- Jong-Hoon Park, Ji-Hoon Han, Seung-Min Song, and Sun-Ki Hong
- Hoseo University, Republic of Korea
- PS2-2-7
- Simulation, Design and Optimization of an Electric High-speed Motor with Distributed Tooth-coil Winding
- Marco Garbe1, Daniel Dieterich1, Juri Dolgirev2, Michael Magin1, and Sven Urschel1
- 1Kaiserslautern University of Applied Sciences, Germany, 2EGH Elektro-Geraetebau-Hambruecken, Germany
- PS2-2-8
- A Parallel Hybrid Excitation Brushless Generator Operating Efficiently within Wide-speed Range
- Weijia Jiang, Zhuoran Zhang, Xiangpei Gu, Taiyang Dai, and Changzhou Lu
- Nanjing University of Aeronautics and Astronautics, China
- PS2-2-9
- Research on a New Topology of Asynchronous Excitation Three Stage Brushless Generator without Rotating Rectifier
- Haonan Tian, Zhuoran Zhang, Jincai Li, and Yankun Wang
- Nanjing University of Aeronautics and Astronautics, China
Session PS2-3Reluctance Machines 2
- Time:
- 12:00-13:00
- Venue:
- FIT Arena
- PS2-3-1
- Temperature-rise Determination Test for Synchronous Reluctance Machines Applying Superposition and Equivalent-loading Methods
- Katsutoku Takeuchi1, Makoto Matsushita1, Masatsugu Oyamada2, Sunao Wakasugi2, Yusuke Moriyama2, and Fumiya Koga2
- 1Toshiba Infrastructure Systems & Solutions Corporation, Japan, 2TMEIC Corporation, Japan
- PS2-3-2
- Design and Optimization of a Ferrite Assisted Synchronous Reluctance Motor for New Energy Vehicles
- Bin Chen1,2, Yong Xiao1,2, Xia Li1,2, Xueqiu Han2, Yusheng Hu1,2,3, and Liyi Li3
- 1Guangdong Provincial Key Laboratory of High-Performance Servo System, China, 2GREE ELECTRIC APPLIANCES INC. of ZHUHAI, China, 3Harbin Institute of Technology, China
- PS2-3-3
- Design and Verification of IE6 Ultra Efficiency Line-start Permanent Magnet Assisted Synchronous Reluctance Motor
- Yusheng Hu1,2, Yong Xiao1,2, Jinfei Shi1,2, Bin Chen1,2, Ying Li2, and Liyi Li3
- 1Guangdong Provincial Key Laboratory of High-Performance Servo System, China, 2GREE ELECTRIC APPLIANCES, INC. of ZHUHAI, China, 3Harbin Institute of Technology, China
- PS2-3-4
- Axial Design Guidelines for Torque Ripple Reduction in Additively Manufactured Synchronous Reluctance Rotors
- Marius Schubert and Bernd Ponick
- Leibniz University Hannover, Germany
- PS2-3-5
- Assessments of Permanent-magnet-assisted Synchronous Reluctance Motors for Electric Forklift Applications in Severe Operational Environments
- Cheng-Tsung Liu1, YiYun Fu1, Sheng-Chan Yen2, Ta-Yin Luo2, and Kuan Yang2
- 1National Sun Yat-sen University, TAIWAN, 2Nidec Taiwan Corporation, TAIWAN
- PS2-3-6
- Static Torque Characteristics of SRM with a Threedimensional Gap Structure
- Iori Shimohama1, Kazuhiro Ohyama1, Hiroaki Fujii2, Hitoshi Uehara2, and Yasushi Hyakutake2
- 1Fukuoka Institute of Technology, Japan, 2Meiwa MFG. Co., Ltd., Japan
- PS2-3-7
- Fault-tolerant Control for Power Converter in Switched Reluctance Motor (SRM) Applications
- Paisak Poolphaka1, Pairote Thongprasri2, Ehsan Jamshidpour3, Thierry Lubin4, and Noureddine Takorabet5
- 1,2Kasetsart University Si Racha Campus, Thailand, 3,4,5University of Lorraine, France
- PS2-3-8
- Performance Evaluation of Novel Segmental Rotor Switch Reluctance Motor with Magnetic Bridge
- Sinian Su1, Jianbo Sun1, Shuixi Zhang2, Honggang Wang3, Shuanghong Wang1, Yang Yang1, Ziqi Zhao1, Ronghai Qu1, and Huangyuan Wu4
- 1Huazhong University of Science and Technology, China, 2State Grid Henan Power Company Luohe Power Supply Company, China, 3Henan Tailong Power Equipment Co., Ltd., China, 4Cyan Exploring Power Technology Wuxi Co, China
Session PS2-4Linear Drives and Magnetic Levitations 3
- Time:
- 12:00-13:00
- Venue:
- FIT Arena
- PS2-4-1
- Method for Enhancing the Stability Margin of the Magnetic Bearing-rotor System Based on a Novel Low Frequency Phase Shifter
- Yang Yan1,2, Kun Wang1,2, Shiqiang Zheng1,2, Le Bo1,2, Min Zhang1,2, and Yucheng Ge1,2
- 1Beihang University, China, 2National Institute of Extremely-Weak Magnetic Field Infrastructure, China
- PS2-4-2
- Study of the Basic Charging Characteristics in the Vertical Linear Vibration Power Generator
- Hodaka Kojima, Eiji Shirahama, Ken-ichi Kondo, and Shunsuke Ohashi
- Kansai University, Japan
- PS2-4-3
- Study of Pitching Suppression in a Propulsion and Levitation Integrated Conveyance System Using the Linear Stepper Motor
- Shota Mitsui, Akito Konishi, Ken-ichi Kondo, and Shunsuke Ohashi
- Kansai University, Japan
- PS2-4-4
- Non-contact Hanging for Flexible Steel Plate by Magnetic Levitation: Investigation on Levitating Characteristics in Stationary State
- Rintaro Itoyama1, Ayato Endo1, Jumpei Kuroda2, Daigo Uchino3, Kazuki Ogawa4, Keigo Ikeda5, Taro Kato6, Takayoshi Narita2, and Hideaki Kato2
- 1Fukuoka Institute of Technology, Japan, 2Tokai University, Japan, 3National Institute of Technology, Numazu College, Japan, 4Aichi University of Technology, Japan, 5Hokkaido University of Science, Japan, 6Tokyo University of Technology, Japan
- PS2-4-5
- Placement of Electromagnets for Edge-supported Maglev Systems: Experimental Study on the Relationship between Steady Current and Vibration Characteristics during Electromagnet Direction Change
- Shotaro Baba1, Ayato Endo1, Jumpei Kuroda2, Daigo Uchino3, Kazuki Ogawa4, Keigo Ikeda5, Taro Kato6, Takayoshi Narita2, and Hideaki Kato2
- 1Fukuoka Institute of Technology, Japan, 2Tokai University, Japan, 3National Institute of Technology, Numazu College, Japan, 4Aichi University of Technology, Japan, 5Hokkaido University of Science, Japan, 6Tokyo University of Technology, Japan
- PS2-4-6
- Improvement Technology of Driving-environment Using Two-degree-of-freedom Active Seat Suspension: Design of Ride Comfort by Vibration Control Using Voice Coil Motor
- Eiichi Okamura1, Ayato Endo1, Jumpei Kuroda2, Daigo Uchino3, Kazuki Ogawa4, Keigo Ikeda5, Taro Kato6, Hideaki Kato2, and Takayoshi Narita2
- 1Fukuoka Institute of Technology, Japan, 2Tokai University, Japan, 3National Institute of Technology, Numazu College, Japan, 4Aichi University of Technology, Japan, 5Hokkaido University of Science, Japan, 6Tokyo University of Technology, Japan
- PS2-4-7
- Non-contact Magnetic Suspension for Edge of Flexible Steel Plate: Experimental Consideration on Stable Levitation
- Kazuma Kawashima1, Ayato Endo1, Jumpei Kuroda2, Daigo Uchino3, Kazuki Ogawa4, Keigo Ikeda5, Taro Kato6, Takayoshi Narita2, and Hideaki Kato2
- 1Fukuoka Institute of Technology, Japan, 2Tokai University, Japan, 3National Institute of Technology, Numazu College, Japan, 4Aichi University of Technology, Japan, 5Hokkaido University of Science, Japan, 6Tokyo University of Technology, Japan
- PS2-4-8
- Vibration Control for Flexible Steel Plate during Magnetic Suspension: Suppression of Two-degree-offreedom Vibration by Edge Supported System
- Seita Onitsuka1, Ayato Endo1, Jumpei Kuroda2, Daigo Uchino3, Kazuki Ogawa4, Keigo Ikeda5, Taro Kato6, Takayoshi Narita2, and Hideaki Kato2
- 1Fukuoka Institute of Technology, Japan, 2Tokai University, Japan, 3National Institute of Technology, Numazu College, Japan, 4Aichi University of Technology, Japan, 5Hokkaido University of Science, Japan, 6Tokyo University of Technology, Japan
- PS2-4-9
- Influence of Blade Row Stages on the Pumping Speed of Molecular Pump Based on Entire Blade Row Algorithm
- Hao Li1, Kun wang1, Zhanpeng Cui1, Shiqiang Zheng1, and Yin Zhang2
- 1Beihang University, China, 2Hangzhou Kuntai Maglev Technology Co., Ltd., China
Session PS2-5Induction Machine Control and Drives
- Time:
- 12:00-13:00
- Venue:
- FIT Arena
- PS2-5-1
- Improvement of Control Mode Switching Method for Copper Loss Reduction of Induction Machines
- Ryosuke Kubota1 and Kazuhiro Ohyama2
- 1Fukuoka Institute of Technology, Junior College, Japan, 2Fukuoka Institute of Technology, Japan
- PS2-5-2
- Initial Speed Estimation Method for Induction Motors using Regression Analysis and Self-excited Vibration Phenomenon
- Hiroto Kominami1, Yoshitaka Iwaji1, Naoki Kunihiro2, Kazuma Okuda2, and Takashi Kaneko2
- 1Ibaraki University, Japan., 2Hitachi, Ltd., Japan
- PS2-5-3
- A Novel Speed Measurement Algorithm Based on Linear Extended State Observer for Segmented Linear Induction Motors with Cooperative Control
- Fan Manyi1,2, Liming Shi1,2, Yaohua Li1,2, Fei Xu1,2, and Zhang Bo1
- 1Key Laboratory of High Density Electromagnetic Power and Systems (Chinese Academy of Sciences), China, 2Shandong Key Laboratory of Advanced Electromagnetic Conversion Technology (Institute of Electrical Engineering and Advanced Electromagnetic Drive Technology, Qilu Zhongke), China
- PS2-5-4
- An Improved PLL Control Method for DFIG Under Asymmetric Faults
- Xianglong Kong, Hailiang Xu, Pingjuan Ge, Xiangyu Chen, and Ruitong Mao
- China University of Petroleum (East China), China
- PS2-5-5
- Transient Control of Grid-forming Doubly-fed Induction Generator Considering Power Angle Stability and Fault Current Limitation
- Ruitong Mao, Pingjuan Ge, Hailiang Xu, and Xianglong Kong
- China University of Petroleum (East China), China
Session PS2-6Synchronous Machine Control and Drives
- Time:
- 12:00-13:00
- Venue:
- FIT Arena
- PS2-6-1
- An Open-circuit Fault Diagnosis Method for Single Switch of Controlled Rectifier in Doubly Salient Electromagnetic Generator System
- Wenbo Zhou1, Bo Zhou1, Yijun Zhang1, Wenjing Fang1, and Xie Xie1
- 1Nanjing University of Aeronautics and Astronautics, China
- PS2-6-2
- Reduction of Iron Loss and Back EMFs of the Doubly Salient Synchronous Reluctance Motor by Estimation of Flux Linkage
- Ryo Hasegawa1 and Kyohei Kiyota1
- 1Tokyo Institute of Technology, Japan
- PS2-6-3
- The Loss-minimizing Control Strategy for DSEM Driving System with Current Source Converter
- Sen Wang, Jiadan Wei, Xiangyu Zhai, and Yidi Meng
- Nanjing University of Aeronautics and Astronautics, China
- PS2-6-4
- A High Frequency Square Wave Harmonic Excitation Control Strategy for Self-excited Synchronous Motors
- Yuwei Zhao1,2, Xiaogang Lin1, and Wei Xie1
- 1Chinese Academy of Sciences, China, 2University of Chinese Academy of Sciences, China
- PS2-6-5
- A Novel Brushless Excitation System Capable of Bipolar Field Current Control from the Stator of Electrically/ Hybrid-excited Synchronous Motor
- Shovan Dey, Annoy Kumar Das, and Baylon G. Fernandes
- Indian Institute of Technology Bombay, India.
- PS2-6-6
- Robust Current Predictive Control of Synchronous Reluctance Machines Considering Magnetic Saturation
- Yu Sui, Chong Bao, Haina Sun, and Shoujun Song
- Northwestern Polytechnical University, China
- PS2-6-7
- Efficiency Optimization Control Strategy for Synchronous Reluctance Motor Considering Iron Loss
- Chong Bao, Yu Sui, Chenyi Yang, Lvan Su, Haina Sun, and Shoujun Song
- Northwestern Polytechnical University, China
- PS2-6-8
- Adaptive Dead-time Algorithm to Reduce Current Harmonics in Three-phase Motor Inverters Used for Electric Vehicles
- Nguyen Gia Minh Thao1, Duc-Kien Ngo2, Md Yakub Ali Khan1, Arockia Selvakumar Arockia Doss3, Motoki Ota1, and Keisuke Fujisaki4
- 1Shimane University, Japan, 2University of Danang–University of Technology and Education, Vietnam, 3Vellore Institute of Technology, India, 4Toyota Technological Institute, Japan
- PS2-6-9
- Study on Minimization of Smoothing Capacitor by Increasing Response of Power Supply Converter
- Yoshiya Sato and Yoshitaka Iwaji
- Ibaraki University, Japan
Session PS2-7PM Machine Control and Drives 3
- Time:
- 12:00-13:00
- Venue:
- FIT Arena
- PS2-7-1
- Robust Model Predictive Control Based on Linear Fitting for Surface-mounted Permanent Magnet Synchronous Motor
- Hanrui Wang1,2, Nannan Sun1,2, Chen Li3,4, Youliang Fu1,2, Qinghui Meng1,2, Yanfei Cao4, Guangjie Shao1,2, Fei Wang1,2, and Jing Zhang1,2
- 1Weichai Power Co., Ltd., China, 2State Key Laboratory of Engine and Powertrain System, China, 3Zhejiang University Advanced Electrical Equipment Innovation Center, China, 4Zhejiang University, China
- PS2-7-2
- A Feedback-error-driven Method for Deadbeat Model Predictive Control Algorithm of PMSM
- Zhiman Lu, Jinglin Liu, and Jiasheng Yin
- Northwestern Polytechnical University, China
- PS2-7-3
- Quantitative Neutral Point Voltage Balance-based Modulated Model Predictive Control for Three-level NPC Inverter-fed PMSM Drive
- Guoqian Sun, Chun Gan, Chong Zhang, and Ronghai Qu
- Huazhong University of Science and Technology, China
- PS2-7-4
- A Modified Modulation Strategy for a Five-level Inverter Based Open-end Winding PMSM with Floating Capacitor
- Shuchen Xu, Yang Liang, and Deliang Liang
- Xi’an Jiaotong University, China
- PS2-7-5
- Model-free Current Predictive Control of Permanent Magnet Synchronous Motor based on Ultralocal Model
- Mohan Yang1, Hongfeng Li1, Kexin Yao2, and Haobo Xu1
- 1Tianjin University, China, 2Huazhong University of Science and Technology, China
- PS2-7-6
- Optimized Predictive Power Control of PMSG with Horizon Disturbance Observer
- Zhenxing Cheng1, Liyi Li1, Xiaopeng Li2, Chengbao Zhong3, and Jiaxi Liu1
- 1Harbin Institute of Technology, China, 2China Academy of Engineering Physics, China, 3Gree Electric Appliances, China
- PS2-7-7
- Multi-motor Coordinated Control System of Outer Rotor Permanent Magnet Synchronous Motor
- Biao Hou, Fengge Zhang, and Shi Jin
- Shenyang University of Technology, China
- PS2-7-8
- Implementation of Two-wheel Independence Drive System Based on Indirect Field-oriented and Direct Torque Control Strategies
- Rachain Saita, Satit Owatchaiphong, and Narong Thumputi
- King Mongkut’s University of Technology, Thailand
- PS2-7-9
- PMSM Characteristics Comparison of Rheostatic Brake Circuit Differences Targeted for Electric Hybrid Aircraft
- Shunsuke Noguchi
- Japan Aerospace Exploration Agency, Japan
- PS2-7-10
- Compensation of Speed Synchronization Error of 4-wheel Distributed Drive System based on Fuzzy PI and Virtual PMSM Coupling Control
- Chenkai Ma1, Jianbo Wang1, Liang Han2, Kan Liu1, Wei Hu1, Jing Zhou1, Shichao Zhou1, Kaiqing Li1, and Tao Peng1
- 1Hunan University, China, 2China Railway Rolling Stock Corporation, China
Session PS2-8Multi-winding/Multi-phase Machine Control
- Time:
- 12:00-13:00
- Venue:
- FIT Arena
- PS2-8-1
- A Robust H∞Control Strategy for Enhanced Performance of Multiphase PMSM
- Yongbo Li1, Hongwei Ma1, and Zedong Zheng2
- 1Beijing Institute of Technology, China, 2Tsinghua University, China
- PS2-8-2
- An Improved Deadbeat Direct Torque and Flux Control of Five-phase Permanent Magnet Synchronous Motor
- Yujia Zhang, Yang Shen, Zhenxiao Yin, Yuxuan Liang, and Hang Zhao
- Hong Kong University of Science and Technology (Guangzhou), China
- PS2-8-3
- Direct Torque Control System of Dual Three-phase PMSM with Load Torque Observer
- Dajun Chen, Xiang Li, Ruiwu Cao, Ning Jiang, and Kai Wang
- Nanjing University of Aeronautics and Astronautics, China
- PS2-8-4
- Order Reduction-based Fault-tolerant Decoupling Control for Dual Three-phase PMSM with Two-phase Open-circuit Fault
- Cong Huang, Wei Hu, Kan Liu, Jianbo Wang, Wen Li, Jing Zhou, Tao Peng, Wenrui Liu, and Chenkai Ma
- Hunan University, China
- PS2-8-5
- Fault-tolerant Control Strategies for Dual Three-phase Permanent Magnet Synchronous Machine with YASA Topology under Open-circuit Faults
- Zhihong Liu1, Lingyun Shao1, Zhuoran Zhang1, Xueyi Yan2, and Zhongze Wu2
- 1Nanjing University of Aeronautics and Astronautics, China, 2Southeast University, China
- PS2-8-6
- Research on Fault-tolerant Control Strategy of Dualwinding Permanent Magnet Synchronous Motor
- Shuo Liu1, Shi Jin1, Guangwei Liu1, and Yue Zhang2
- 1Shenyang University of Technology, China, 2Shandong University, China
- PS2-8-7
- Fault-tolerant Control Strategy for Single-phase Open Circuit Fault for Six-phase Doubly Salient Electromagnetic Machine
- Xingwei Zhou1, Shengming Chen1, Peixing Liu2, Shuwen Xu1, and Zefeng Yang1
- 1Hohai University, China, 2State Grid Jibei Electric Power Co., Ltd., China
Session PS2-9Power Converter 1 (DC-DC)
- Time:
- 12:00-13:00
- Venue:
- FIT Arena
- PS2-9-1
- Fuzzy Neural Nonsingular Terminal Sliding Mode Control of DC-DC Buck Converter
- Xiaoyu Gong and Juntao Fei
- Hohai University, China
- PS2-9-2
- Complete Soft Switching Implementation Based on LCC-LCC Compensation Network for Wireless Power Transfer System
- Xi Zhang, Han Guang, Qingxiang Xie, and Qianfan Zhang
- Harbin Institute of Technology, China
- PS2-9-3
- Power Optimization Strategy for Buck Circuits Based on Digital Twins
- Yuang Luo1,2, Lu Zhao1, Yikesha Halimulati1,2, Qiongxuan Ge1, Shi Cheng1,2, and Yuhang Chi1,2
- 1Chinese Academy of Sciences, China, 2University of Chinese Academy of Sciences, China
- PS2-9-4
- Back-flow Power Optimization Strategy of DAB Converter with Extended Phase Shift Control
- Hongwei Fang1, Weijie Wang1, Fan Jiang2, and Yike Du1
- 1Tianjin University, China, 2China Institute of Marine Technology & Economy, China
- PS2-9-5
- DC-link Capacitor Lifetime Extension for Two-level Back-to-back Converters Based on Zero-sequence Voltage Injection
- Qiuqiong Lin, Ziyu Wei, and Pinjia Zhang
- Tsinghua University, China
Session PS2-10Power Converter 2 (AC-DC, DC-AC)
- Time:
- 12:00-13:00
- Venue:
- FIT Arena
- PS2-10-1
- A New Hybrid Modulation Method with Low Current Distortion and Switching Losses for Single-phase Threelevel Inverters
- Paiboon Kiatsookkanatorn1, Phongsathorn Sangsuwan1, Prachuab Iamsamang2, and Somboon Sangwongwanich3
- 1Rajamangala University of Technology Suvarnabhumi (RUS), Thailand, 2Bangkokthonburi University, Thailand, 3Chulalongkorn University, Thailand
- PS2-10-2
- Improved Capacitor Voltage Balancing Method for CHB Inverter Based on Hybrid Modulation Strategy and Reference Voltage Reconfiguration
- Ye Zhang1,2, Zixin Li1,2, Fanqiang Gao1,2, Cong Zhao1,2, and Yaohua Li1,2
- 1Chinese Academy of Sciences, China, 2University of Chinese Academy of Sciences, China
- PS2-10-3
- Carrier-based Discontinuous PWM Strategy by Switching Clamp Modes for Vienna Rectifier with Unbalanced DC-links
- Zhijian Zhang1, Bingxing Li1, Li Ding1, Nannan Zhao2, Ziming Hu2, Chengrui Li3, Gaolin Wang1, and Dianguo Xu1
- 1Harbin Institute of Technology, China, 2Midea Group, China, 3Harbin Institute of Technology (Shenzhen), China
- PS2-10-4
- Control of Quick Charger System Applying MMC with High Frequency AC Output
- Shin-ichi Hamasaki, Kazuhiro Inoue, and Tetsuji Daido
- Nagasaki University, Japan
- PS2-10-5
- A Compact Hybrid Multilevel Converter with Wide Operation Range
- Xiaoyin Wu, Yuhua Gao, Yi Wang, Rui Wang, and Xiaoqi Xu
- North China Electric Power University, China
- PS2-10-6
- Control of Variable Speed Pumped Storage Unit Based on Power Electronic Transformer Under Unbalance of Power Grid Voltage
- Pei Huang (Corresponding Author), Xiang Peng, and Renjun Dian
- Wuhan University of Science and Technology, China
- PS2-10-7
- Three-phase to Single-phase Matrix Converter that Suppresses Voltage Fluctuations during Load Changes
- Akito Murata and Naoki Yamamura
- Mie University, Japan
- PS2-10-8
- Common Mode Voltage Suppression Method for Thirdharmonic Injection Two-stage Matrix Converter in Low Modulation Ratio
- Yaotian Shi, Bo Zhou, Chengjia Lu, Qingyun Chang, and Yang Huang
- Nanjing University of Aeronautics and Astronautics, China
- PS2-10-9
- IPF Improvement of DPWM-controlled for DMC with a Double PI Controller
- Sahel Solemanifard and Tzung-Lin Lee
- National Sun Yat-sen University, Taiwan
Session PS3-1Linear Drives and Magnetic Levitations 4
- Time:
- 13:00-14:00
- Venue:
- FIT Arena
- PS3-1-1
- Design and Optimization of a Permanent Magnet biased Hybrid Magnetic Bearing for Turbo-molecular Pump
- Kaixuan Wang1,2, Di Wang1,2, and Yun Le1,2
- 1Beihang University, China, 2National Institute of Extremely-Weak Magnetic Field Infrastructure, China
- PS3-1-2
- Model Calibration of Inconsistent Coils Shape Driven by Coupling Effect of Magnetic Levitation Planar Motor
- Fuxiang Chen, Kai Liu, Yingtong Wu, Aoqi Hu, Xinpeng Wei, Cailin Hong, and Lizhan Zeng
- Huazhong University of Science and Technology, China
- PS3-1-3
- Influence of Secondary Structure on the Transverse Edge Effect of LP-DSLIM
- Zhuo Zhang1,2, Yumei Du1,2, Yongxian Liu1,2, Ruihua Zhang1,2, and Liming Shi1,2
- 1Chinese Academy of Sciences, China, 2University of Chinese Academy of Sciences, China
- PS3-1-4
- Modal Vibration Control of Magnetic Bearing Rotor System Based on Second Order Generalized Integratorgradient Estimator
- Zhengpu Chen, Jun Liu, and Jinxiang Zhou
- Beihang University, China
- PS3-1-5
- Simulation of Vibration Characteristics of Magnetically Levitated Steel Plate under Disturbance Condition
- Kazuki Ogawa1, Yamato Uchida2, Ikkei Kobayashi2, Jumpei Kuroda2, Keigo Ikeda3, Taro Kato4, Ayato Endo5, Takayoshi Narita2, and Hideaki Kato2
- 1Aichi University of Technology, Japan, 2Tokai University, Japan, 3Hokkaido University of Science, Japan, 4Tokyo University of Technology, Japan, 5Fukuoka Institute of Technology, Japan
- PS3-1-6
- Analysis and Control of Self-sensing Model of Isolated Axial Magnetic Bearing
- Rui Zhang, Ning Wang, Hao Wu, and Liwei Song
- Harbin Institute of Technology, China
- PS3-1-7
- Structural Optimization Design of Permanent Magnet Linear Force Motor for Aviation
- Yuyuan Yang, Jinglin Liu, Xinran Shi, and Feiyang Liu
- Northwestern Polytechnical University, China
- PS3-1-8
- The Method of Single-segment Layer-by-layer Substitution for Inverse Design of Passive Magnetic Springs
- Rui Zhou, Cailin Hong, Lifeng Fu, Wei Zhang, Yumei Bai, Wei Jiang, and Jiulin Wu
- Huazhong University of Science and Technology, China
- PS3-1-9
- Research on Optimization Design of Double-sided Consequent-pole Permanent Magnet Synchronous Linear Motor
- Jing Li, Xuzhen Huang, Qiang Tan, Zheng Wang, Yue Yang, and Yansong Liu
- Nanjing University of Aeronautics and Astronautics, China
Session PS3-2Flux Switching & Variable Flux Machines 2
- Time:
- 13:00-14:00
- Venue:
- FIT Arena
- PS3-2-1
- Investigation of Design Methods to Improve the Performance of a Motor Which is Capable of Switching between WFFSM Drive and SynRM Drive
- Iori Kokubo and Kyohei Kiyota
- Tokyo Institute of Technology, Japan
- PS3-2-2
- Study on Pole-slot Combinations of Half-wave Rectified Variable Field Flux Motor with Axial Gap Structure
- Kentaro Yazama1, Takashi Abe1, Yoshitsugu Otomo1, and Takahiro Koga1,2
- 1Nagasaki University, Japan, 2ANSYS Japan K.K., Japan
- PS3-2-3
- Experimental Validation of a Six-pole Half-wave Rectified Variable Field Flux Motor
- Shu Yoshida1, Takashi Abe1, Yoshitsugu Otomo1, and Takahiro Koga1,2
- 1Nagasaki University, Japan, 2ANSYS Japan K.K., Japan
- PS3-2-4
- Design Study on Hybrid Excitation Generator for Microhydroelectric System
- Kazuto Maruyama1, Takashi Kosaka1, Yasushi Kato1,2, Naoki Yamamoto2, Yoshiki Yasuda2, and Akio Yamagiwa2
- 1Nagoya Institute of Technology, Japan, 2Daikin Industries, Ltd., Japan
- PS3-2-5
- Comparison of Variable Flux Memory Machine and Double-variable Flux Memory Machine with Hybrid Magnetic Circuits
- Xianxian Zeng, Heyun Lin, Yuxiang Zhong, Xifang Zhao, and Hui Yang
- Southeast University, China
- PS3-2-6
- Design and Analysis of Variable Flux Motor with Rotatable Magnet
- Daiki Gotoh and Masayuki Kato
- Ibaraki University, Japan
- PS3-2-7
- Field Unit Type Magnet-assisted Wound Field Motor for HEV and EV Applications with Distributed Mortise Structure
- Yuki Hidaka1, Kengo Adachi1, and Daisuke Sato2
- 1Nagaoka University of Technology, Japan, 2Nagaoka Motor Development Co., Ltd., Japan
Session PS3-3Special Machines
- Time:
- 13:00-14:00
- Venue:
- FIT Arena
- PS3-3-1
- Precise Prediction of Air-gap Magnetic Harmonics for IPMSM Based on Improved Magnetic Field Modulation Theory
- Jiyuan Ma, Yu Zeng, Wenxiang Zhao, Jinghua Ji, Qingze Hu, and Chen Jia
- Jiangsu University, China
- PS3-3-2
- A Novel Equivalent Magnetic Network Method for Permanent Magnet Vernier Motor
- Hongwei Fang1, Hang Ye1, Yike Du1, Zhaoxia Xiao2, and JinGuo Zhang1
- 1Tianjin University, China, 2Tiangong University, China
- PS3-3-3
- Scaling Effect Analysis of Surface-mounted Permanent Magnet Vernier Machine with Concentrated Windings
- Junzhou Li, Yuting Gao, Yuanzhi Zhang, and Xiaoming Zha
- Wuhan University, China
- PS3-3-4
- A Novel Consequent-pole Vernier Permanent Magnet Machine with Dual Armature Winding Configuration
- Qiang Wang1, Renjun Dian1, Wenyu Yan1, and Linjie Ren2(Corresponding Author)
- 1Wuhan University of Science and Technology, 2Tsinghua University, China
- PS3-3-5
- A High Strength and Low Cogging Torque Modulator Structure for Magnetic-geared Machines
- Junjie Tao1, Dong Wei1, Kan Liu1, Zi-Qiang Zhu2, Yan Ding1, Huaqiang Cai1, Jinya Chen1, Zhiwei Zhao1, and Hongdong Wu3
- 1Hunan University, China, 2University of Sheffield, UK, 3Hengtong Marine Cable Systems Co., Ltd., China
- PS3-3-6
- Optimization of Repulsion Cycloidal Magnetic Gear with Inset Radial Magnets
- Pin-Hao Liao, Mi-Ching Tsai, Po-Wei Huang, and Tsung-Wei Chang
- National Cheng Kung University, Taiwan
- PS3-3-7
- A Novel Model for Hybrid Stepper Motors Considering Magnetic Saturation
- Yu-Chen Kuo and Min-Fu Hsieh
- National Cheng Kung University, Taiwan
- PS3-3-8
- Comparative Analysis of Tangentially Magnetized Stator-permanent-magnet Hybrid Stepping Machines with Four, Five and Six-tooth
- Xiaobao Chai, Jinglin Liu, Minglang Xiao, Zhiman Lu, and Ruizhi Guan
- Northwestern Polytechnical University, China
- PS3-3-9
- Experimental Verification of Distribution Factors in Counter-rotating Twin Harmonic PM Machines
- Michiel Desmedt, Thomas Hepsøe, and Robert Kristoffer Nilssen
- NTNU, Norway
- PS3-3-10
- A Novel High-speed Solid Rotor Induction Motor with Equidirectional Toroidal Rectangular Winding
- Peixin Wang, Yinjun Sun, Jikai Si, Rui Nie, and Shuai Xu
- Zhengzhou University, China
Session PS3-4Bearingless Machine 2
- Time:
- 13:00-14:00
- Venue:
- FIT Arena
- PS3-4-1
- Analysis of Fundamental Electromagnetic Performance of Stator Permanent Magnet Bearingless Slice Motor Topology
- Wenqing Hao, Zhiquan Deng, and Ying Xiong
- Nanjing University of Aeronautics and Astronautics, China
- PS3-4-2
- Proposal of Pediatric Centrifugal Pump Type Ventricular Assist Device Using a Bearingless Motor
- Yusuke Yatsu, Arisa Matsuo, Satoshi Murayama, and Kenji Suzuki
- Tokyo City University, Japan
- PS3-4-3
- Reduction of Force Error Angle by Flux-strengthening Control in Two-axis Actively Positioned Bearingless PM Motor
- Keita Kajino and Hiroya Sugimoto
- Tokyo Denki University, Japan
- PS3-4-4
- Characteristics Analysis of Novel Permanent Magnet Biased Bearingless Switched Reluctance Motor
- Zhenyao Xu1, Yifan Sun1, Cheng Huang1, Guangwei Liu1, Dong-Hee Lee2, and Shuo Wang3
- 1Shenyang University of Technology, China, 2Kyungsung University, Republic of Korea, 3University of Nottingham Ningbo China, China
- PS3-4-5
- Variable Gain Control of Nonlinear Suspension Force for Bearingless Doubly Salient Electromagnetic Motor Under Magnetic Saturation
- Haonan Zou, Li Yu, Wei Chen, Zhongshan Luo, and Zhuoran Zhang
- Nanjing University of Aeronautics and Astronautics, China
- PS3-4-6
- Sensorless Control of PMa-BSynRM Based on ISWATS Adaptive Neural Network Left Inverse Soft-sensing Technique
- Yichen Liu, Huangqiu Zhu, and Yizhou Hua
- Jiangsu University, China
- PS3-4-7
- Calculation of Eddy Current Loss in Surface Permanent Magnet Rotor Due to Suspension Flux in High Power Bearingless Motors
- Taichi Konno1, Hiroya Sugimoto1, Minoru Yoshida2, Chiharu Sumiyama2, and Tomoya Ishigami2
- 1Tokyo Denki University, Japan, 2Maruwa Electronic Inc., Japan
- PS3-4-8
- Decoupling of Magnetic Circuits between Combined Radial-axial Magnetic Bearing and Permanent Magnet Bearingless Motor
- Hisato Nakamura1, Taichi Konno1, Hiroya Sugimoto1, Minoru Yoshida2, Ryo Takashima2, Chiharu Sumiyama2, and Tomihiro Kinjo3
- 1Tokyo Denki University, Japan, 2Maruwa Electronic Inc., Japan, 3Japan Aerospace Exploration Agency, Japan
- PS3-4-9
- Comparison and Design Optimization of Consequentpole and Multi-monopole Surface Permanent Magnet Bearingless Motors
- Shouma Kono1, Hiroya Sugimoto1, and Takahiro Noguchi2
- 1Tokyo Denki University, Japan, 2University of Minnesota, USA
- PS3-4-10
- Optimization Design of Hybrid Excitation Bearingless Permanent Magnet Synchronous Generator
- Yuchen Zhu, Xijun Hua, Yizhou Hua, and Yichen Liu
- Jiangsu University, China
Session PS3-5Parameter Estimation
- Time:
- 13:00-14:00
- Venue:
- FIT Arena
- PS3-5-1
- Maximum Torque per Ampere Control of Variable Flux Memory Motor Based on Online Parameter Identification
- Ziqiang Zhang, Ruiqing Ma, Weizhou Yang, Ping Fan, and Peng Chen
- Northwestern Polytechnical University, China
- PS3-5-2
- Position Offset Injection Based Winding and Permanent Magnet Temperature Decoupled Estimation for PMSMs
- Yuting Lu1, Beichen Ding1, and Guodong Feng1,2
- 1Sun Yat-sen University, China, 2Guangdong Provincial Key Laboratory of Fire Science and Intelligent Emergency Technology, China
- PS3-5-3
- Multi-objective Optimization Three-vector-based Model Predictive Current Control with Adaline Online Parameter Identification for PMSM Drives
- Pengbo ZHAO, Zeyu ZAHNG, Jien MA, Lin QIU, and Youtong FANG
- Zhejiang University, China
- PS3-5-4
- Fundamental Study of On-line Inductance Identification for IPMSM
- Keita Ui and Yoshitaka Iwaji
- Ibaraki University, Japan
- PS3-5-5
- The Full Rank Identification of DTP-PMSM Parameters
- Xiang Li, Dajun Chen, Ruiwu Cao, Kai Wang, and Ning Jiang
- Nanjing University of Aeronautics and Astronautics, China
- PS3-5-6
- Online Parameters Identification for an IPMSM Based on Extended Kalman Filter
- Khanaphot Treebubpha, Sompob Polmai, and Supat Kittiratsatcha
- King Mongkut’s Institute of Technology Ladkrabang, Thailand
- PS3-5-7
- Position Offset and Current Angle Combined Injection Based Online Multiparameter Estimation of PMSM Considering Inverter Distortion
- Yuheng Pei1, Zhe Tong1, and Guodong Feng1,2
- 1Sun Yat-sen University, China, 2Guangdong Provincial Key Laboratory of Fire Science and Intelligent Emergency Technology, China
Session PS3-6Switched Reluctance Machine Control and Drives
- Time:
- 13:00-14:00
- Venue:
- FIT Arena
- PS3-6-1
- A Novel SMO Based Diagnosis Method for Interturn Short-circuits in SRM by Unaligned Inductance Identification
- Qiyuan Cheng, Shoujun Song, Chenyi Yang, Chong Bao, and Qingkun Yang
- Northwestern Polytechnical University, China
- PS3-6-2
- Levitation Displacement Control of Bearingless Switched Reluctance Motor with UDE-based Method
- Qiang Cui and Xin Cao
- Nanjing University of Aeronautics and Astronautics, China
- PS3-6-3
- Research on Direct Instantaneous Torque and Suspension Force Control Strategy for Stepped Rotor Bearingless Switched Reluctance Motor
- Zhenyao Xu1, Fengzhi Ning1, Huijun Wang2, Dong-Hee Lee3, and Shuo Wang4
- 1Shenyang University of Technology, China, 2Beihang University, China, 3Kyungsung University, Republic of Korea, 4University of Nottingham Ningbo, China
- PS3-6-4
- Validation of Variable Voltage Control Method Using Z-source Inverter for SRM Drive
- Satoshi Murayama, Yusuke Yatsu, and Kenji Suzuki
- Tokyo City University, Japan
- PS3-6-5
- High-performance Starting Control Strategy for Switched Reluctance Starter/Generator
- Qingkun Yang, Shoujun Song, Chenyi Yang, Qiyuan Cheng, and Chong Bao
- Northwestern Polytechnical University, China
- PS3-6-6
- LADRC-based High Dynamic Control Strategy for SRMbased EMA System
- Jiabao Bu1, Jinhua Du1, Yun Long1, Guoqiang Zhang1, Peng Kou1, and Zhanqiang Luo2
- 1Xi’an Jiaotong University, China, 2AVIC of China Qing’an Group Co, China
- PS3-6-7
- Research on Voltage Stabilizing System of Switched Reluctance Motor Based on Fuzzy PID Control
- Tong Chang, Shuanghong Wang, and Zixin Li
- Huazhong University of Science and Technology, China
- PS3-6-8
- Fault-tolerant Sensorless Control Method Based on Multiple Second Order Generalized Integrator for SRM Drives
- Dexu Lv1, Kai Wang2, Wen Ding1, and Yangfan Wang1
- 1Xi’an Jiaotong University, China, 2Hudong Heavy Machinery Co., Ltd., China
- PS3-6-9
- An Inductance-slope-based Sensorless Control Method for Switched Reluctance Motor
- Fanyan Zeng, Shuanghong Wang, and Zixin Li
- Huazhong University of Science and Technology, China.
Session PS3-7Torque Ripple Suppression Control
- Time:
- 13:00-14:00
- Venue:
- FIT Arena
- PS3-7-1
- Torque Ripple Suppression Strategy Based on Quasiresonant Active Disturbance Rejection Control for PM/ RHR-DSLSSM
- Shukai Wen1, Shi Jin1, Wuhen Jin1, Siyang Yu1, and Zhaoyu Zhang2
- 1Shenyang University of Technology, China, 2Dalian Zhiding Technology Co., Ltd., China
- PS3-7-2
- Torque Ripple Reduction Control of Axial Rotorstaggered Permanent Magnet Reluctance Motor Using Nonlinear Extend State Observer
- Guoqiang Zhang and Jinhua Du
- Xi’an Jiaotong University, China
- PS3-7-3
- A Novel Torque Ripple Mitigation Control Method for Single-phase PMSM Based on Virtual Multi-phase Algorithm
- Lijian Wu1, Yu Xia1, Tao Wang1, Xiubiao Yang2, and Wenzhi Wang2
- 1Zhejiang University, China, 2Jiaxipera Compressor Co., Ltd., China
- PS3-7-4
- Harmonic Injection-based Torque Ripple Suppression Strategy for Synchronous Reluctance Motor
- Haina Sun, Chong Bao, Yu Sui, Chenyi Yang, Qiyuan Cheng, and Shoujun Song
- Northwestern Polytechnical University, China
- PS3-7-5
- Torque Ripple Suppression Control Using Parallel Resonant Controller and ANN in Position and Acceleration Sensorless Control of Stepping Motor
- Mizuki Miyata and Sari Maekawa
- Meiji University, Japan
Session PS3-8Power Converter 3 (WPT)
- Time:
- 13:00-14:00
- Venue:
- FIT Arena
- PS3-8-1
- Bidirectional SP-type Wireless Power Transfer System Based on Parity-time Symmetry Condition
- Ryota Aratani, Yuki Shimizu, and Yoshitaka Kawabata
- Ritsumeikan University, Japan
- PS3-8-2
- Determination Scheme of Ferromagnetic Metal Objects Using Detection Coil in Wireless Power Transfer
- Seung Ahn Chae1, Min Seung Song1, Dae Yong Um2, and Gwan Soo Park1
- 1Pusan National University, Republic of Korea, 2Gyeongsang National University, Republic of Korea
- PS3-8-3
- Estimation of Transmitter Inductance on Foreign Object in Wireless Power Transfer
- Min Seung Song, Seung Ahn Chae, and Gwan Soo Park
- Pusan National University, Republic of Korea
- PS3-8-4
- Frequency-based Power Distribution via Virtual AC Bus for Dual-frequency Wireless Energy Router System
- Mingkai Yang, Gang Wang, Liyuan Liu, and Xuemin Tan
- Chengdu University of Information Technology, China
- PS3-8-5
- Power Factor Improvement Control of Variable Active Capacitor System for Wireless Power Transfer
- Tomohiro Asari, Shin-ichi Hamasaki, and Tetsuji Daido
- Nagasaki University, Japan
- PS3-8-6
- A Vehicle-to-vehicle (V2V) Mode in Multi-receiver WPT System Utilizing Transmitting Loop from Primary Compensation Circuit
- Kan Voottipruex1, Hatta Sawachan1, Suriyotai Supanyapong1, Supapong Nutwong2, Nattapong Hatchavanich2, and Ekkachai Mujjalinvimut2
- 1King Mongkut’s University of Technology, Thailand, 2King Mongkut’s University of Technology Thonburi, Thailand
- PS3-8-7
- Wireless Power Transfer System for Multiple Drones In-flight Charging Applications under Wide Charging Tolerance with Constant Charging Current
- Kasan Sukvanachaikul, Nattapong Hatchavanich, Supapong Nutwong, Sumate Naetiladdanon, Anawach Sangswang, and Ekkachai Mujjalinvimut
- King Mongkut’s University of Technology Thonburi, Thailand
Session PS3-9Power Electronics of Mobility Applications
- Time:
- 13:00-14:00
- Venue:
- FIT Arena
- PS3-9-1
- Time-efficient Power Loss Calculation for Batteryelectric Powertrains Based on Harmonic Loss Models
- Maximilian Hagedorn1, Cornelius Rettner2, Mathias Korn3, and Axel Mertens1
- 1Leibniz University Hannover, Germany, 2Volkswagen AG, Germany, 3Audi AG, Germany
- PS3-9-2
- Active Power Decupling Strategy for Integrated Singlephase Charging System of EVs with Dual-battery
- Yidi Meng1, Jiadan Wei1, Gaofeng Li1, Zeyu Zhang1, and Le Zhang2
- 1Nanjing University of Aeronautics and Astronautics, China, 2Wuxi Taihu University, China
- PS3-9-3
- Modeling and Control of a Hybrid Power System for Electric Propulsion Aircraft
- Siyang Liang1, Hongwei Zhao1, Tao Yang2, Xin Wang2, Yang Qi1, and Weilin Li1
- 1Northwestern Polytechnical University, China, 2University of Nottingham, UK
- PS3-9-4
- A Capacity Planning Method for EV Charging Stations Based on Fuzzy C-means Clustering and Deep Extreme Learning Machine
- Bohao LIANG1, Xiangyu KONG1, Jidong WANG1, Mingxuan LU2, Longyu ZHANG1, and Mao LIU1
- 1Tianjin University, China, 2State Grid Liaoning Electric Power Company Economic and Technical Research Institute, China
- PS3-9-5
- CFD Thermal Analysis of Axial-flux Permanent Magnet Synchronous Motor with Water Cooling Channels for Underwater Propulsion Applications
- Jang-Hyun Park1, Jae-Gil Lee1, Yeon-Ho Jeong1, Kwangdeok Kim2, Ilhwan Park2, and Do-Kwan Hong1
- 1Korea Electrotechnology Research Institute, Republic of Korea, 2Hyosung Heavy Industries Corporation, Republic of Korea
- PS3-9-6
- Design of a 100 kW SPMSM for Podded Propulsion and Multiphysics Analysis of Fault Operating Simulation
- Da-Eun Kim1,2, Jang-Hyun Park1,2, Jae-Gil Lee1,2, Yeon-Ho Jeong2, and Do-Kwan Hong1,2
- 1University of Science and Technology, Republic of Korea, 2Korea Electrotechnology Research Institute, Republic of Korea
- PS3-9-7
- Analysis of the Battery Capacity and Imbalanced Charging Ability for a Cascade H Bridge in Shinkansen Regeneration Energy Storage Application
- Zhaoyang Jin1, Keiichiro Kondo1, Kentaro Nishi2, and Rika Saito2
- 1Waseda University, Japan, 2R&D Center of JR East Group, Japan
- PS3-9-8
- Mass Reduction of a PMSM through Segmented Stator and Material Mix by Holistic Drivetrain Consideration
- Maximilian Clauer1, David Bauer1, and Nejila Parspour2
- 1Dr. Ing. h.c. F. Porsche AG, Germany, 2University of Stuttgart, Germany
- PS3-9-9
- Sliding Mode Control Method Based on FLC for Performance Improvement of PMD Battery Charger
- Gyuri Kim and Yeongsu Bak
- Keimyung University, Republic of Korea
- PS3-9-10
- Solution of Active Safety for Virtual Track Train Based on RRT* and MPC
- Zhipeng Jing, Zhenggang Lu, Zehan Wang, Juyao Wei, and Zheng Yin
- Tongji University, China
Session PS3-10Control of Power Converter
- Time:
- 13:00-14:00
- Venue:
- FIT Arena
- PS3-10-1
- Improved Current Limiting Control for LVRT Strategy of Virtual Synchronous Generator
- Hongwei Fang1, Yuwei Yin1, Zhaoxia Xiao2, and Junjie Xiong3
- 1Tianjin University, China, 2Tiangong University, China, 3State Grid Jiangxi Electric Power Research Institute, China
- PS3-10-2
- Generic Algorithm Based Parameter Optimization for an S-SP Compensation Topology Based Inductive Power Transfer System
- Yu Chen1, Li Gao1, Kan Liu1, Pengfei Sang1, Liang Han2, Haozhe Luan1, Kanglong He1, and Hongdong Wu3
- 1Hunan University, China, 2China Railway Rolling Stock Corporation, China, 3Hengtong Marine Cable Systems Co., Ltd., China
- PS3-10-3
- A Variable-frequency and Phase-shifted Based Current Sharing Control for Parallel LLC Resonant Converters with Parameter Differences
- Kanglong He1, Li Gao1, Liang Han2, Kan Liu1, Haozhe Luan1, Kaiqing Li1, Wei Li1, and Pengfei Sang1
- 1Hunan University, China, 2China Railway Rolling Stock Corporation, China
- PS3-10-4
- A Half Controlled Current Source Actively Commuted Converter with the Low Switching Frequency Modulation Strategy
- Hang Zhang1, Zixin Li1, Fanqiang Gao1, Xiangming Lyu2, Cong Zhao1, Fei Xu1, and Yaohua Li1
- 1Chinese Academy of Sciences, China, 2Northeastern University at Qinhuangdao, China
- PS3-10-5
- Suppression of Second Harmonic Current by Active Power Decoupling Circuit Based on Bus Voltage Feedforward
- Pan Li, Jianyong Su, Han Wang, and Guijie Yang
- Harbin Institute of Technology, China
- PS3-10-6
- Investigation on Error Decomposition-based Feedback Control Strategy
- YE Siwen, SHEN Yihe, WEI Mingou, YANG Xijun, and GAO Fei
- Shanghai Jiao Tong University, China
- PS3-10-7
- Multi-objective Coordinated Control of Permanent Magnet Direct-drive Wind Power System Under Asymmetrical Grid Fault
- Xingwei Zhou, Shuwen Xu, Shengming Chen, Zefeng Yang, and Tianyu Fang
- Hohai University, China
- PS3-10-8
- Current Harmonic Suppression Strategy for Gridconnected NPC Converters at Low Switching Frequencies
- Zexi Liang1,2, Ruihua Zhang1,2, Bo Zhang1,2, and Qiongxuan Ge1,2
- 1Chinese Academy of Sciences, China, 2University of Chinese Academy of Sciences, China
- PS3-10-9
- Fault-tolerant Strategy for More Reliable Cascaded H-bridge Inverters
- Min-Sol Kim1, Ju-Yoen Baek2, Kyo-Beum Lee2, and Youngjong Ko3
- 1Pukyong National University, Republic of Korea, 2Ajou University, Republic of Korea, 3Pukyong National University, Republic of Korea
Session OS3BBearingless Machine 1
- Time:
- 14:30-16:30
- Venue:
- Room: B
- Chair:
- Osamu Ichikawa (Polytechnic University, Japan), Wolfgang Gruber (Johannes Kepler University Linz, Austria)
- OS3B-1
- Homopolar Bearingless Slice Motor with Single-phase Suspension Windings
- Ying Xiong, Zhiquan Deng, Xin Cao, and Wenqing Hao
- Nanjing University of Aeronautics and Astronautics, China
14:30-14:50
- OS3B-2
- Combined Winding Design for Improving Suspension Force Characteristics of Bearingless Motors
- Zikai Yang, Yu Hu, and Jiahao Chen
- ShanghaiTech University, China
14:50-15:10
- OS3B-3
- Five-degree-of-freedom Active-suspended Axial Gap Self-bearing PMSM with Double Inner Stator
- Satoshi Ueno, Kazuki Hara, and Chengan Zhao
- Ritsumeikan University, Japan
15:10-15:30
- OS3B-4
- Proposal of 2-DOF Actively Controlled Consequentpole-type Bearingless Single-phase Motor Using Zero-sequence Current
- Kaito Tanaka, Yusuke Fujii, and Akira Chiba
- Tokyo Institute of Technology, Japan
15:30-15:50
- OS3B-5
- Rotor Design Study for Exterior Rotor Bearingless Permanent Magnet Machines
- Tengrui Shi1, Xiaolin Wang1, Xucong Bao1, Qiang Ding2, Zhenglong Li1, and Zhenxue Fan1
- 1Nanjing University of Aeronautics and Astronautics, China, 2Nanjing Vocational University of Industry Technology, China
15:50-16:10
- OS3B-6
- Development of Asymmetrical Four-phase Bearingless Motor with Unequal-tooth-pitch Stator
- Yoshinori Kamiya and Junichi Asama
- Shizuoka University, Japan
16:10-16:30
Session OS3CMultiphase Machines
- Time:
- 14:30-16:30
- Venue:
- Room: C
- Chair:
- Hiroyuki Kaimori (Science Solutions International Laboratory, Inc., Japan), Huanran Wang (Zhejiang University, China)
- OS3C-1
- Operation Principle of a Novel Coaxial Triple-DOF Motor
- Yiyang Xu1, Jian Wang1,2, Tingna Shi1,2, Dong Yan1, Hao Chen1, and Yanfei Cao1
- 1Zhejiang University, China, 2Advanced Electrical Equipment Innovation Center, China
14:30-14:50
- OS3C-2
- Minimization Copper Loss Full Range for Single-phase Open-circuit Fault Tolerant Control in Five-phase SPMSM with Non-sinusoidal Back EMF
- Huanran Wang1, Xiangqian Huang2, Xiaoyan Huang1, Zhuo Chen1, Ang Liu1, Hui Xu1, Han Zhao3, and Chunyang Gu3
- 1Zhejiang University, China, 2Hangzhou Three Phases Technology Co., Ltd., China, 3Yongjiang Laboratory, China
14:50-15:10
- OS3C-3
- Five-phase PMSM Fault-diagnostic Strategy Based on Symmetrical Component Method for Weak Inter-turn Short-circuit Fault
- Qifan Xiao, Mingqiao Wang, Wei Liu, Ziyu Zhou, Xiaoying Qiu, and Ping Zheng
- Harbin Institute of Technology, China
15:10-15:30
- OS3C-4
- Experimental Comparison of a Three- and Five-phase Squirrel Cage Induction Machine
- Alexander Möller, Andreas Binder, and Yves Burkhardt
- Technical University of Darmstadt, Germany
15:30-15:50
- OS3C-5
- Comparison of Electromagnetic and Vibration Performances of Dual Three-phase and Multiphase SPM Motors
- Hironori Minegishi, Yusuke Fujii, and Akira Chiba
- Tokyo Institute of Technology, Japan
15:50-16:10
- OS3C-6
- Reduction of Carrier Harmonic Iron Loss of Phase-shift Windings Dual Three-phase Motors by Phase Current-shift Control
- Yoshihiro Miyama1 and Kan Akatsu2
- 1Mitsubishi Electric Corporation, Japan, 2Yokohama National University, Japan
16:10-16:30
Session OS3DFlux-Modulated Machines
- Time:
- 14:30-16:30
- Venue:
- Room: D
- Chair:
- Yuki Hidaka (Nagaoka University of Technology, Japan), Ronghai Qu (Huazhong University of Science and Technology, China)
- OS3D-1
- Torque-to-weight Ratio Improvement of Large-scale Magnetic Gears for Offshore Wind Power Generation
- Takanori Sumi1, Akihiro Okazaki1, Kenji Nakamura1, Tomokazu Shinji2, and Keiji Takeda2
- 1Tohoku University, Japan, 2TDK Corporation, Japan
14:30-14:50
- OS3D-2
- Frequency Response Analysis of Magnetic Coupling and Magnetic Gear
- Keigo Iwaki and Kenji Nakamura
- Tohoku University, Japan
14:50-15:10
- OS3D-3
- Design and Analysis of Magnetic Gear for Advanced Air Mobilities
- Emiri Asahina1, Kenji Nakamura1, Motoki Ohta2, Mamoru Kimura2, and Shin Kusase3
- 1Tohoku University, Japan, 2Shimane University, Japan, 3MARC Institute Co., Ltd., Japan
15:10-15:30
- OS3D-4
- Design and Optimization of High Torque Permanent Magnet Vernier Machines with Fault Tolerance
- Yunjiao Li1, Jie Fu2, Xiaobei Li2, and Jing Zhao1
- 1Beijing Institute of Technology, China, 2Beijing Institute of Precision Mechatronics and Controls, China
15:30-15:50
- OS3D-5
- A Novel Efficient and High-capacity Permanent Magnet Vernier Machine for Urban Intelligent Wind Power Systems
- Yongtao Liang1, Zaixin Song1, Yidan Ma1,2, and Xiaoyu Lang1
- 1The Hong Kong Polytechnic University, China, 2Xi’an Jiaotong University, China
15:50-16:10
- OS3D-6
- High-torque Rotor Structure with Flux Collection Iron Core in Small Spoke Array Permanent Magnet Vernier Motor
- Yasuhiro Kataoka, Takeru Kobayashi, and Yoshihisa Anazawa
- Akita Prefectural University, Japan
16:10-16:30
Session OS3EPM Motor Control 3
- Time:
- 14:30-16:30
- Venue:
- Room: E
- Chair:
- Shunsuke Noguchi (Japan Aerospace Exploration Agency, Japan), Spasoje Mirić (University of Innsbruck, Austria)
- OS3E-1
- Optimized Full-speed Range Current Trajectory Control for Permanent Magnet Synchronous Motor System
- Qingguo Sun, Shenglong He, Feng Niu, Wenjing Xu, and Shanhu Li
- Hebei University of Technology, China
14:30-14:50
- OS3E-2
- Efficiency Optimization Control of Surface Permanent Magnet Synchronous Motor Based on Virtual Sinusoidal Signal Injection
- Zhiwei Chen, Shubin Jin, and Yongpeng Shen
- Zhengzhou University of Light Industry, China
14:50-15:10
- OS3E-3
- An MTPA Control Strategy for IPMSM Based on Virtual Signal Injection Considering the Inverter Nonlinearity
- Jiaxiang Li1, Yan Yan1, Chen Li1, Jian Wang1, Xuefeng Jin2, and Hao Chen1
- 1Zhejiang University, China, 2Tiangong University, China
15:10-15:30
- OS3E-4
- A Reference Flux Calculation Method Using Local Search Algorithm for Maximum Efficiency Operation in Direct Torque Controlled IPMSM Drives
- Taishin Yamashita, Atsushi Shinohara, and Kichiro Yamamoto
- Kagoshima University, Japan
15:30-15:50
- OS3E-5
- Super-twisting Algorithm Sliding Mode Observer-based Multi-vector Model-free Predictive Control Method for PMSM
- Ran Tao, Yufeng Jiang, and Wei Wang
- Southeast University, China
15:50-16:10
- OS3E-6
- A Current Observer for Interior Permanent-magnet Synchronous Motor with Single DC-Link Current Sensor
- Pengcheng Zhu, Jiming Zou, and Yongxiang Xu
- Harbin Institute of Technology, China
16:10-16:30
Session OS3FSensorless Control 2
- Time:
- 14:30-16:30
- Venue:
- Room: F
- Chair:
- Hisao Kubota (Meiji University, Japan), Gia Minh Thao Nguyen (Shimane University, Japan)
- OS3F-1
- Position Sensorless Control of CHB Converter Fed Three-phase PMSM Drives Using Collaborative High-frequency Square-wave Voltage Injection
- Minrui Gu1, Zheng Wang1, Qian Sha1, Bolun Zhang1, Haotian Chang2, and Haiyong Zhu2
- 1Southeast University, China, 2NR Electric Co., Ltd., China
14:30-14:50
- OS3F-2
- Sensorless Noise Reduction Strategy for Permanent Magnet Synchronous Motor Based on Random High-frequency Sinusoidal Injection
- Sisi Li, Binxing Li, Guoqiang Zhang, Siqi Wang, Gaolin Wang, and Dianguo Xu
- Harbin Institute of Technology, China
14:50-15:10
- OS3F-3
- Extraction of the Sampled High-frequency Current Trajectory with a Novel Synchronous Minor Sampling Process in IPMSM using PWM Carrier-synchronized Voltage Injections
- Tetsuji Daido, Muam Aaron, and Shin-ichi Hamasaki
- Nagasaki University, Japan
15:10-15:30
- OS3F-4
- Study of Direct Torque Control with Reference Flux Vector Calculation for Position Sensorless IPMSM Drives with High-frequency Signal Injection
- Atsushi Shinohara and Kichiro Yamamoto
- Kagoshima University, JAPAN
15:30-15:50
- OS3F-5
- Artificial Intelligence-based Sensorless Control of Non-sinusoidal Seven-phase PMSM
- Youxi HUANG1, Ngac ky NGUYEN1, Eric SEMAIL1, and Jinlin GONG2
- 1Univ. Lille, France, 2Shandong University, China
15:50-16:10
- OS3F-6
- A Novel Sensorless Sliding-mode Control of PMSM with VSI Nonlinearity Compensation
- Shaoshan Jin, Yongxiang Xu, Jinbao Zhang, Pan Wang, and Jibin Zou
- Harbin Institute of Technology, China
16:10-16:30
Session OS3HFault Diagnosis & Fault-tolerant Control
- Time:
- 14:30-16:30
- Venue:
- Room: H
- Chair:
- Yukinori Inoue (Osaka Metropolitan University, Japan), Xiaojun Zhang (Zhejiang University, China)
- OS3H-1
- A Diagnostic Method for Inter-turn Short Circuit Faults Based on High Frequency Park Vectors
- Xiaobao Feng1, Dewen Tian2, Bo Wang1, Rongxin Wang1, and Zihan Wei1
- 1Southeast University, China, 2China North Vehicle Research Institute, China
14:30-14:50
- OS3H-2
- Interturn Short-circuit Fault Diagnosis Method of Permanent Magnet Synchronous Motor Based on Phase Current Residuals
- Yao Rao1, Jie Fu2, Peijuan Cui2, Zaiping Zheng2, and Wei Wang1
- 1Southeast University, China, 2Beijing Institute of Precision Mechatronics and Controls, China
14:50-15:10
- OS3H-3
- Multireference-frame Based Model Predictive Fault-tolerant Control for Dual Three-phase Permanent Magnet Synchronous Machines
- Jingheng Zhu, Wenlong Li, Baojian Ji, Lei Li, and Qingle Wu
- Nanjing University of Science & Technology, China.
15:10-15:30
- OS3H-4
- Natural Fault-tolerant Control Strategy of Dual Three-phase PMSM Drives with a Common Neutral Point under Open-circuit Fault
- Kailiang Yu1, Zheng Wang2, Chenhao Zhao1, Huanzhi Wang1, Shengdao Zhu1, and Christopher H. T. Lee1
- 1Nanyang Technological University, Singapore, 2Southeast University, China
15:30-15:50
- OS3H-5
- A Fault-tolerant Control Strategy for Multiphase Motor Based on MPC Modulation
- Wangtong Liu1, Zhen Ye2, Lieyong Wang2, Zhe Chen1, and Guangzhao Luo1
- 1Northwestern Polytechnical University, China, 2Lanzhou Wanli Aviation Electromechanical Co., Ltd., China
15:50-16:10
- OS3H-6
- An Improved Fault-tolerant Control for PMSM with Current Sensor Fault
- Zhirong Zhu, Tingna Shi, Zhichen Lin, Chen Li, and Hao Chen
- Zhejiang University, China
16:10-16:30
Session OS3IPower Converter 2 (DC-AC)
- Time:
- 14:30-16:30
- Venue:
- Room: I
- Chair:
- Koji Orikawa (Hokkaido University, Japan), Xinhong Yu (Haixi Institutes Chinese Academy of Sciences, China)
- OS3I-1
- A Hybrid Modulation Strategy and Loss Modeling of Si/SiC Seven-level Converter for Aircraft Electric Propulsion
- Yiming Sun, Chengming Zhang, Zihao Zhu, Jiaxin Li, and Liyi Li
- Harbin Institute of Technology, China
14:30-14:50
- OS3I-2
- An Improved Si/SiC Hybrid Three-level ANPC Inverter with Optimized Thermal Distribution-based Modulation Scheme
- Bolun Zhang, Zheng Wang, and Minrui Gu
- Southeast University, China
14:50-15:10
- OS3I-3
- An Octal-switch Redundant Submodule for MMC to Tolerate Open-circuit Faults
- Mei-Fang Wang, Chen-Han Lin, Pei-Wen Lee, and Tzung-Lin Lee
- National Sun Yat-sen University, TAIWAN
15:10-15:30
- OS3I-4
- A Coupling-transformerless Voltage-fed Active EMI Filter for Two-stage PV Inverters
- Pawaret Ampai and Surapong Suwankawin
- Chulalongkorn University, Thailand
15:30-15:50
- OS3I-5
- Improvement and Analysis of 3-phase DCLA with Unequally Divided Source Voltage for Actual Implementation
- Tomohiko Igarashi1,2, Kohei Nomoto2, and Hirohito Funato2
- 1Polytechnic University of Japan, Japan, 2Utsunomiya University, Japan
15:50-16:10
- OS3I-6
- Loss Equalization of Unbalanced Three-phase Inverter by Pulse-voltage-injection Two-phase PWM using Variable Switching Pause Period
- Yuki Hanai1, Masataka Minami2, Shin-ichi Motegi1, and Masakazu Michihira1
- 1Kobe City College of Technology, Japan, 2Kindai University, Japan
16:10-16:30
Session OS3JControl of Power Converter
- Time:
- 14:30-16:30
- Venue:
- Room: J
- Chair:
- Ravi Nath Tripathi (Kyushu Institute of Technology, Japan), Hailiang Xu (China University of Petroleum (East China), China)
- OS3J-1
- Experimental Verification of Discontinuous Current Mode for Boost Inverters
- Makoto Ishii and Shohei Komeda
- Tokyo University of Marine Science and Technology, Japan
14:30-14:50
- OS3J-2
- High-robustness Capacitor Voltage Active Damping based on Model Free Predictive Current Control for ANPC GCI with LCL Filter
- Xiaoxue Tang1, Xinhong Yu1, Longxiang Chen1, Marcelo Lobo Heldwein2, Jose Rodriguez3, and Fengxiang Wang1
- 1Haixi Institutes Chinese Academy of Sciences, China, 2Technical University of Munich, Germany, 3Universidad San Sebastian, Chile
14:50-15:10
- OS3J-3
- A New Control Method and Power Response of Power Compensator with Low Switching Frequency
- Joungjin Seo and Hanju Cha
- Chungnam National University, Republic of Korea
15:10-15:30
- OS3J-4
- Evaluation of Automatic Adjustment Methods for Voltage Reference to Compensate Dead-time Distortion using Machine Learning
- Hideki Ayano1, Makoto Ohmi1, Yuto Omae2, and Yoshihiro Matsui3
- 1National Institute of Technology, Japan, 2Nihon University, Japan, 3Fukuoka Institute of Technology, Japan
15:30-15:50
- OS3J-5
- A Survey of Lifetime Extension Techniques for High-reliability Power Electronics
- Min Zhang1, Yongxing Yang1, Yukai Wen1, Wei Jiang1, Dan Zhao2, and Ke Shen1
- 1Northwestern Polytechnical University, China, 2Xi'an University of Technology, China
15:50-16:10
- OS3J-6
- Fault Diagnosis Method of Servo Motor Bearing Installation Misalignment Based on CSFF-CNN
- Jing Wang1, Jianye Li1, Ming Yang1, and Xinmei Zhang2
- 1Harbin Institute of Technology, China, 2Ningbo Anson CNC Technology Co., Ltd, China.
16:10-16:30
Session OS3KPower Converters of Renewable Energy Systems 2
- Time:
- 14:30-16:30
- Venue:
- Room: K
- Chair:
- Takaharu Takeshita (Nagoya Institute of Technology, Japan), Wanning Zheng (Wuhan University of Science and Technology, China)
- OS3K-1
- Low Frequency AC Transmission for Offshore Wind Power
- Yi LU1, An Wei CHEN1, Guo Liang ZHAO2, Xiu Li WANG3, Nian Wen XIANG4, and Jian Gang BI5
- 1Country State Grid Zhejiang Electric Power Co., Ltd., China, 2Global Energy Interconnection Research Institute Co., Ltd., China, 3Xi’an Jiaotong University, China, 4Hefei University of Technology, China, 5China Electric Power Research Institute Co., Ltd., China
14:30-14:50
- OS3K-2
- Improved Damping Control Based on Hamiltonian Control Law for Low-carbon Hydrogen Production Systems
- Burin Yodwong1, Pongsiri Mungporn1, Yaowaret Maiket1, Damien Guilbert2, Matheepot Phattanasak1, Uthen Kamnarn3, Melika Hinaje4, Gianpaolo Vitale5, and Phatiphat Thounthong1
- 1King Mongkut’s University of Technology North Bangkok, Thailand, 2Université Le Havre Normandie, France, 3Rajamangala University of Technology Lanna, Thailand, 4Université de Lorraine, France, 5Italian National Research Council, Italy
14:50-15:10
- OS3K-3
- Sensorless Control Strategy of Remote Area Autonomous PMSG-based Microgrids for Improving Redundancy
- Xi Luo1, Xinghao Wang1, Dehui Luo1, Huayu Ji1, Jiani Luo1, Xijian Lin1, and Dianxun Xiao1,2
- 1The Hong Kong University of Science and Technology (Guangzhou), China, 2HKUST Shenzhen–Hong Kong Collaborative Innovation Research Institute, China
15:10-15:30
- OS3K-4
- Autonomous Passivity Model Predictive Control for Fixed-time Feedforward Decoupling of DC Microgrids with Constant Power Loads
- Zehua Zhang, Panbao Wang, Dongxin Guo, Sibao Ding, Wei Wang, and Dianguo Xu
- Harbin Institute of Technology, China
15:30-15:50
- OS3K-5
- Impact Analysis of the Distribution and Installation Proportions of Grid-forming and Grid-following Converters on the Stability of a 100% Renewable Energy System
- Lixing Tian1, Shiwei Chen1, Wanning Zheng1, Dan Liu2, Chang Ye2, and Kezheng Jiang2
- 1Wuhan University of Science and Technology, China, 2State Grid Hubei Electric Power Research Institute, China
15:50-16:10
- OS3K-6
- Power Control Using Sub-Battery for Electric Motorcycle
- Momoe Sakai and Takaharu Takeshita
- Nagoya Institute of Technology, Japan
16:10-16:30
Session OS3LAI Application for Electric Machine and Drive
- Time:
- 14:30-16:30
- Venue:
- Room: L
- Chair:
- Nobukazu Hoshi (Tokyo University of Science, Japan), Ying Liu (Harbin Institute of Technology, China)
- OS3L-1
- An Online Auto-tuning Method for PID Controllers Based on Back Propagation Neural Network
- Liwen Bao, Fei Peng, Yunkai Huang, and Yunlu Du
- Southeast University, China
14:30-14:50
- OS3L-2
- Evaluation of Feasibility for Optimal Motor Design using Deep Q-network
- Ji-Hoon Han, Eui-Jin Choi, Jong-Hoon Park, and Sun-Ki Hong
- Hoseo University, Republic of Korea
14:50-15:10
- OS3L-3
- A Study of Motor Fault Condition Classification Using an Unsupervised Learning-based Ensemble Model
- Eui-Jin Choi, Seung-Min Song, Ji-Hoon Han, and Sun-Ki Hong
- Hoseo University, Republic of Korea
15:10-15:30
- OS3L-4
- Comparison of Recurrent Neural Networks on Dry-type Transformer Thermal Models under Various Conditions
- Junlaphat Jarasureechai, Chanantorn Sophon, Chankit Promrat, Ekkachai Mujjalinvimut, Piyasawat Navaratana Na Ayudhya, Tirasak Sapaklom, Jakkrit Kunthong, and Atip Doolgindachbaporn
- King Mongkut’s University of Technology Thonburi, Thailand
15:30-15:50
- OS3L-5
- Gear Fault Diagnosis in Geared Motors based on Frequency Adaptation Graph Prototype Network with Limited Data
- Yidan Ma1,2, Zaixin Song1, Yongtao Liang1, and Jianfu Cao2
- 1The Hong Kong Polytechnic University, China, 2Xi’an Jiaotong University, China
15:50-16:10
- OS3L-6
- Heuristic Investigation of the Required Amount of Data as Part of the Scalable Data-based Diagnostic Concept
- Andreas Schmitz1,2, Felix Heimann2, Marco Decker2, Clemens Gühmann1, and Roland Serway2
- 1Technische Universität, Germany, 2IAV GmbH, Germany
16:10-16:30
November 29 (Fri.), 2024
Session OS4BLinear Drives and Magnetic Levitations 2
- Time:
- 9:30-11:50
- Venue:
- Room: B
- Chair:
- Shunsuke Ohashi (Kansai University, Japan), Victor Tedesco (The Texas Heart Institute, USA)
- OS4B-1
- Evaluation of Support Stiffness of a Permanent Magnet Attractive Force Type Passive Magnetic Bearing
- Yanbo Dong, Satoshi Ueno, and Chengyan Zhao
- Ritsumeikan University, Japan
9:30-9:50
- OS4B-2
- Multi-objective Parameter Optimization Design of Radial Magnetic Levitation Bearing
- Yanbo Wang1, Jiwei Cao1, Bin Chen2, Xi Chen3, Jiaxi Liu1, and Liyi Li1
- 1Harbin Institute of Technology, China, 2Guangdong Provincial Key Laboratory of High-Performance Servo System, China, 3Shanghai Academy of Spaceflight Technology, China
9:50-10:10
- OS4B-3
- A Mixed Sensitivity H∞ Control Method Based on Active Magnetic Bearing
- Sen Yan1, Xi Chen2, Jiaxi Liu1, Jiwei Cao1, and Liyi Li1
- 1Harbin Institute of Technology, China, 2Shanghai Academy of Spaceflight Technology, China
10:10-10:30
- OS4B-4
- Topology Optimization of an Alternate Permanent Magnet Electrodynamic Suspension Using a 3-d Hybrid Analytical Model
- Louis Beauloye and Bruno Dehez
- UCLouvain, Belgium
10:30-10:50
- OS4B-5
- Thrust Analysis of a Reluctance-based Magnetic Lead Screw with Flux-concentrating Structure
- Hayate Ayuzawa1, Akira Heya1, Yoshihiro Nakata2, Hisaaki Mamiya3, and Tsuyoshi Inoue1
- 1Nagoya University, Japan, 2The University of Electro-Communications, Japan, 3Nabeya Bi-tech Kaisha, Japan
10:50-11:10
- OS4B-6
- Basic Consideration of Topology Optimization for Eddy Current Dampers
- Kodai Watanabe1, Akira Heya1, Shinsaku Nakamura2, and Tsuyoshi Inoue1
- 1Nagoya University, Japan, 2Ebara Corporation, Japan
11:10-11:30
- OS4B-7
- Proposal for Estimation of Modal Damping Ratio in Electromagnetic Bone Conduction Devices
- Takaya Furui, Wataru Kitagawa, Takaharu Takeshita, Akehiro Masuda, Ryohei Masuda, and Masahiro Nakashima
- 1Nagoya Institute of Technology, Japan, 2SANKO MOLD Co., Ltd., Japan
11:30-11:50
Session OS4CPermanent Magnet Machines 3
- Time:
- 9:30-11:50
- Venue:
- Room: C
- Chair:
- Yukihiro Yoshida (Akita University, Japan), Guoyu Chu (UNSW Sydney, Australia)
- OS4C-1
- Structural Study of IPMSMs Achieving Both High Torque and Wide Constant Power Operating Range
- Yosuke Hakamata1, Masayuki Sanada1, Shigeo Morimoto1, Yukinori Inoue1, Ikuto Homma2, Yusuke Muto2, Shuhei Tamamura3, and Masashi Sonoda3
- 1Osaka Metropolitan University, Japan, 2Sanden Corporation, Japan, 3WOLONG Motor Control Technology Co., Ltd., Japan
9:30-9:50
- OS4C-2
- Research on the Optimization of Power Density and Its Influencing Factors of the YASA Motor
- Jiaxin Li, Chengming Zhang, Liyi Li, Yiming Sun, and Jiangwen Liu
- Harbin Institute of Technology, China
9:50-10:10
- OS4C-3
- AC Copper Loss Separation and Reduction in IPMSM using Finite Element Analysis
- Kenya Naruse1,2, Masahiro Kayano1, Hironari Mitarai1, Kazuki Tamura2, and Kenji Nakamura2
- 1AICHI STEEL Corporation, Japan, 2Tohoku University, Japan
10:10-10:30
- OS4C-4
- Design and Analysis of Permanent Magnet Synchronous Machine with High Power Density for Aircraft Starter-generator
- Zhen Zhang, Qunjian Lou, Peidong Hu, Jian Wang, and Yan Yan
- Zhejiang University, China
10:30-10:50
- OS4C-5
- Characterization of a High Torque Density Halbach Motor in UAV Application
- Chao Zhi1,2, Yangyang Huang1, Haotian Wu1,2, Qian Zhao1, Lijun Xu1, and Yinian Mao1,2
- 1Meituan Technology, China, 2Meituan Academy of Robotics Shenzhen, China
10:50-11:10
- OS4C-6
- Design and Analysis of In-wheel Flux Reversal Motor for Compact EV
- Shotaro Tsunoda and Kenji Nakamura
- Tohoku University, Japan
11:10-11:30
- OS4C-7
- Multi-objective Robust Optimization of a Low-cost and Efficient IPMSM for Battery Electric Vehicle
- Andrew Botham1, Bipana KC1, M. Hossain Mohammadi2, Reza Nasirizarandi2, and Narayan C. Kar1
- 1University of Windsor, Canada, 2R&D Americas, Canada
11:30-11:50
Session OS4DLoss, Thermal and Cooling of Electric Machines
- Time:
- 9:30-11:50
- Venue:
- Room: D
- Chair:
- Yanhui Gao (Oita University, Japan)
- OS4D-1
- Research on Immersion Evaporative Cooling under Different Pressure Conditions in High Power Density Motor
- Yuqing Liu1, Jiwei Cao1, Bin Chen2, Jiaxi Liu1, Yuchen Song1, and Liyi li1
- 1Harbin Institute of Technology, China, 2Guangdong Provincial Key Laboratory of High-Performance Servo System, China
9:30-9:50
- OS4D-2
- A Baseline Thermal Model for Liquid-cooled Multi-megawatt Scale Direct-drive Permanent Magnet Wind Turbine Generators
- Fergus Hall and Alasdair McDonald
- The University of Edinburgh, Scotland
9:50-10:10
- OS4D-3
- Computationally Efficient Estimation of Thermally Induced Stresses in Motorette Using Numerical Homogenization Techniques and Experimental Validation
- Faezeh Hosseini1,2, Guillaume Crevecoeur1,2, and Hendrik Vansompel1,2
- 1Ghent University, Belgium, 2MIRO Corelab, Belgium
10:10-10:30
- OS4D-4
- Experimental Investigation of Windage Loss Impacts on Electrical Machine with Oil Jet Cooling
- Sen Zhang1,2, Zeyuan Xu1, Fengyu Zhang1, Chuan Liu1, Yuling He3, He Zhang4, Chris Gerada1, and David Gerada1
- 1University of Nottingham, U.K., 2University of Nottingham Ningbo, China, 3North China Electric Power University, China, 4Yongjiang Laboratory, China
10:30-10:50
- OS4D-5
- Loss Evaluation in a Ductile Cast Iron Frame of a Permanent Magnet Synchronous Motor
- Shunpei Goto1, Yasuhito Takahashi1, Koji Fujiwara1, Makoto Matsushita2, and Katsutoku Takeuchi2
- 1Doshisha University, Japan, 2Toshiba Infrastructure Systems & Solutions Corporation, Japan
10:50-11:10
- OS4D-6
- Evaluation of Inverter Topologies and Switching Frequencies Regarding Harmonic Losses in PMSM
- Eike Christian Krüger1,2, Janine Ebersberger1,2, Axel Mertens1,2, and Bernd Ponick1,2
- 1Technische Universität Braunschweig, Germany, 2Leibniz University Hannover, Germany
11:10-11:30
- OS4D-7
- Measurement of Magnetic Parameters with Focus on Eddy Current Losses in Permanent Magnets of Electrical Machines using Flexible Matrix Sensors
- Nijan Yogal1, Christian Lehrmann1, and Markus Henke2
- 1Physikalisch-Technische Bundesanstalt, Germany, 2Technische Universität Braunschweig, Germany
11:30-11:50
Session OS4ESuperconducting & Special Machines
- Time:
- 9:30-11:50
- Venue:
- Room: E
- Chair:
- Yusuke Fujii (Tokyo Institute of Technology, Japan), Chao Zhi (Meituan Corporation, China)
- OS4E-1
- Superconductive GdBaCuO 3-phase High Speed Outrunner Motor for High Load Cargo Drones
- Andreas Greifelt1, Moritz Berrenberg2, and Niels Peder Harkes2
- 1MAXMORE Germany GmbH, Germany, 2MAXMORE Technology Ltd., China
9:30-9:50
- OS4E-2
- Study on AC Loss Reduction in HTS Motors for Electrified Aircraft Propulsion
- Enze Ma, Yulong Li, Yuan Gao, Huaqi Lian, and Heng Yu
- Beihang University, China
9:50-10:10
- OS4E-3
- Analysis on the Characteristics of the Decompression Cooling System Used in the Superconducting Motor
- Yuan Gao, Yulong Li, Enze Ma, Huaqi Lian, Zuoxia Wang, and Caiyu Yang
- Beihang University, China
10:10-10:30
- OS4E-4
- Dynamic Non-linear Numerical-analytical Model for Synchronous Homopolar Machines
- Amedeo Vannini1, Mauro Di Nardo2, Alessandro Marfoli1, Antonino La Rocca1, and Chris Gerada1
- 1University of Nottingham, UK, 2Politecnico di Bari, Italy
10:30-10:50
- OS4E-5
- Design and Evaluation of a Flat PCB-based Axial Flux Motor
- Haotian Wu1,2, Chao Zhi1,2, Han Gao1, Lijun Xu1, and Yinian Mao1
- 1Meituan Technology, China, 2Meituan Academy of Robotics Shenzhen, China
10:50-11:10
- OS4E-6
- A Double-feed Magnetic Resonant Coupling Machine with Air-gap Windings for High Power Density and Efficiency
- Kazuto Sakai, Takaaki Toda, and Ryo Shimizu
- Toyo University, Japan
11:10-11:30
- OS4E-7
- Transmission Torque Characteristics of Strain Wave Gear with 16-poles Magnet
- Fumiya Kitayama and Ryou Kondo
- Ibaraki University, Japan
11:30-11:50
Session OS4FSynchronous Machine Control and Drives 2
- Time:
- 9:30-11:50
- Venue:
- Room: F
- Chair:
- Yoshitaka Iwaji (Ibaraki University, Japan), Shuo Wang (University of Nottingham Ningbo, China)
- OS4F-1
- Online MTPA Angle Search Method Using Flux Linkage Plane Estimation of SynRM
- Souya Arakawa, Shigeo Morimoto, Yukinori Inoue, and Masayuki Sanada
- Osaka Metropolitan University, Japan
9:30-9:50
- OS4F-2
- Position Estimation and Parameter Identification of SynRM at Standstill
- Masahiro Oyanagi, Shigeo Morimoto, Yukinori Inoue, and Masayuki Sanada
- Osaka Metropolitan University, Japan
9:50-10:10
- OS4F-3
- Maximum Torque Per Ampere Control Implemented Hardware System for Synchronous Reluctance Motor
- Yu Nabeshima and Tsuyoshi Hanamoto
- Kyushu Institute of Technology, Japan
10:10-10:30
- OS4F-4
- Voltage Angle Regulated Field Weakening Control Based on Overmodulation Strategy for PMa-SynRM Drives
- Runze Jing1, Dawei Ding1, Qiwei Wang1, Zhaoqiang Fu2, Wenlong Liu2, Li Ding1, Gaolin Wang1, and Dianguo Xu1
- 1Harbin Institute of Technology, China, 2Guangdong Midea Air-Conditioning Equipment Co., Ltd., China
10:30-10:50
- OS4F-5
- Dual Inverter Controlled Third Harmonic Current Injection Scheme for an Open-end Winding Brushless Wound Rotor Synchronous Machine
- Ghulam Jawad Sirewal, Eungjae Kim, and Gilsu Choi
- Inha University, Republic of Korea
10:50-11:10
- OS4F-6
- Acoustic Noise Reduction in Resolver-based PMSM Servo Drives using NLMS Adaptive Filtering
- Tao Li, Chaohui Liang, and Duhuang Su
- Spintrol Technology (Shenzhen) Co., Ltd., China
11:10-11:30
- OS4F-7
- Applying Partial PAM Method Suitable for Robot Motor Drive
- Hideki Jonokuchi1, Yoshihiro Okumatsu2, and Yoh Sato2
- 1Nagoya Institute of Technology, Japan, 2TOYOTA MOTOR CORPORATION, Japan
11:30-11:50
Session OS4GPM Motor Control 4
- Time:
- 9:30-11:50
- Venue:
- Room: G
- Chair:
- Sari Maekawa (Meiji University, Japan), Binxing Li (Harbin Institute of Technology, China)
- OS4G-1
- Implementation and Validation of a LUT-based Model of an IPMSM Considering Saturation and Spatial Harmonics
- Daniel. C. Rodriguez Pinto, Achref Douiri, and Rik W. de Doncker
- Institute for Power Electronics and Electrical Drives, Germany
9:30-9:50
- OS4G-2
- Impact of Voltage Modulation Module on Negative Input Impedance and DC-link Stability in Permanent Magnet Synchronous Motor Drives
- Zhen Jin1, Wei Xu1, Jiyao Wang1, Shuhua Fang1, and Xiping Liu2
- 1Southeast University, China, 2Jiangxi University of Science and Technology, China
9:50-10:10
- OS4G-3
- Influence of d-axis Current on Torque and Transformer Secondary-side Power in Power Superposition System for Position Sensor of Surface-mounted PMSM
- Haruki Sazanami1, Takeshi Kiribuchi2, Yukinori Inoue1, Shigeo Morimoto1, and Masayuki Sanada1
- 1Osaka Metropolitan University, Japan, 2OMRON, Japan
10:10-10:30
- OS4G-4
- Improvement Performance of FOC for PMSM Based on Reinforcement Learning TD3 Agent Current Controller
- Kittithuch Paponpen and Tanpisit Atipasaworn
- Silpakorn University, Thailand
10:30-10:50
- OS4G-5
- Torque Control Characteristics of Simple Controller-based Direct Torque Control for PMSM Drive System
- Hiroshi Enokura1, Yukinori Inoue2, Shigeo Morimoto2, Masayuki Sanada2, Toshimitsu Aizawa3, Takashi Takagi3, and Taichi Kawakami1
- 1Osaka Metropolitan University College of Technology, Japan, 2Osaka Metropolitan University, Japan, 3Toshiba Corporation, Japan
10:50-11:10
- OS4G-6
- Modulation Signal Optimized Synchronous PWM
- Tetsuya Kojima, Tomoya Tachibana, Shota Kondo, Junji Kitao, and Tomohira Takahashi
- Mitsubishi Electric Corporation, Japan
11:10-11:30
- OS4G-7
- An Accurate Measurement Method for Iron Loss Resistance of Permanent Magnet Synchronous Motor
- Yongpeng Shen, Yakai Ge, Zhiwei Chen, and Bo Zhou
- Zhengzhou University of Light Industry, China
11:30-11:50
Session OS4HSensorless Control 3
- Time:
- 9:30-11:50
- Venue:
- Room: H
- Chair:
- Yoshiyasu Takase (YASKAWA Electric Corporation, Japan), Adrish Bhaumik (National University of Singapore, Singapore)
- OS4H-1
- Torque Ripple Suppression Control in Medium to High-speed Ranges with Position Sensorless Vector Control
- Taiki Mikami, Keitaro Kawarazaki, and Nobukazu Hoshi
- Tokyo University of Science, Japan
9:30-9:50
- OS4H-2
- A Mutual Inductance Estimation Based Sensorless Control for IPMSM with Complex-coefficient Filter in Low-speed Range
- Yuhan Chen1, John Xu1, Jing Li1, Dunant Halim1, and Huanran Wang2
- 1University of Nottingham Ningbo, China, 2Zhejiang University, China
9:50-10:10
- OS4H-3
- Robust Deadbeat Predictive Current Control for High-speed Synchronous Machine Sensorless Drive with Instant Inductance Identification
- Yinfeng Hu1, Wei Hua1, and Mingjin Hu2
- 1Southeast University, China, 2The Hong Kong Polytechnic University, China
10:10-10:30
- OS4H-4
- Sensorless Control for IPM with Adaptive Resistance Estimation Using Flux Norm Correction
- Zeqiang He and Tadahiko Shinshi
- Tokyo Institute of Technology, Japan
10:30-10:50
- OS4H-5
- Suppression of Velocity Pulsations with Resonant Controllers in Sensorless Vector Control of Permanent Magnet Synchronous Motors
- Naohiko Sekine and Hisao Kubota
- Meiji University, Japan
10:50-11:10
- OS4H-6
- Efficient I-F Startup Method for Refrigeration Compressors
- Morten Milton Bleshøy1, Kaiyuan Lu1, Kresten Kjær Sørensen2, John-Josef Leth1, and Jan Dimon Bendtsen1
- 1Aalborg University, Denmark, 2Bitzer Electronics, Denmark
11:10-11:30
- OS4H-7
- Vibration Suppression Method using Disturbance Observer in Sensorless 120-degree Conduction Compressor Motor Drive
- Yusuke Omi, Takumi Yasuda, Hiroki Watanabe, and Jun-ichi Itoh
- Nagaoka University of Technology, Japan
11:30-11:50
Session OS4ILinear Motor Control and Drives
- Time:
- 9:30-11:50
- Venue:
- Room: I
- Chair:
- Takayuki Miyajima (Daikin Industries, Ltd., Japan), Ruiwu Cao (Nanjing University of Aeronautics and Astronautics, China)
- OS4I-1
- Design for Bidirectional Movement of Bendable Tubular Linear Motor
- Kaito Yamamoto and Seiichiro Katsura
- Keio University, Japan
9:30-9:50
- OS4I-2
- Research on the Influence Mechanism and Stability Control Method of Composite Disturbance on Double-end Power Supply of High Speed Maglev Traction System
- Bo Zhang1,2,3, Zhanming Zhang2,3, Qiongxuan Ge2,3, Weixin Chen2,3, Ke Wang2,3, and Yaohua Li2,3
- 1National Railway Administration of P. R.C, China, 2Chinese Academy of Sciences, China, 3Shijingshan District, China
9:50-10:10
- OS4I-3
- A Novel Segment Switching Method for Dual Three-phase Linear Motors with Stator Segmented Powered
- Yanfei Li1,2, Zixin Li1,2, Cong Zhao1, Fei Xu1,2, Liming Shi1,2, and Yaohua Li1,2
- 1Chinese Academy of Sciences, China, 2University of Chinese Academy of Sciences, China
10:10-10:30
- OS4I-4
- A Smooth Power Supply Switching Method of Segmented Long Primary Linear Motors for High-speed Applications
- Cong Zhao1,2, Zixin Li1,2, Farui Zhang3, Fanqiang Gao1,2, Fei Xu1,2, and Hang Zhang1
- 1Chinese Academy of Sciences, China, 2University of Chinese Academy of Sciences, China, 3Institute of Electrical Engineering and Advanced Electromagnetic Drive Technology Qilu Zhongke, China
10:30-10:50
- OS4I-5
- Full-decoupled Two-degree-of-freedom Position Controller for PMSLM Based on ADRC
- Yiwei Zhang, Xuzhen Huang, and Jian Xu
- Nanjing University of Aeronautics and Astronautics, China
10:50-11:10
- OS4I-6
- Friction Compensation Method with Iterative Learning Based Bang-bang Compensator in PMLSM System
- Kai Kang, Mingyi Wang, Jianxin Cui, Chengming Zhang, and Liyi Li
- Harbin Institute of Technology, China
11:10-11:30
- OS4I-7
- Adaptive Feedforward Control Based on Recursive Least Squares Algorithm for the Biaxial Maglev Planar-motor-driven Gantry System
- Minghong Liu, Mingyi Wang, Junchi Li, Qinwei Sun, Chengming Zhang, and Liyi Li
- Harbin Institute of Technology, China
11:30-11:50
Session OS4JPower Converter 3 (WPT)
- Time:
- 9:30-11:50
- Venue:
- Room: J
- Chair:
- Hirohito Funato (Utsunomiya University, Japan)
- OS4J-1
- High Distance to Diameter Ratio Wireless Power Transfer System
- Jiantao Zhang1, Zhan Gao1, Jianyu Lan2, Dean Wang1, Ying Liu1, Fuze Chen1, Wenbo Zhao1, and Chunbo Zhu1
- 1Harbin Institute of Technology, China, 2Shanghai Institute of Space Power-Sources, China
9:30-9:50
- OS4J-2
- Analysis of Low-eddy Current WPT Applied in Underground Coal Mines
- Yingying Wang, Jiahui Yu, and Shuangli Chen
- China University of Mining and Technology, China
9:50-10:10
- OS4J-3
- A Novel Capacitive Power Transfer System with Embedded Coupler for Rotary Application
- Ying Liu, Liangyi Pan, Shunyu Yao, Jiantao Zhang, and Chunbo Zhu
- Harbin Institute of Technology, China
10:10-10:30
- OS4J-4
- Characteristic Analysis of Coupling Mechanism for Wireless Power Transfer System with Transparent Window Used in Coal Mine
- Yingying Wang, Shuangli Chen, Jiahui Yu, and Zuhuo Liang
- China University of Mining and Technology-Beijing, China
10:30-10:50
- OS4J-5
- WPT Coil Position for Minimizing SOC Fluctuations in Battery-powered Trains
- Eita Sato and Keiichiro Kondo
- Waseda University, Japan
10:50-11:10
- OS4J-6
- Coupling Coefficient Estimation Method for SP-type Wireless Power Transfer System
- Hiroki Sugihara, Yuki Shimizu, and Yoshitaka Kawabata
- Ritsumeikan University, Japan
11:10-11:30
- OS4J-7
- Hybrid Closed-form Modulation Scheme for Three-phase Dual-active Bridge with Reduced RMS Current
- Lukas Leucker, Daniel von den Hoff, and Rik W. De Doncker
- RWTH Aachen University, Germany
11:30-11:50
Session OS4KPower Converter (General)
- Time:
- 9:30-11:50
- Venue:
- Room: K
- Chair:
- Shotaro Takahashi (Akita University, Japan), Yi Lu (State Grid Zhejiang Electric Power Research Institute, China)
- OS4K-1
- Simulation Platform for GaN-based Three-phase Voltage Source Inverter Analysis: Switching Frequency and Deadtime
- Vijay Kumar Singh1, Ravi Nath Tripathi2, and Manoj Badoni3
- 1Rajiv Gandhi Institute of Petroleum Technology Jais, India, 2Kyushu Institute of Technology, Japan, 3Thapar Institute of Engineering and Technology, India
9:30-9:50
- OS4K-2
- Application of Mn-Zn Ferrite to Passive Common-noise Canceller Placed on Inverter DC Side
- Jinxing Zhou and Koji Orikawa
- Hokkaido University, Japan
9:50-10:10
- OS4K-3
- Passive Cancellation for Reducing Input- and Output-side Common-mode Currents in Three-phase PWM Inverter-fed Motor Drive Systems
- Shotaro Takahashi, Matoi Ono, and Ryosuke Kanbayashi
- Akita University, Japan
10:10-10:30
- OS4K-4
- Efficient and Compact 400-v, 100-a Solid-state Circuit Breaker Using SiC Devices
- Taro Takamori1,2, Taiki Hirai2, and Keiji Wada2
- 1The University of Tokyo, Japan, 2Tokyo Metropolitan University, Japan
10:30-10:50
- OS4K-5
- An Energy-saving Strategy for Permanent Magnet Synchronous Motors System
- Hao Yang, Zhichao Huang, Song Qiu, and Qingxiang Liu
- Southwest Jiaotong University, China
10:50-11:10
- OS4K-6
- Improved Sliding Mode Control Method Using a Hyperbolic Function for Battery Charger of PMDs
- Junhyeok Choi and Yeongsu Bak
- Keimyung University, Republic of Korea
11:10-11:30
- OS4K-7
- Parallel Grid-forming Inverters for 100% Inverter-based Resources RE100 Microgrid -Emphasis on Secondary Control-
- Phimnaphat Phonthani, Preenapan Panya, and Surapong Suwankawin
- Chulalongkorn University, Thailand
11:30-11:50
Session OS4LPower Converter 3 (AC-DC)
- Time:
- 9:30-11:50
- Venue:
- Room: L
- Chair:
- Hiroaki Yamada (Yamaguchi University, Japan), Xinhong Yu (Haixi Institutes Chinese Academy of Sciences, China)
- OS4L-1
- An Improved Super-twisting Sliding Mode Controller over Totem-pole Power Factor Corrector
- Yihe SHEN, Siwen YE, Mingou WEI, Zhibin LING, and YANG Xi-jun
- Ministry of Education (Shanghai Jiao Tong University), China
9:30-9:50
- OS4L-2
- Low Harmonic 24-pulse Rectifier Based on Square-wave Voltage Injection
- Bin wang, Manlei huang, Jingfang wang, Chen nie, and Changbao wang
- Harbin Engineering University, China
9:50-10:10
- OS4L-3
- A Synchronous Rectification Strategy Driven by Current and Digital for Three Phase LLC Resonant Converter
- Xinghong Luo1, Xuliang Yao1, Yannan Gao2, and Jingfang Wang1
- 1Harbin Engineering University, China, 2Guangdong Ocean University, China
10:10-10:30
- OS4L-4
- Simplified Linear Kalman Filter for Sensorless Oriented Control of PWM Rectifiers
- F. Centi, A. Credo, G. Fabri, A. Fioravanti, and M. Tursini
- University of L’Aquila, Italy
10:30-10:50
- OS4L-5
- Fault-tolerant Strategy of Flying-capacitor Boost Three Level Converter
- Da Zhang1, YuGu1, Donglai Zhang1, Hao Yang1, Tangpei Jiao2, and Hui Li2
- 1Harbin Institute of Technology (Shenzhen), China, 2Space Microwave Technology Institute (Xi’an), China
10:50-11:10
- OS4L-6
- Evaluation of the Impact of Power Quality on Each Home Appliance
- Tomoaki Shoji and Masahiko Hasegawa
- Tokyo Electric Power Company Holdings, Inc., Japan
11:10-11:30
- OS4L-7
- Power Balancing Control of Sub Modules with Battery Units in Single-phase Grid-tied MMC Under Unbalanced Generated Power
- Ryo Yoshimura and Hiroaki Yamada
- Yamaguchi University, Japan
11:30-11:50
Session PS4-1Numerical Analysis and Modeling 2
- Time:
- 12:00-13:00
- Venue:
- FIT Arena
- PS4-1-1
- Fast Steady-state Analysis Method for Cage Induction Motors Based on Polyphase TP-EEC Method in a Rotational Reference Frame
- Hiroyuki Kaimori1, Yasuhito Takahashi2, and Shinji Wakao3
- 1Science Solutions International Laboratory, Inc., Japan, 2Doshisha University, Japan, 3Waseda University, Japan
- PS4-1-2
- Analysis of Electromagnetic Force and Power Consumption in Magnetic Levitation Planar Motor with Dual-layer Coil Array
- Kai Liu, Fuxiang Chen, Yingtong Wu, Aoqi Hu, Xinpeng Wei, and Lizhan Zeng
- Huazhong University of Science and Technology, China
- PS4-1-3
- Dynamic Behavior of Levitated Flexible Steel Plate in Bending Electromagnetic Levitation System during Disturbance Input
- Yamato Uchida1, Kazuki Ogawa2, Ikkei Kobayashi1, Jumpei Kuroda1, Daigo Uchino3, Keigo Ikeda4, Taro Kato5, Ayato Endo6, Takayoshi Narita1, and Hideaki Kato1
- 1Tokai University, Japan, 2Aichi University of Technology, Japan, 3Numazu National College of Technology, Japan, 4Hokkaido University of Science, Japan, 5Tokyo University of Technology, Japan, 6Fukuoka Institute of Technology, Japan
- PS4-1-4
- Magnetic Properties of Iron Core Materials Based on the Creep Model and Dynamic Observation of Magnetic Domains
- Shiyu Wang, Zhen Wang, Yanli Zhang, and Xiuke Yan
- Shenyang University of Technology, China
- PS4-1-5
- Improvement of a Magnetostrictive Model Considering Applied Stress and Magnetic Fields Including Hysteresis Effects
- Ming Cai, Yanli Zhang, Zhen Wang, and Xiuke Yan
- Shenyang University of Technology, China
- PS4-1-6
- A Novel Electromagnetic Analysis Method of Spoke-type Permanent Magnet Machine with Overhang Structure
- Yunlu Du1,2, Yunkai Huang1, Fei Peng1, Baocheng Guo3, Liwen Bao1, and Hajime Igarashi2
- 1Southeast University, China, 2Hokkaido University, Japan, 3Nanjing Normal University, China
- PS4-1-7
- Simulation Analysis of Air Cooling System Flow Field Characteristics for Generator-motor in Pumped Storage Power Stations
- Zhao Yifeng1, Zhao Sheng2, Lu Weifu1, Gui Zhonghua1, Zhang Fei1, and Chen Jinxiu2
- 1Pumped-storage Research Institute, China, 2Institute of Electrical Engineering CAS, China
- PS4-1-8
- Electromagnetic-structural Coupled Analysis of Magnetic-elastic Power Generation System with High Load and Small Deformation Characteristics
- Yun-Jung Hwang, Jong-Oh Park, Seung-Eun Rho, Eun-Chae Jung, Kyung-Sik Seo, and Il-Han Park
- Sungkyunkwan University, Republic of Korea
- PS4-1-9
- Frequency Response Analysis for Transformer Winding with Improved Equivalent Circuit
- Rongjie Wei1, Xiuke Yan1, Yanbing Li2, Yanli Zhang1, and Zhen Wang1
- 1Shenyang University of Technology, China, 2Pera Corporation Ltd, China
Session PS4-2Noise, Vibration and Reliability of Electric Machines 2
- Time:
- 12:00-13:00
- Venue:
- FIT Arena
- PS4-2-1
- Probabilistic Analysis of Partial Discharges in the Stator Winding Insulation for Electrified Aviation
- Norman Blanken, Labassi Younes Laajouzi, and Bernd Ponick
- Leibniz University Hannover, Germany
- PS4-2-2
- Fast and Accurate Radial-flux PMSM Step-skewing Computation Methodology for NVH Improvements Across the Machine Full Operation Range
- Sebastian Ciceo1, Raluca Raia2, Flavius Paduraru2, and Kohta Sugiura3
- 1Siemens Digital Industry Software, Belgium, 2Siemens Digital Industry Software, Romania, 3Siemens Digital Industry Software, Japan
- PS4-2-3
- Investigation of Measurement Method for Thickness of Hot Springs Scale Using Electromagnetic Force Vibration
- Hiroyuki Ikusada1, Ryota Takasugi1, Shinya Shiota1, Yuji Gotoh1, and Teruyoshi Sasayama2
- 1Oita University, Japan, 2Kyusyu University, Japan
- PS4-2-4
- A Negative Stiffness Injection Method for PMSM in the Five-DoF Magnetic Levitation System to Suppress the Vibration
- Qiang Yu, Xin Cao, and Zhiquan Deng
- Nanjing University of Aeronautics and Astronautics, China
- PS4-2-5
- Novel Online Non-invasive Measurement Approach for PMSM-transmission Chain Radial Natural Frequency Based on Driving PMSM Radial Force Injection
- Juntao Wang, Zhiyuan Wang, and Pinjia Zhang
- Tsinghua University, China
- PS4-2-6
- A Novel Partial Slot Unwounded Method for Electromagnetic Vibration Reduction of Large Electric Machines
- Xiaolong Zhao1, Jianjun Liu2, Longhui Liu1, Yong Yang2, Jian Xiao2, Wanhai Zhao3, Haoyu Kang1, Lu Sun1, Jin Wang1, and Libing Zhou1
- 1Huazhong University of Science and Technology, China, 2Dongfang Electric Machinery Co., Ltd., China, 3Nanyang Power Supply Company, China
- PS4-2-7
- A Motor Vibration Suppression Method Based on Vibration Reduction Coils
- Yanshuo Jia, Yuanzhi Zhang, Yihang Luan, and Jianjun Sun
- Wuhan Universities, China
- PS4-2-8
- Multi-mode Vibration Suppression for Electric Machines using Passive Dynamic Vibration Absorbers Mounting on Stator Outer Peripheral
- Naho Funasaka, Makoto Isobe, and Takashi Kosaka
- Nagoya Institute of Technology, Japan
- PS4-2-9
- Vibration Reduction by Grooving on Magnets for PMSMs
- Xinbang Wang, Qiang Tan, Junhao Pian, and Jing Li
- Nanjing University of Aeronautics and Astronautics, China
- PS4-2-10
- Combined Fault Diagnosis of Stator and Rotor Windings in a PWM Inverter-fed Induction Motor Using Frequency Spectrum of Estimated Air-gap Torque
- Keita Takehana, Hideaki Hirahara, and Shu Yamamoto
- Polytechnic University, Japan
Session PS4-3Transformers and Power Apparatus
- Time:
- 12:00-13:00
- Venue:
- FIT Arena
- PS4-3-1
- Study on the Design Optimization of Cast-resin Transformer using Permutation with Repetition and Python’s Scipy Method
- JongGun Lee, WoongHee Lee, and KyoungHoon Lee
- HD HYUNDAI ELECTRIC, Republic of Korea
- PS4-3-2
- Optimal Design of Three-phase Transformer using Genetic Algorithm and FEMM
- Peter Nkwocha Harmony, Junki Park, Yujin Lee, and Jeihoon Baek
- Koreatech University, Republic of Korea
- PS4-3-3
- Additive Manufacturing Lightweight Inductor
- Tsung-Wei Chang, Po-Wei Huang, Huan-Hsuan Yeh, Cheng-Hsin Shih, and Mi-Ching Tsai
- National Cheng Kung University, Taiwan
- PS4-3-4
- Influence of Distorted Voltage and Harmonics on Highfrequency Transient Model of Transformers
- Yingying Wang, Jindi Pang, Bolin Jin, Zuhuo Liang, and Shuangli Chen
- China University of Mining and Technology, China
- PS4-3-5
- Core Loss Calculation of Nanocrystalline Highfrequency Transformer under Non-sinusoidal Excitation
- Zhiwei Sui, Wenliang Zhao, Minglei Dou, Haibo Ding, and Li Zhang
- Shandong University, China
- PS4-3-6
- Analysis of Inter-turn Short-circuit Characteristics in Single-phase Traction Transformers Based on Digital Twin
- Yikesha Halimulati1,2, Lu Zhao1, Yuang Luo1,2, Qiongxuan Ge1, Shi Cheng1,2, and Yuhang Chi1,2
- 1Chinese Academy of Sciences, China, 2University of Chinese Academy of Sciences, China
- PS4-3-7
- The Basic Study on the Optimization of Mutual Induction Circuit that Separates Zero Energy into Positive and Negative Energy
- Yoshiaki Yoshida1 and Yukio Suzuki2
- 1Hiroshima Institute of Technology, Japan, 2SEMITEC Corporation, Japan
- PS4-3-8
- A Proposal of a New Temperature Rise Test Method for Filter Reactors — Middle-frequency Test —
- Hiroaki Maeji1,2, Minoru Kuwata1,2, and Koji Fujiwara2
- 1Sumitomo Electric Industries, Ltd., Japan, 2Doshisha University, Japan
Session PS4-4Other Related Topics in Electric Machines
- Time:
- 12:00-13:00
- Venue:
- FIT Arena
- PS4-4-1
- Investigation on the Torque to Mass Ratio of Synchronous Magnetic Couplings
- Yusuf Akcay1, Oliver Tweedy2, Paolo Giangrande3, and Michael Galea4
- 1University of Sheffield, UK, 2University of Nottingham, UK, 3University of Bergamo, Italy, 4University of Malta, Malta
- PS4-4-2
- A Hybrid Spiral Stepper Motor with Staggered Punching Structure
- Wei Hao1, Rui Zhang1, Yuchao Shi2, and Liwei Song1
- 1College of Harbin Institute of Technology, China, 2Harbin Institute of Technology, China
- PS4-4-3
- Design and Optimization of Non-insulated Pipe Wall Electromagnetic Flowmeter for High-temperature Liquid Metal Flow Measurement
- Yikun LI, Jien MA, Sixian ZHU, Wenxiao WU, Lin QIU, and Youtong FANG
- Zhejiang University, China
- PS4-4-4
- Parameter Optimization Design of Magnetic Levitation Centrifugal Blood Pump Based on Parameter Sensitivity Analysis
- Kun Wang1, Ji Min Chen1, Yun Le1, Shi Qiang Zheng1, and Yin Zhang2
- 1Beihang Univ, China, 2Hangzhou Kuntai Maglev Technology Co., Ltd.
- PS4-4-5
- Energy-saving Power Transmission Device for CNC
- Baek-Ju Sung1, Jong-Bae Lee1, Do-Sik Kim1, Yong-Seon Yun2, and Yong-Hyun Kim2
- 1KIMM, Republic of Korea, 2KHANSTN, Republic of Korea
- PS4-4-6
- Detection of Slot Discharges by using On-line PD Monitoring System with a Non-contact Sensor
- Takashi Harakawa, Akira Fujimoto, Tomoaki Takahashi, and Hirotaka Tsubakihara
- Toshiba Energy Systems & Solutions Corporation, Japan
- PS4-4-7
- Analysis and Control Strategy Study of Large-scale Pumped Storage Power Station Phase Modulation Operation
- Zhangbin Yang1,2, Jiaxin Huang1,2, Daixiao Peng3, Xi Cai3, Xueguang Lian3, Hang Cai3, and Jinxiu Chen1
- 1Chinese Academy of Science, China, 2University of Chinese Academy of Sciences, China, 3China Three Gorges Corporation, China
- PS4-4-8
- Model Predictive Control with Disturbance Compensation for Trajectory Tracking of Three-degreeof-freedom Spherical Joint Actuator
- Yan Wen, Ziyang Chen, Guoli Li, Qunjing Wang, Qian Zhang, and Lufeng Ju
- Anhui University, China
- PS4-4-9
- Efficiency Improvement of Induction Motors with Novel Magnetic Slot Wedges
- Shin Noguchi, Keiko Kikuchi, Kyohei Aimuta, and Hirohisa Sano
- Proterial, Ltd., Japan
- PS4-4-10
- Improvement of Shape Memory Alloy (NiTi) Actuation Frequency Using Highly Thermally Conductive Metal Layer
- Marjan Ghorbani1, Xinxin Liao1, Sean Thomas2, Thomas Martinez1, and Yves Perriard1
- 1École Polytechnique Fédérale de Lausanne, Switzerland, 2Pennsylvania State University, USA
Session PS4-5Sensorless Control 2
- Time:
- 12:00-13:00
- Venue:
- FIT Arena
- PS4-5-1
- Improved Synchronous Demodulation Method for Three-stage Synchronous Machine Based on D-axis Response High-frequency Voltage
- Zhihui Wang, Jiadan Wei, and Le Zhang
- Nanjing University of Aeronautics and Astronautics, China
- PS4-5-2
- Improved Sensorless Control of IPMSM Drives Using Complex Bandpass Filter and Pseudolinear Enhanced PLL
- Haoyuan Yu1, Wang Bo1, Jun Huang1, and Dewen Tian2
- 1Southeast University, China, 2China North Vehicle Research Institute, China
- PS4-5-3
- Model Predictive Sensorless Control with Highfrequency Square-wave-type Voltage Synchronized with Carrier
- Takashi Mitsunaga1, Sari Maekawa1, Ryosuke Saito2, Yuki Kumakiri2, and Akira Nakazawa2
- 1Meiji University, Japan, 2Toshiba Infrastructure Systems & Solutions Corp., Japan
- PS4-5-4
- Position Sensorless Control in Low-speed Regions for Non-saliency and Concentrated Winding Motors
- Kohei Hayashi and Yoshitaka Iwaji
- Ibaraki University, Japan
- PS4-5-5
- Position Sensorless Control of Dual Three-phase PMSM Based on Improved Sliding Mode Observer
- Anchen Yang1, Mingyao Lin1, and Keman Lin2
- 1Southeast University, China, 2Hohai University, China
- PS4-5-6
- A Precise Rotor Flux Estimator for a Sensorless Dual Three-phase SPMSM
- Yilong Wang1, Bing Tian1, Cong Guo1, and Qiming Bai2
- 1Nanjing University of Aeronautics and Astronautics, China, 2Saisheng Information Technology Research Institute Jiangsu Co., Ltd., China
Session PS4-6Sensorless Control 3
- Time:
- 12:00-13:00
- Venue:
- FIT Arena
- PS4-6-1
- Effects of d-axis Inductance Change for Position Sensorless Control of SynRM at Low Velocities by Using an Extended EMF caused by High-frequency Current Superposition
- Yuto Yamamori1, Yuki Miki1, Mutuwo Tomita1, Masaru Hasegawa2, and Shinji Doki3
- 1Natl. Inst. of Tech., Gifu Coll., Japan, 2Chubu Univ., Japan, 3Nagoya Univ., Japan
- PS4-6-2
- Inductance Linearization Region-based Initial Rotor Position Estimation Method for Doubly Salient Electromagnetic Motor
- Wenjing Fang, Bo Zhou, Yijun Zhang, Xie Xie, and Xiaodong Yu
- Nanjing University of Aeronautics and Astronautics, China
- PS4-6-3
- Position Estimation for Sinusoidal Doubly Salient Electromagnetic Machine by Injecting High-frequency Current Signal into Excitation Winding
- Yang Huang, Bo Zhou, Xiaodong Yu, and Yaotian Shi
- Nanjing University of Aeronautics and Astronautics, China
- PS4-6-4
- Research on Initial Rotor Position Estimation for DSEM Based on Excitation Field Building
- Xie Xie, Bo Zhou, Wenjing Fang, Yijun Zhang, and Wenbo Zhou
- Nanjing University of Aeronautics and Astronautics, China
- PS4-6-5
- Position Sensorless Control Method for Doubly Salient Electromagnetic Machine Based on Non-conduct Phase Current Injection
- Qianqian Zhang, Zhuoran Zhang, Li Yu, Xu Chen, and Yao Sun
- Nanjing University of Aeronautics and Astronautics, China
- PS4-6-6
- Reciprocating Drive of Position Sensorless Linear Switched Reluctance Motor Based on Mathematical Model of Magnetization Curves
- Tadashi Hirayama
- Kogakuin University, Japan
Session PS4-7Motion Control and Maglev Control Systems
- Time:
- 12:00-13:00
- Venue:
- FIT Arena
- PS4-7-1
- Design of a Dynamic Compensator for Load-side Speed and Torsional Torque Controls of a Two-inertia System
- Wen Li1, Yongdan Chen2, Dong Wei1, Kan Liu1, Jing Zhou1, Tao Peng1, Wenrui Liu1, and Cong Huang1
- 1Hunan University, China, 2China North Vehicle Research Institution, China
- PS4-7-2
- Simple Design Method of Two-degree-of-freedom PID Position Controller Specifying Disturbance Response for Linear Servo Motors
- Hideaki Hirahara1, Kenshiro Kuroki2, and Shu Yamamoto1
- 1Polytechnic University, Japan, 2Okinawa Polytechnic College, Japan
- PS4-7-3
- Modeling and Optimal Control for 2-DOF Differential Robot Joint Based on Cascade Extended State Observer
- Yuheng Wang, Deliang Liang, Zhe Liang, and Yang Liang
- Xi’an Jiaotong University, China
- PS4-7-4
- Dual-redundant Electro-mechanical Actuators Force Fight Reduction Control Based on Position Sensor Fault-tolerant
- Wenrui Liang, Shoujun Song, and Xiaocan Huang
- Northwestern Polytechnical University, China
- PS4-7-5
- Vibration Suppression Method in Flexible Loads Motor Drives System based on Speed Feedback Resonance Filter
- Qiyang Zeng1, Ming Yang1, Chaoyi Shang1, Ruizhe Zhou1, Pengcheng Lan1, and Xinmei Zhang2
- 1Harbin Institute of Technology, China, 2Ningbo Anxin CNC Technology Co., Ltd., China
- PS4-7-6
- Servo System End-of-system Oscillation Suppression Based on Acceleration Limiting and Notch Filtering
- Zhiyuan Wang, Juntao Wang, and Pinjia Zhang
- Department of Electrical Engineering, China
- PS4-7-7
- Speed Regulation Strategy of Blood Pump Motor used in Hypothermic Therapy
- Kun Wang1, Shiyi Xu1, Mohan Hao1, Shiqiang Zheng1, and Yin Zhang2
- 1Beihang University, China, 2Hangzhou Kuntai Maglev Technology Co., Ltd., China
- PS4-7-8
- Servo Motor Control System Design Based on EtherCAT Real-time Communication
- Fengyang Liu, Dianguo Xu, and Qiang Gao
- Harbin Institute of Technology, China
- PS4-7-9
- Study of Robust Control Strategy for the Levitation Subsystem of Bilateral Long Primary Permanent Magnet Linear Synchronous Motor
- Shuntian Yan1, Qiang Tan1, Yingzhen Li2, and Jing Li1
- 1Nanjing University of Aeronautics and Astronautics, China, 2China Industrial Control Systems CERT, China
- PS4-7-10
- Vibration Suppression Based on Phase Shift Notch Filter for Bearingless Motor Rotor Mass Unbalance System
- Zhenglong Li, Xiaolin Wang, and Xucong Bao
- Nanjing University of Aeronautics and Astronautics, China
Session PS4-8Power Converters of Renewable Energy Systems 2
- Time:
- 12:00-13:00
- Venue:
- FIT Arena
- PS4-8-1
- A Novel Day-ahead Probability Prediction Method for PV Station Based on Improved CNN-autoformer Network
- Wenzhi Zhu1, Yixin Liu1, Li Guo1, Yanrong Li1, Xiliang Li2, and Cuigu Wu2
- 1Tianjin University, China, 2Xinte Energy Company Limited, China
- PS4-8-2
- Flexible Resource Data Acquisition and Dynamic Characterization Techniques for Virtual Power Plants with a High Percentage of New Energy Access
- Peirong Zhang1, Xiangyu Kong1, Yuan Ren1, Qingrong Zheng2, and Zhuofan Tang2
- 1Tianjin University, China, 2State Grid Shanghai Electric Power Company, China
- PS4-8-3
- Research on Reserve Capacity Planning Method for Distribution Systems Considering Uncertainty of Temperature-controlled Loads
- Longyu Zhang1, Xiangyu Kong1, Yue Guo2, Yi Song2, and Xuyang Wang2
- 1Tianjin University, China, 2State Grid Economic and Technological Research Institute Co., Ltd., China
- PS4-8-4
- A Novel Method for Optimal Capacity Configuration of the Grid-connected Wind-solar Complementary Power Generation
- Yuan Zhu and Kazuhiro Ohyama
- Fukuoka Institute of Technology, Japan
- PS4-8-5
- A Study of Dynamic Characteristics of Series-connected Wind Farm Using a Simulation Model That Can Reduce Computational Load
- Fujio Tatsuta and Shoji Nishikata
- Tokyo Denki University, Japan
- PS4-8-6
- Multi-time Scale Optimization Scheduling Model for Over-matched PV Station with Energy Storage
- Wenzhi Zhu1, Yixin Liu1, Li Guo1, Yanrong Li1, Xiliang Li2, and Cuigu Wu2
- 1Tianjin University, China, 2Xinte Energy Company Limited, China
- PS4-8-7
- A Coupled Analysis of Nonlinear Vibration Energy Harvester Based on Predictor-corrector Approach
- Takahiro Sato
- Muroran Institute of Technology, Japan
- PS4-8-8
- Machine Learning based Methodology for Fast Assessment of Battery Health Status
- Younggill Son and Woongchul Choi
- Kookmin University, Republic of Korea
- PS4-8-9
- Fleet Management on Inland Waterways for Electric Boat Ferry System
- Ma. Leonora Elizabeth O. Borromeo, Luis Jarod De Luna, Rovinna Janel C. Tayo, and Lew Andrew R. Tria
- University of the Philippines, Philippines
- PS4-8-10
- A Two-stage Sorting Method based on Deep Clustering for Retired Lithium-ion Battery Considering Static and Dynamic Consistency
- Liangliang Wei, Yiwen Sun, Hongzhang Xu, and Han Yi
- Shenzhen Campus of Sun Yat-sen University, China
Session PS4-9Power Converters of Renewable Energy Systems 3
- Time:
- 12:00-13:00
- Venue:
- FIT Arena
- PS4-9-1
- Design of the Hydroelectric Turbine Unit’s Evaporative Cooling Automatic Control System
- Zhonghua Gui1, Fucheng Han2, Weifu Lu1, Jinxiu Chen2, Hongkui Qiao1, Fei Zhang1, and Shiyue Du1
- 1Pumped-storage Research Institute, China, 2Institute of Electrical Engineering CAS, China
- PS4-9-2
- Optimized Configuration Method for Intelligent Terminals Based on Improved Bat Optimization Algorithm
- Yanyu Yan1, Xiangyu Kong1, Xudong Wang2, Yuying Ma1, and Longyu Zhang1
- 1Tianjin University, China, 2State Grid Tianjin Electric Power Company, China
- PS4-9-3
- A Distributionally Robust Optimization Scheduling Method for Cascaded Hydro-PV-storage Complementary Power System Based on Deep Learning
- Mao Liu, Xiangyu Kong, Bohao Liang, and Longyu Zhang
- Tianjin University, China
- PS4-9-4
- Advanced Method for Electricity Theft Detection: A Case Study in Low-voltage Station
- Bixuan Gao, Xiangyu Kong, and Bohao Liang
- Tianjin University, China
- PS4-9-5
- A Multi-microgrid Energy Trading Strategy to Achieve Carbon Neutrality
- Jin Gao1, Mohammadreza Lak1, and Zhenguo Shao2
- 1Yuan Ze University, Taiwan, 2Fuzhou University, China
- PS4-9-6
- Online Location Approach for Aged Segment of HVDC Cables Using Insertion Index Perturbation and Reflection Analysis
- Ziyu Wei1, Yang Wu2, Qiuqiong Lin1, and Pinjia Zhang1
- 1Tsinghua University, China, 2Aalborg University, Denmark
- PS4-9-7
- A Chance-constrainted Multi-stage Planning Method for Rural Microgrids Considering Energy Self-sustained Ability under Extreme Off-grid Scenarios
- Yixin Liu1, Yanrong Li1, Shigong Jiang2, Peng Li3, Zhongjian Liu2, and Huixuan Li3
- 1Tianjin University, China, 2State Grid Research Institute, China, 3State Grid Henan Research Institute, China
Session PS4-10Power Electronic Devices and Applications
- Time:
- 12:00-13:00
- Venue:
- FIT Arena
- PS4-10-1
- Design and Implementation of Online IGBT Junction Temperature Measurement System for Practical Application in DC/AC Converter
- Yuanxin Zhang1, Shiqi Ji1, Haoyu Wang1, Zhengming Zhao1, Jiayang Zheng1, Chunchen Li1, Chao Sheng2, and Weitao Yang2
- 1Tsinghua University, China, 2China Southern Power Grid Technology Co., Ltd., China
- PS4-10-2
- Thyristor-based Multi-port DC Solid-state Circuit Breaker Capable of Bidirectional Operation
- Boseung Kwak, Sunghyeon Park, Juwon Kim, and In-Dong Kim
- Pukyong National University, Republic of Korea
- PS4-10-3
- Development of a New Hybrid Switch with Larger DC Current Breaking Capacity and Longer Lifetime
- Daisuke Shiojima1, Takayuki Kawaguchi1, and Shuhei Kato2
- 1Sigma Energy Co., Ltd, Japan, 2Nihon University, Japan
- PS4-10-4
- Emulation of an Inter-turn Short Circuit with a Variable Fault Resistor
- Lukas Braun, Tim Becker, Enno Wagenaar, Xinyi Yu, Duc Pham, and Rik W. de Doncker
- RWTH Aachen University, Germany
- PS4-10-5
- Loss Analysis of Hybrid Switch with Minimum SiC MOSFET Conduction Modulation
- Sibao Ding, Panbao Wang, Zehua Zhang, Wei Wang, and Dianguo Xu
- Harbin Institute of Technology, China
- PS4-10-6
- Characterization of Commercial High-power SiC Modules for Loss Performance in Continuous Operational DAB Applications
- Yikang Xiao1, Shiqi Ji1, Zhengming Zhao1, Bochen Shi1, Wenhao Xie1, Mingyu Yang1, Yuanxin Zhang1, Chao Sheng2, and Weitao Yang2
- 1Tsinghua University, China, 2China Southern Power Grid Technology Co., Ltd., China
- PS4-10-7
- Reliability Analysis of Three-phase Transformer-less UPS Using SiC Devices
- Tae-Ju Lee1, Dong-Ju Lee1, and Rae-Young Kim2
- 1Kukje Electric Mfg. Co., Ltd., Republic of Korea, 2Hanyang University, Republic of Korea
- PS4-10-8
- Non-contact Measurement of Defect in the Backside of Steel Plate by Electromagnetic Force Vibration
- S.Niwa, Y. Gao, and Y. Gotoh
- Oita University, Japan
Awards
We prepare 4 categories for awards.
Award Category
- ICEMS2024 Outstanding Paper Award (with reward of 50,000 JPY)
- ICEMS2024 Excellent Paper Award (with reward of 40,000 JPY)
- ICEMS2024 Incentive Paper Award (with reward of 20,000 JPY)
- ICEMS2024 Student Paper Award
Nominees will receive an email from the secretariat by November 22.
Award ceremony will be held before the closing ceremony on November 29.
Outline of the Award and closing ceremony
- Date:
- Friday, November 29
- Time:
- 13:15-13:45
- Room:
- Room A (Main room)